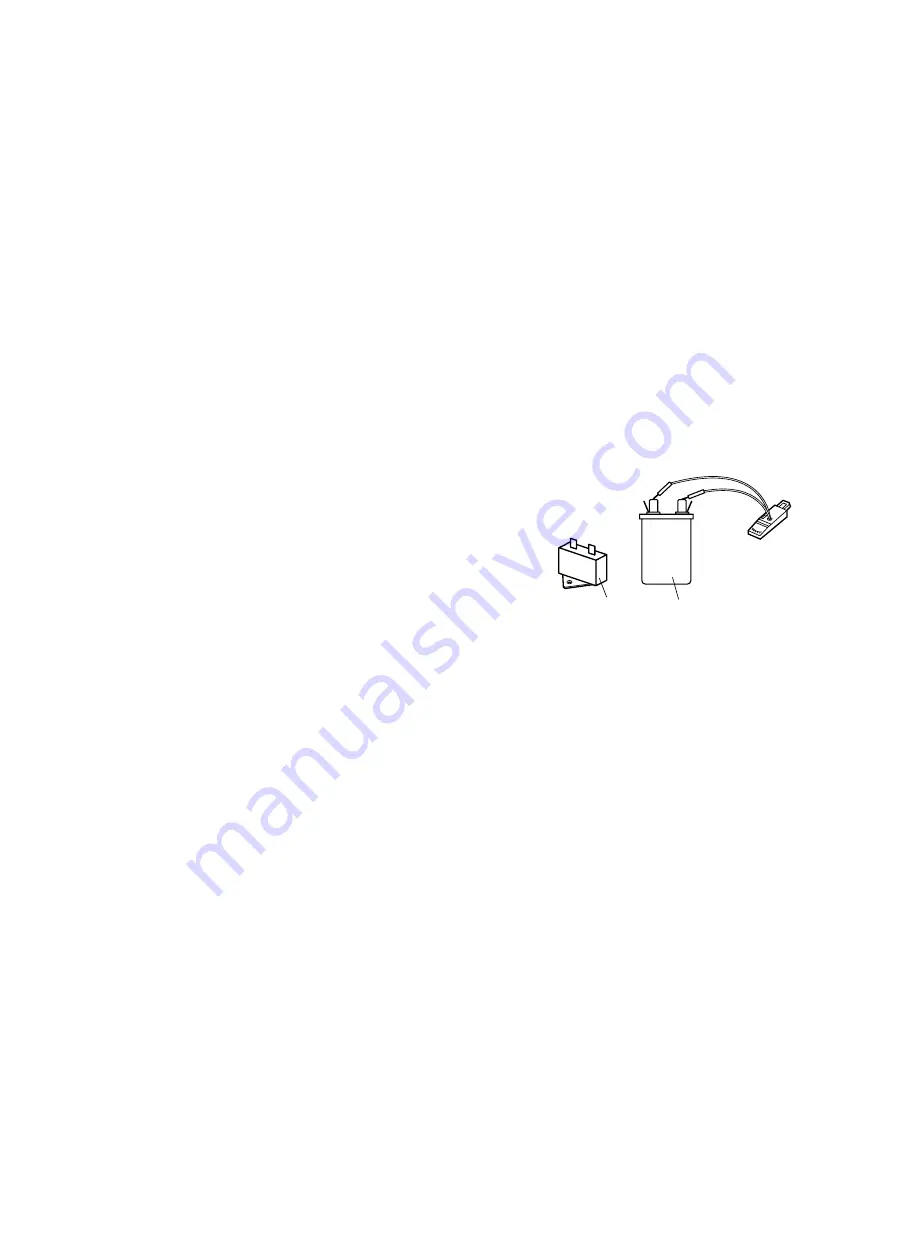
2-
3
CV10CTX
8. Leaks
Several methods are used to detect leaks in systems.
●
Electronic Leak Detectors
are very sensitive and are able to detect leaks down to 1/2 ounce per year.
A good electronic leak detector is generally far better in locating very small leaks.
●
Halide Torch
be sure the room is free from refrigerant vapours. Watch the flame for the slightest change in calor.
A very faint green indicates a small leak. The flame will be unmistakably changed to green or purple when large leaks are encountered.
To simplify leak detection pressurize the system to approximately 75 lbs.
Some leaks can be located by a visual inspection of the system components and solder joints and if oil is found at any given location it
generally is a sign that a leak exists at that point due to the fact that flame does carry oil with it travels through the system.
●
Soap Bubbles
Liquid detergents can sometimes assist in finding small leaks by brushing detergent on the suspect area and watching for bubbles.
Before applying detergent be sure that the system is pressurized.
Tap line devices are permissible for diagnosis only they are not suitable when evacuating the system. After the diagnosis has been
made they must be removed so that the system will be restored to a hermeticly sealed condition.
RUNNING CAPACITOR AND FAN CAPACITOR
NOTE: DISCHARGE THE RUNNING CAPACITOR AND FAN CAPACITOR
BEFORE TOUCHING CAPACITOR OR WIRING.
1) Discharge capacitor by shorting terminals.
2) Take the wires off the capacitor terminals.
3) Set the selector switch of a volt-ohm-meter (or a tester) on the resistance
range.
4) Connect the probes to the capacitor terminals and watch the indicator swing.
The indicator does not swing at all ..... Open.
The indicator swings but does not return ..... Shorted.
The indicator swings, then returns a moment later ..... Good.
1. Insulation test
Check the resistance between the terminals and case.
Reading must be more than 10MΩ at DC 500V.
2. Overload relay
Check continuity between terminals with volt-ohm-meter.
3. Insulation test
Check resistance between terminals and the relay case.
Reading must be more than 10MΩ at DC 500V.
4. Compressor
1) Take the wires off compressor terminals.
2) Set selector switch of volt-ohm-meter on the resistance range.
3) Put the probes on the terminals of the compressor and check continuity
between each terminal.
5. Insulation test
Check the resistance between the terminals and the copper tube.
Reading must be more than 10MΩ at DC 500V.
[2] ELECTRICAL COMPONENT TEST
RUNNING CAPACITOR
FAN CAPACITOR