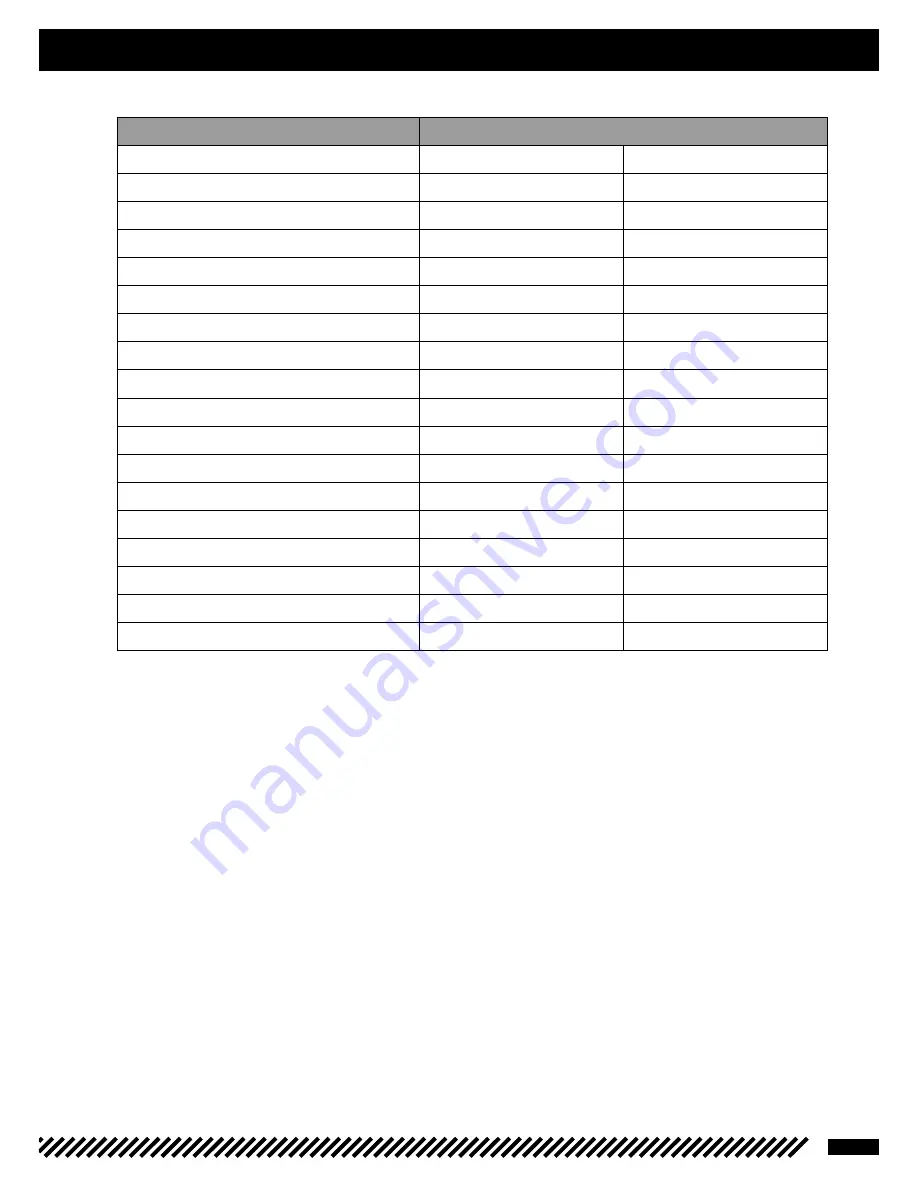
45
TIGHTENING TORQUE TABLE
Engine torques
Loctite
Speed sensor screw
8 Nm
•
Coolant drain screw
10 Nm
Oil level screw
6 Nm
Clutch slave cylinder mounting screws
9 Nm
Cylinder head (using a crossing pattern)
25 Nm
Crankcase drain plug
8 Nm
Clutch pressure plate screws
10 Nm
Water pump mounting screws
10 Nm
Flywheel nut
60 Nm
•
Clutch hub nut
100 Nm
•
Primary drive nut
150 Nm
•
Ignition cover screws
10 Nm
Central housing screws
10 Nm
Intake manifold screws
10 Nm
•
Starter motor triangle plate mounting screws
10 Nm
Starter motor bolts
10 Nm
Cylinder mounting screws
40 Nm
Transmission sprocket nut
150 Nm
•
Summary of Contents for 250 SE-R 2017
Page 1: ...MANUEL D ATELIER I WORKSHOP MANUAL I MANUAL DE TALLER ...
Page 49: ...49 WIRINGDIAGRAMS Main harness 6517 ...
Page 50: ...250 300 SE R 50 WIRINGDIAGRAMS ...
Page 51: ...51 WIRINGDIAGRAMS Lighting harness 250 SE R 300 SE R ...
Page 52: ...250 300 SE R 52 WIRINGDIAGRAMS Lighting harness Racing 250 SE R 300 SE R ...
Page 53: ...53 WIRINGDIAGRAMS Wiring harness accessories ...
Page 54: ......