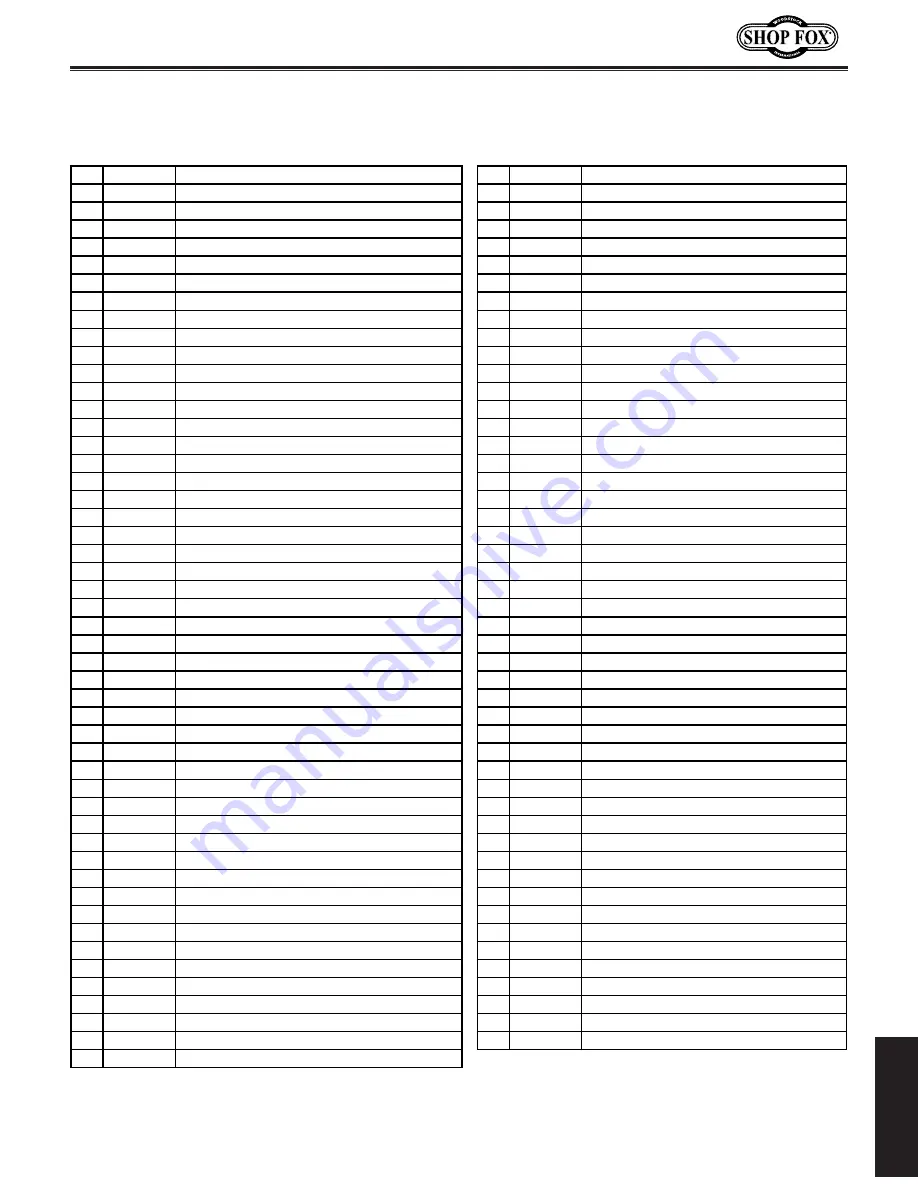
-41-
Model W1836 (For Machines Mfd. Since 04/15)
PA
RT
S
Main.Parts.List
REF PART #
DESCRIPTION
REF PART #
DESCRIPTION
1
X1836001 FLAT WASHER 4MM
55
X1836055 TAP SCREW M3 X 8
2
X1836002 PHLP HD SCR M4-.7 X 8
57
X1836057 HINGE PIN
3
X1836003 SET SCREW M6-1 X 12
58
X1836058 ACCESS DOOR
4
X1836004 HANDWHEEL 59MM, HOLE: M20-1.5 LH
59
X1836059 ROUND KNOB M8-1.25
5
X1836005 PHLP HD SCR M4-.7 X 10
60
X1836060 KNOCKOUT BAR M8-1.25 X 10, 270L
6
X1836006 PHLP HD SCR M4-.7 X 6
61
X1836061 HINGE
7
X1836007 BELT COVER HINGE
62
X1836062 ACCESS DOOR RELEASE KNOB
8
X1836008 HEX NUT M4-.7
63
X1836063 V-BELT 270J3
9
X1836009 BELT COVER
64
X1836064 HEX BOLT M8-1.25 X 90
10
X1836010 BELT COVER CLIP
65
X1836065 COMPRESSION SPRING 1 X 14 X 85
11
X1836011 SPINDLE PULLEY
66
X1836066 LOCK NUT M8-1.25
12
X1836012 SPACER
67
X1836067 LATHE BODY
13
X1836013 BALL BEARING 6005ZZ
68
X1836068 MOTOR PULLEY
14
X1836014 INT RETAINING RING 47MM
69
X1836069 CAP SCREW M6-1 X 16
15
X1836015 SHAFT M8-1.25 X 8, 45L
70
X1836070 LOCK WASHER 6MM
16
X1836016 SPINDLE LOCK KNOB
71
X1836071 FLAT WASHER 6MM
17
X1836017 ROLL PIN 3 X 12
72
X1836072 MOTOR MOUNT PLATE
18
X1836018 INDEX PIN SLEEVE M16-1.5 X 20
73
X1836073 FENDER WASHER 8MM
19
X1836019 COMPRESSION SPRING
74
X1836074 MOTOR 3/4 HP 110V 1-PH
20
X1836020 INDEX PIN
75
X1836075 SHOP FOX PADDLE SWITCH 110V
21
X1836021 CAP SCREW M8-1.25 X 30
76
X1836076 SWITCH BOX COVER
22
X1836022 LOCK WASHER 8MM
77
X1836077 TAP SCREW M3 X 10
23
X1836023 FLAT WASHER 8MM
78
X1836078 POWER CORD 18G 3W 72" 5-15P
25
X1836025 POINTER
79
X1836079 SWITCH BOX
27
X1836027 WORK LIGHT
80
