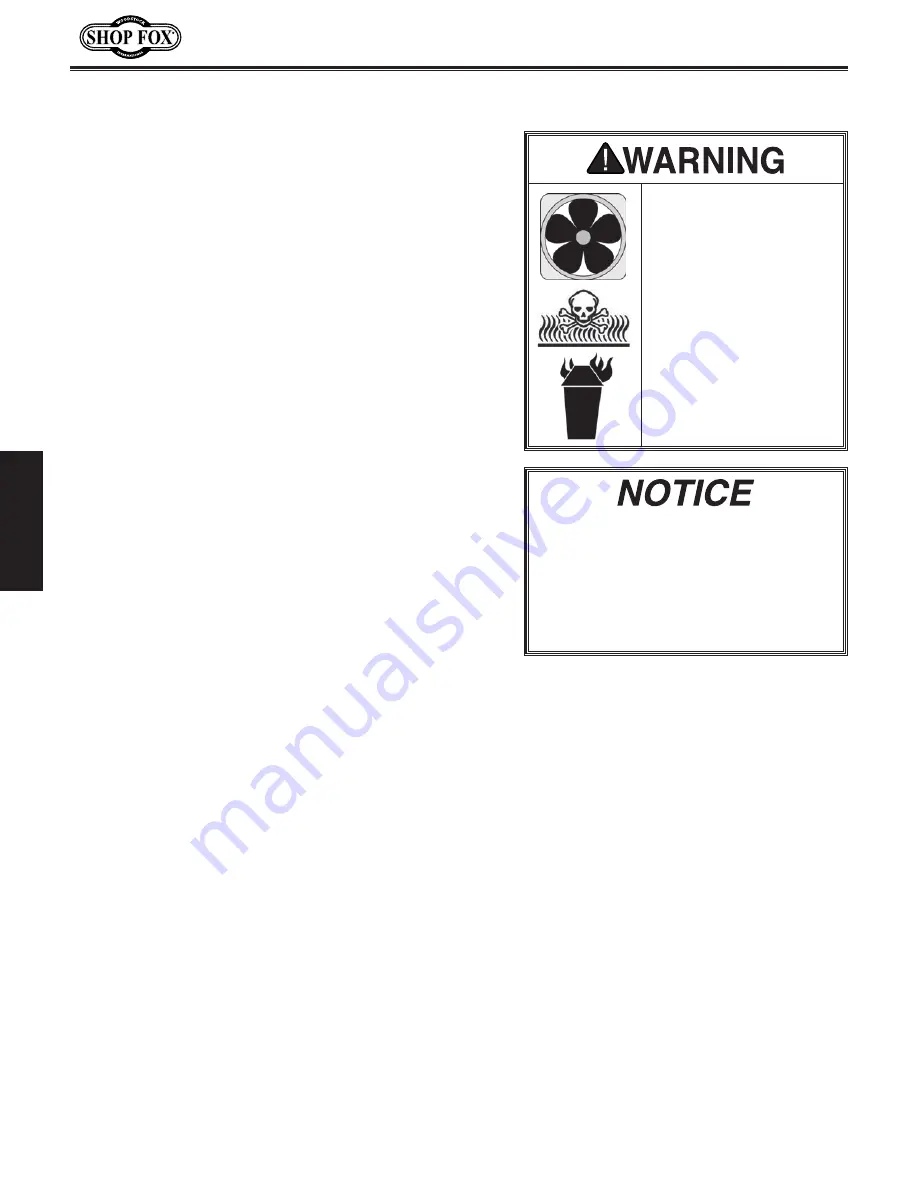
-12-
Model M1117 (For Machines Mfd. Since 9/21)
SE
TU
P
To prevent corrosion during shipment and storage of your
machine, the factory has coated the bare metal surfaces
of your machine with a heavy-duty rust prevention
compound.
If you are unprepared or impatient, this compound can
be difficult to remove. To ensure that the removal of this
coating is as easy as possible, please gather the correct
cleaner, lubricant, and tools listed below:
• Cleaner/degreaser designed to remove storage wax
and grease
• Safety glasses & disposable gloves
• Solvent brush or paint brush
• Disposable Rags
To.remove.rust.preventative.coating,.do.these.steps:
1.
DISCONNECT MACHINE FROM POWER!
2.
Put on safety glasses and disposable gloves.
3.
Coat the rust preventative with a liberal amount of
cleaner/degreaser, then let it soak for 5–10 minutes.
4.
Wipe off surfaces. If your cleaner/degreaser is
effective, the coating will wipe off easily.
Tip:
An easier way to clean off thick coats of rust
preventative from flat surfaces is to use a PLASTIC
paint scraper to scrape off the majority of the
coating before wiping it off with your rag. (Do
not use a metal scraper or you may scratch your
machine.)
5.
Repeat
cleaning steps as necessary until all of the
compound is removed.
6.
To prevent rust on freshly cleaned surfaces,
immediately coat with a quality metal protectant.
Gasoline.and.petroleum.
products.have.low.flash.
points.and.can.explode.
or.cause.fire.if.used.to.
clean.machinery..Avoid.
using. these. products.
to. clean. machinery..
Many. cleaning. solvents.
are. toxic. if. inhaled..
Minimize. your. risk.
by. only. using. these.
products. in. a. well.
ventilated.area.
In. a. pinch,. automotive. degreasers,.
mineral. spirits. or. WD•40. can. be. used.
to. remove. rust. preventative. coating..
Before. using. these. products,. though,.
test.them.on.an.inconspicuous.area.of.
your. paint. to. make. sure. they. will. not.
damage.it.
Cleaning.Machine
Summary of Contents for M1117
Page 40: ......