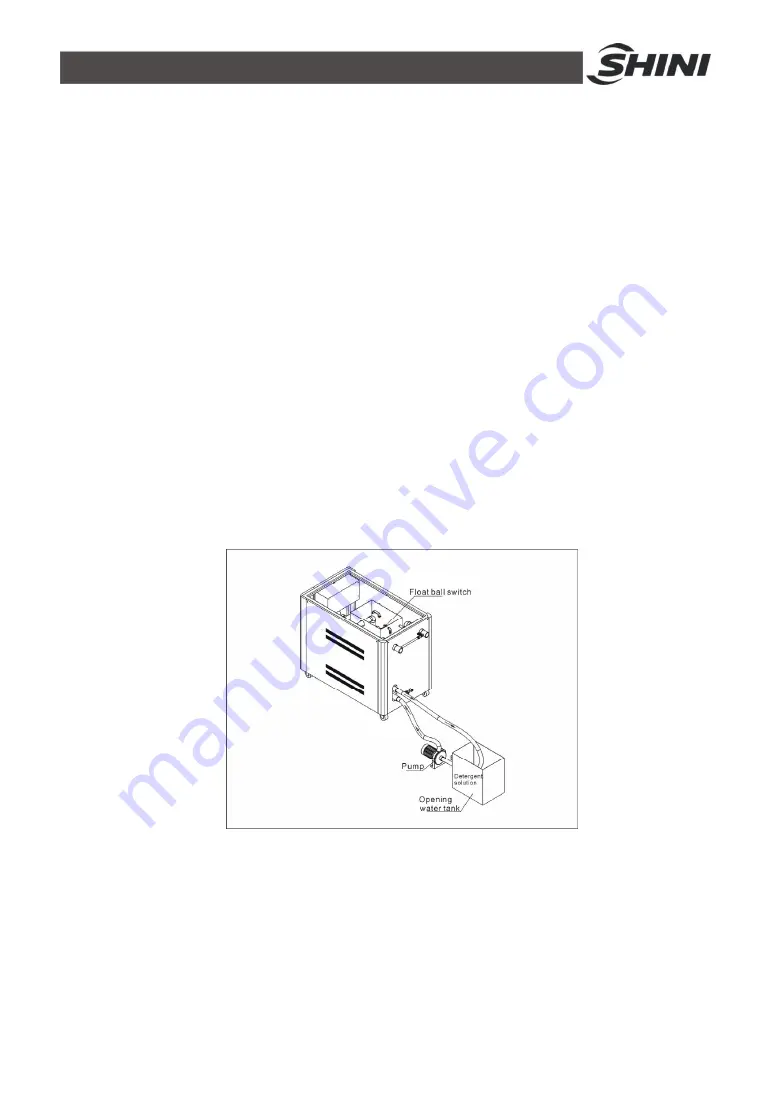
45(49)
6.2 Components Maintenance
6.2.1 Condenser
A. Water-cooled series
SIC-W-R2 series water chiller adopts tube-in-shell condenser which may have
incrustations piled up in the inner side of its heat pipe or sundries caused by bad
water treatment. All these will influence the heat emission effect, so it is
necessary to clean the condenser at fixed periods to ensure its good working
performance.
If water treatment had been on to the cooling water, it is suggested that firstly
use hydrogen peroxide for sterilization and then use high pressure air rifle to
clean it and check whether there is still incrustation. If the cooling water had not
be put under the water treatment, citric acid or sulfamic acid together with
corrosion inhibitor is suggested to clean the condenser, after that use high
pressure air rifle to clean it, and it is necessary to use passivator after the
acid-washing.
Tube-in-shell Condenser Cleaning
:
1. Ensure the float ball in water tank of the machine is closed, to prevent the
detergent solution from getting into the water tank of the machine.
2. Connect pipeline with hoses according to above picture.
3. Detergent and water (according to purchased detergent mixing requirement
for specific proportion) proportional to solution and pour into the opening
water tank, then start-up pump cleaning.
Summary of Contents for SIC-A-R2
Page 2: ......
Page 6: ...6 49...
Page 40: ...40 49 6 Maintenance and Repair A Water cooled Series...
Page 41: ...41 49...
Page 42: ...42 49 B Air cooled Series...