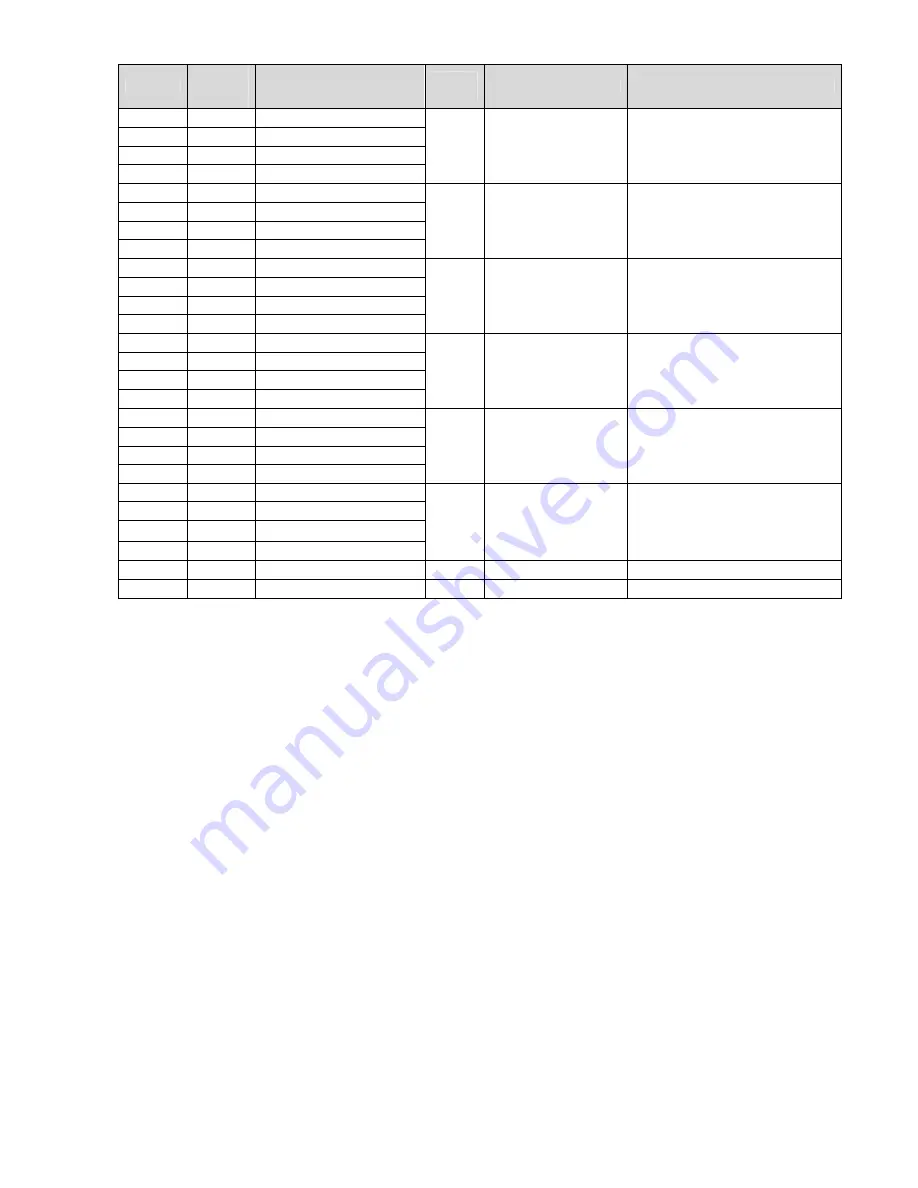
98
Address
Relative
address
(HEX)
Name
Arrange
ment
Description
Remarks
30131
82 Unit (1/4)
30132
83 Unit (2/4)
30133
84 Unit (3/4)
30134
85 Unit (4/4)
CH01
Current unit
30135
86 Unit (1/4)
30136
87 Unit (2/4)
30137
88 Unit (3/4)
30138
89 Unit (4/4)
CH02
Current unit
30139
8A Unit (1/4)
30140
8B Unit (2/4)
30141
8C Unit (3/4)
30142
8D Unit (4/4)
CH03
Current unit
30143
8E Unit (1/4)
30144
8F Unit (2/4)
30145
90 Unit (3/4)
30146
91 Unit (4/4)
CH04
Current unit
30147
92 Unit (1/4)
30148
93 Unit (2/4)
30149
94 Unit (3/4)
30150
95 Unit (4/4)
CH05
Current unit
30151
96 Unit (1/4)
30152
97 Unit (2/4)
30153
98 Unit (3/4)
30154
99 Unit (4/4)
CH06
Current unit
30155
9A Reserve
・・・
・・・
8.3.5 Reading from or Writing to the Holding Register Area
The holding register area is a read-write area. Parameter settings and the start and stop
command of the recording state are mapped. For read, specify the start address (relative) and
data count (assuming that one word is two bytes) of the data to be read. For write, specify the
start address and the data to be written.
For details, see the separate ”RM10C HYBRID RECORDER COMMUNICATION COMMAND
INSTRUCTION MANUAL (HXPRM10mnC0005E) ”.