X1836080 STRAIN RELIEF PG7 TYPE-3
28
X1836028 TOOL REST 148L (POST 16 X 75)
81
X1836081 STRAIN RELIEF PG9 TYPE-3
29
X1836029 EXT RETAINING RING 10MM
82
X1836082 MOTOR CORD 18G 3W 16"
30
X1836030 TOOL REST CAM FOLLOWER M10-1.25 X 30
83
X1836083 CARBON BRUSH COVER
31
X1836031 SHOULDER SCREW M5-.8 X 6, 6 X 8
84
X1836084 CARBON BRUSH 2-PC SET
32
X1836032 COMPRESSION SPRING
86
X1836086 LOCK PLATE
33
X1836033 ADJUSTABLE HANDLE
87
X1836087 LOCK NUT M10-1.5
34
X1836034 LOCK BOLT M8-1.25 X 18, INT THREAD M5-.8
88
X1836088 RUBBER FOOT
35
X1836035 TOOL REST BASE
89
X1836089 CORD WRAP MOUNT
36
X1836036 BUSHING
90
X1836090 PHLP HD SCR M5-.8 X 12
37
X1836037 TOOL REST LOCK LEVER
91
X1836091 FLAT WASHER 5MM
38
X1836038 SPUR CENTER MT#2
92
X1836092 SHOULDER SCREW M6-1 X 10, 7 X 44
39
X1836039 FACEPLATE 80MM, HOLE: M25-3
93
X1836093 HANDWHEEL HANDLE 50MM
40
X1836040 GEAR 24T
94
X1836094 HANDWHEEL 82MM, HOLE: 15MM
41
X1836041 GEAR COVER PLATE
95
X1836095 TAILSTOCK LOCK LEVER
42
X1836042 SPINDLE
96
X1836096 TAILSTOCK CAM FOLLOWER M8-1.25 X 30
45
X1836045 HEX NUT M3-.5
98
X1836098 TAILSTOCK
46
X1836046 RPM SENSOR MOUNTING PLATE
99
X1836099 TAILSTOCK LEADSCREW
47
X1836047 FLAT WASHER 3MM
100 X1836100 CARBON BRUSH HOLDER
48
X1836048 PHLP HD SCR M3-.5 X 12
101 X1836101 QUILL
49
X1836049 DIGITAL READOUT LABEL
102 X1836102 TOOL RACK
50
X1836050 PHLP HD SCR M4-.7 X 12
103 X1836103 LIVE CENTER MT#2
51
X1836051 LATHE CARRYING HANDLE
108 X1836108 CAP SCREW M8-1.25 X 16
52
X1836052 COTTER PIN 3/8-1/2 X 1-5/8 HAIRPIN
109 X1836109 PHLP HD SCR M4-.7 X 20
53
X1836053 DIGITAL READOUT COVER
116 X1836116 CIRCUIT BOARD DZ-236A1
54
X1836054 DIGITAL READOUT WP0011A-01