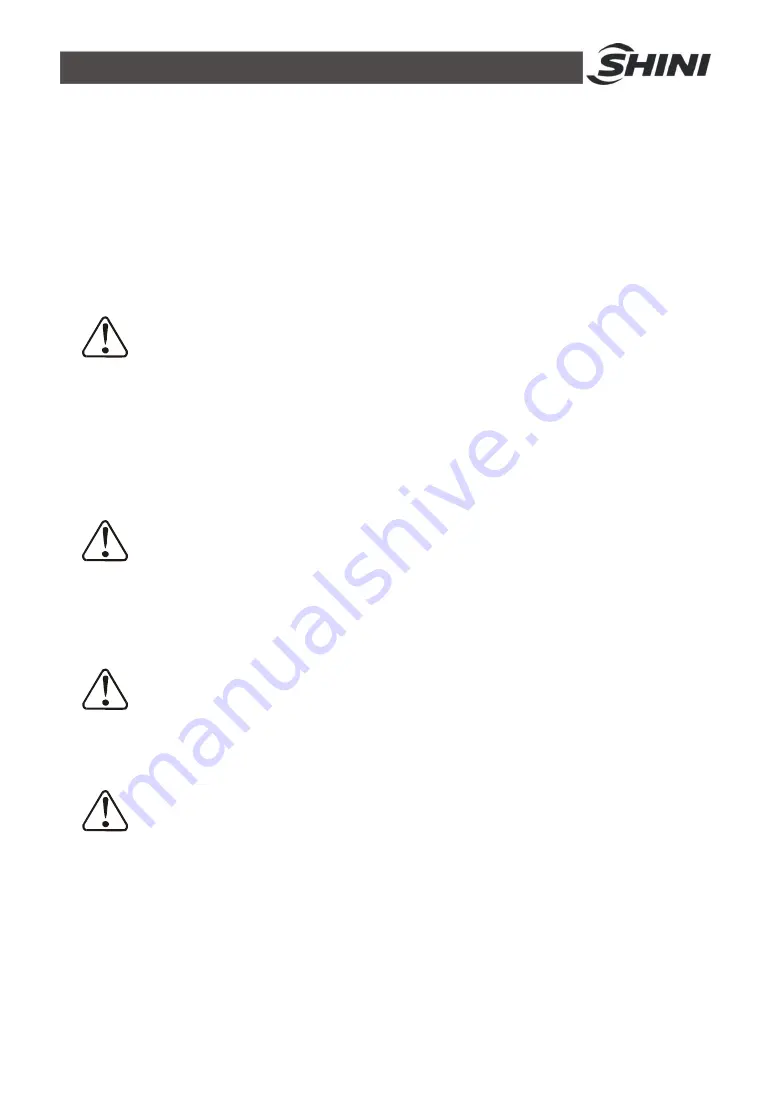
23(142)
the robot will stop working and alarm. When the pressure up to 6bar, It will
affect the service life of pneumatic components.
Compressed air consumption depends on the robot accessories.
2.3
Electrical Connection
2.3.1 Main Power Supply
The power requirements are given on the serial plate of the robot, the
power connection is provided through cable conductor and CEE plug.
The power connection should be performed only by an authorized
electrician and according to applicable electric utility regulations.
2.3.2 Interface with the Injection Molding Machine
The robot is equipped with standard electrical interfaces according to
Euromap12 and Euromap67.
Connection of the interface plug to the machine and testing of all signals
must be done by a specialist in injection molding machines and robots.
Preferably, this should be done by one of our service engineers together
with a qualified service engineer for the injection molding machine.
The interface signal functions must be carefully tested, as improper
operation may cause malfunction or damage to the robot and molding
machine.
In particular, the functions of the safety circuits must be thoroughly
checked.
●
Testing the emergency stop signals to and from the IMM.
●
When press the emergency stop switch on hand controller, the error
message emergency stop must also be indicated at the IMM. And when
press the emergency stop on IMM, the emergency stop signal must also be
indicated at the robot.
Summary of Contents for ST1-S
Page 1: ...ST1 S User Manual Date May 2016 Vision V1 0 English ...
Page 2: ......
Page 10: ...10 142 ...
Page 94: ...94 142 7 Assembly Diagram 7 1 Traverse Unit ST1 S and ST1 T S Picture 7 1 ...
Page 99: ...99 142 7 2 Vertical Unit ST1 S Picture 7 2 ...
Page 102: ...102 142 7 3 Main Arm Unit ST1 S Picture 7 3 ...
Page 105: ...105 142 7 4 Sub arm Unit ST1 S Picture 7 4 ...
Page 108: ...108 142 7 5 Main Arm ST1 T S Picture 7 5 ...
Page 110: ...110 142 7 6 Sub arm ST1 T S Picture 7 6 ...
Page 113: ...113 142 7 7 Vertical ST1 T S Picture 7 7 ...
Page 115: ...115 142 7 8 Traverse Unit ST1 T S Middle Telescopic Arm Picture 7 8 ...
Page 119: ...119 142 7 9 Main Arm ST1 T S Middel Telescopic Arm Picture 7 9 ...
Page 123: ...123 142 7 10 Sub arm ST1 T S Middel Telescopic Arm Picture 7 10 ...
Page 127: ...127 142 7 11 Crosswise Unit ST1 T S Middle Telescopic Arm Picture 7 11 ...
Page 131: ...131 142 8 1 2 The Panasonic Servo Motor and Servo Driver Wiring Diagram Picture 8 2 ...
Page 132: ...132 142 8 1 3 The Panasonic Servo Motor and I O Board Wiring Diagram Picture 8 3 ...
Page 133: ...133 142 8 1 4 The Delta Servo Motor and Servo Driver Wiring Diagram Picture 8 4 ...
Page 134: ...134 142 8 1 5 The Delta Servo Motor and I O Board Wiring Diagram Picture 8 5 ...
Page 135: ...135 142 8 1 6 The Cuinsico Servo Motor and Servo Driver Wiring Diagram Picture 8 6 ...
Page 136: ...136 142 8 1 7 The Cuinsico Servo Motor and I O Board Wiring Diagram Picture 8 7 ...
Page 137: ...137 142 8 1 8 Z axis I O Board Wiring Diagram Picture 8 8 ...
Page 138: ...138 142 8 1 9 Main Arm Wiring Diagram Picture 8 9 ...
Page 139: ...139 142 8 1 10 Sub arm Wiring Diagram Picture 8 10 ...
Page 140: ...140 142 8 1 11 Main Arm Output Wirng Diagram Picture 8 11 ...
Page 141: ...141 142 8 1 12 Signals Input Wiring Diagram Picture 8 12 ...
Page 142: ...142 142 8 1 13 Signals Output Wiring Diagram Picture 8 13 ...