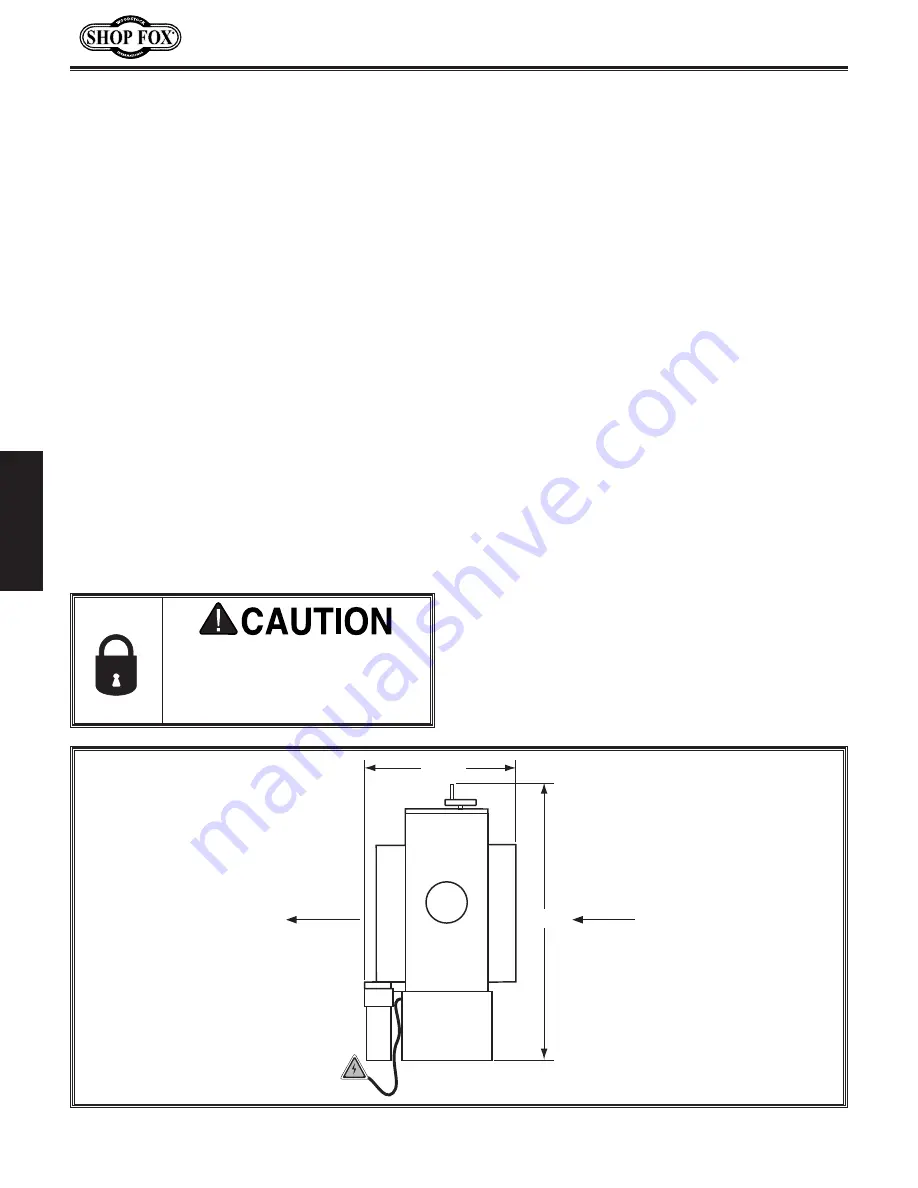
-14-
Model W1854 (For Machines Mfd. Since 02/18)
SE
TU
P
Machine.Placement
Weight.Load
Refer to the
Machine.Specifications
for the
weight of your machine. Make sure that the
surface upon which the machine is placed will
bear the weight of the machine, additional
equipment that may be installed on the
machine, and the heaviest workpiece that will
be used. Additionally, consider the weight of
the operator and any dynamic loading that may
occur when operating the machine.
Space.Allocation
Consider the largest size of workpiece that
will be processed through this machine and
provide enough space around the machine
for adequate operator material handling or
the installation of auxiliary equipment. With
permanent installations, leave enough space
around the machine to open or remove doors/
covers as required by the maintenance and
service described in this manual.
See.below.for.
required.space.allocation.
Physical.Environment
The physical environment where your machine is
operated is important for safe operation and the
longevity of its components. For best results,
operate this machine in a dry environment
that is free from excessive moisture, hazardous
chemicals, airborne abrasives, or extreme
conditions. Extreme conditions for this type
of machinery are generally those where the
ambient temperature range exceeds 41°–104°F;
the relative humidity range exceeds 20–95%
(non-condensing); or the environment is subject
to vibration, shocks, or bumps.
Electrical.Installation
Place this machine near an existing power
source. Make sure all power cords are protected
from traffic, material handling, moisture,
chemicals, or other hazards. Make sure to leave
access to a means of disconnecting the power
source or engaging a lockout/tagout device.
Lighting
Lighting around the machine must be adequate
enough that operations can be performed
safely. Shadows, glare, or strobe effects that
may distract or impede the operator must be
eliminated.
Children. or. untrained. people.
may.be.seriously.injured.by.this.
machine..Only.install.in.an.access.
restricted.location.
Figure.3.
Working clearances.
22
1
⁄
2
"
35
1
⁄
2
"
(Ensure adequate outfeed distance)
(Ensure adequate infeed distance)
Feed Direction
Feed Direction
Summary of Contents for W1854
Page 53: ...Model W1854 For Machines Mfd Since 02 18 ...
Page 56: ......