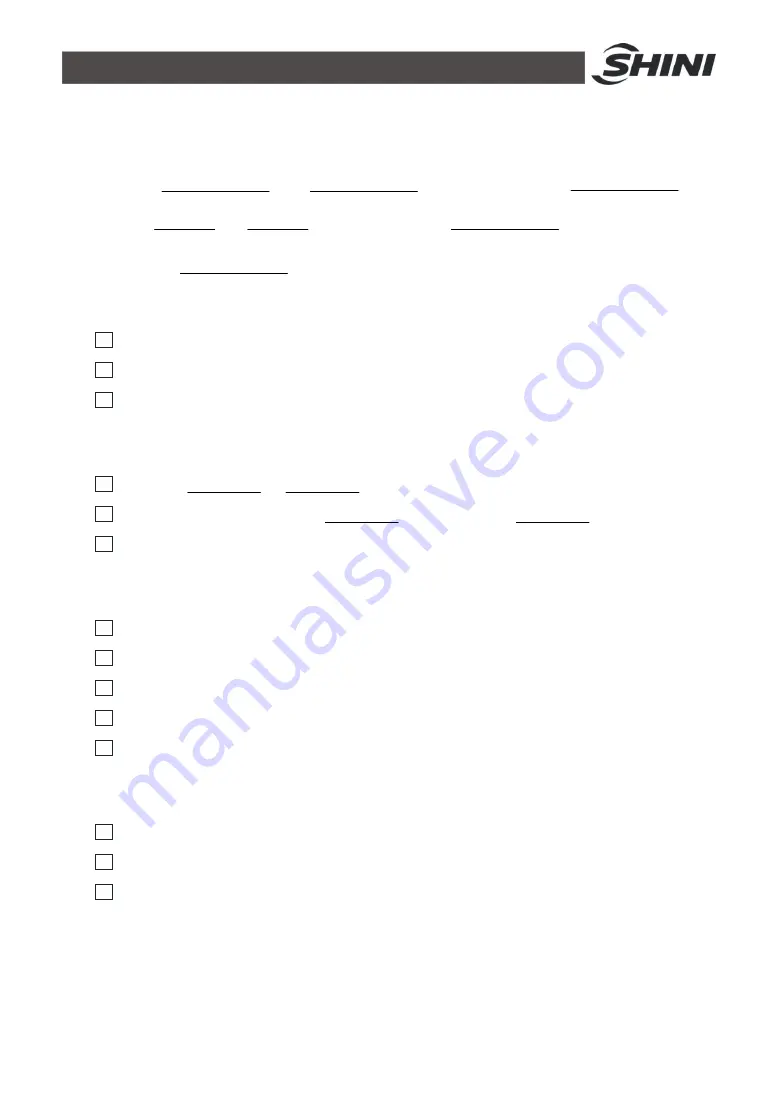
41(42)
6.3 Maintenance Schedule
6.3.1 About the Machine
Model SN Production date
Voltage
Ф
V Frequency Hz
Total power kW
6.3.2 Check after Installation
Check the pipes are all correctly connected.
Check if there are leakages in the piping system.
Check if there are breaks in welding joint.
Electrical Installation
Voltage: V Hz
Fuse specification: 1 Phase A 3 Phase A
Check phase sequence of power supply.
6.3.3 Daily Checking
Check switch functions.
Check all the electrical wires.
Check whether pressure gauges are accurate.
Check whether compressor temperature is normal.
Check whether cooling water circulation is normal.
6.3.4 Weekly Checking
Check electrical connections.
Check protection & alarm function of the water chiller.
Check whether set point of high-low pressure switch is normal.
6.3.5 Montly Checking
Summary of Contents for SIC-10W
Page 1: ...SIC W Water cooled Water Chillers Date Mar 2022 Version Ver D English ...
Page 2: ......
Page 35: ...35 42 6 Repair and Maintenance ...
Page 36: ...36 42 ...