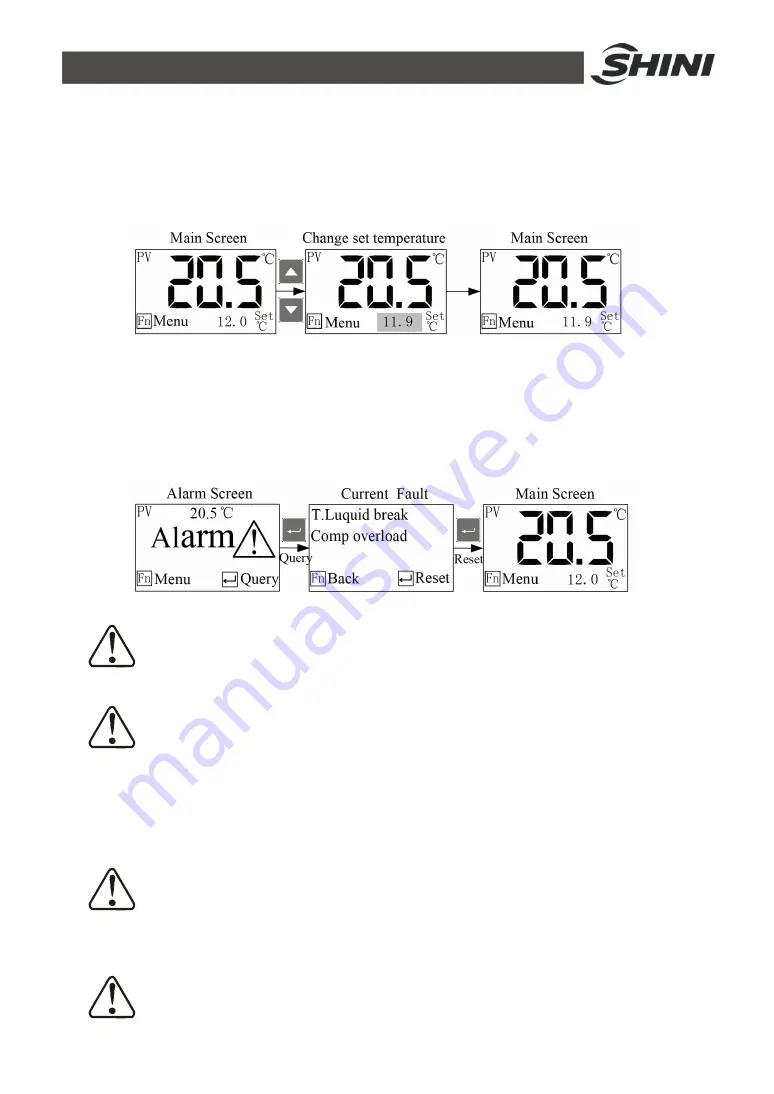
26(40)
4.3 Quick Operation
1. Changing and Setting Temperature
If the user parameter [Lock Temp.] is set to "No", the setting temperature can be
modified directly in the main screen, with operation details as follows:
Note: the setting temperature can also be modified in the user parameters.
2. Query/Reset Fault
In case of fault, the alarm screen will automatically pop up. The operation details
of query and reset faults are as follows:
Attention!
Pump rotating direction should be correct.
Attention!
Before starting the system, make sure that cooling water pump is turned
on. Check the water tank of the chiller. Do not start the machine when
there is no water left in water tank. We shall not be liable for any damages
caused by this reason.
Attention!
In order to reduce the possibilities of machine damage and prolong the
life, start the machine with correct methods.
Attention!