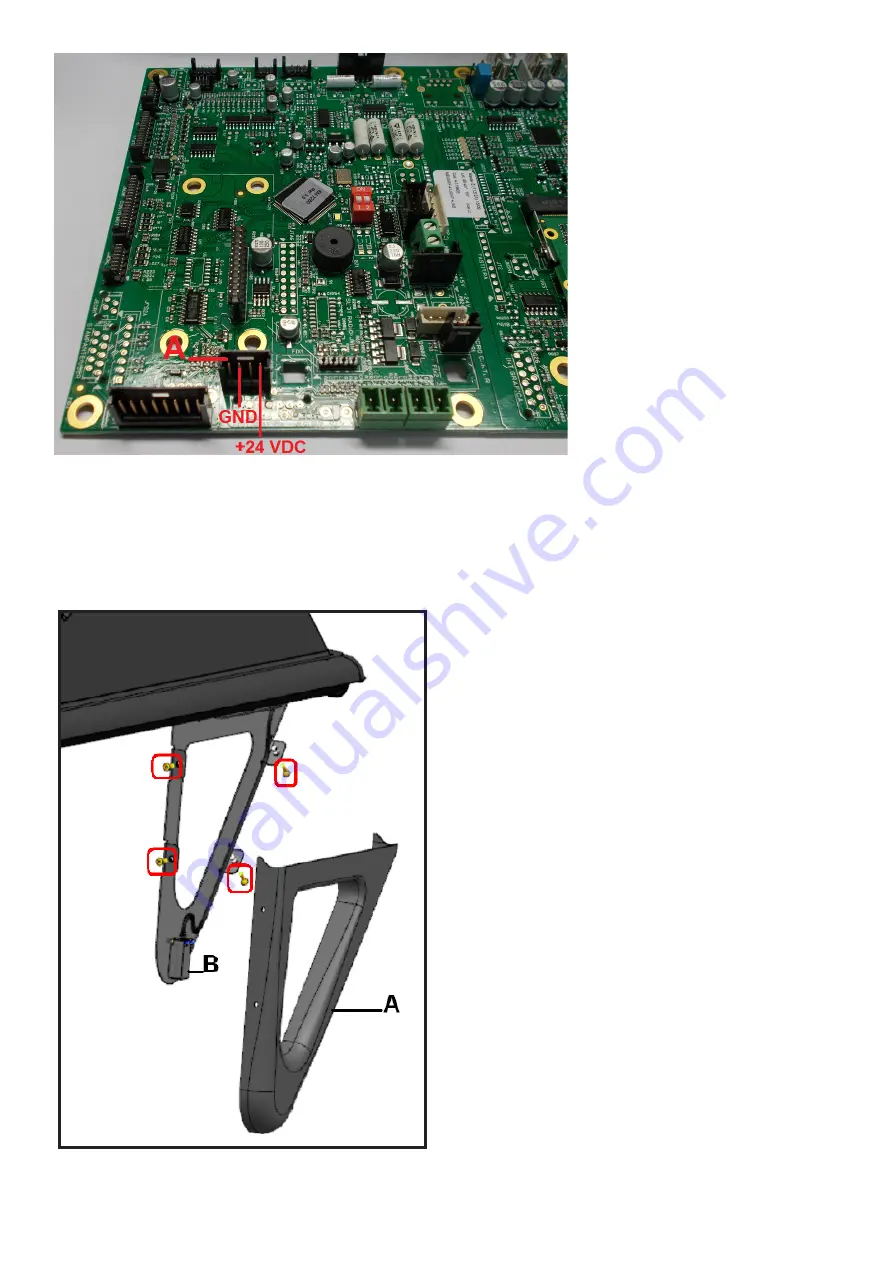
Fig. 8a
If the values are not correct, repeat sensor calibration as described in the user and maintenance manual.
If the sensor needs to be replaced, proceed as follows:
-
Remove the plastic cover (A, Fig. 8b), undoing the four fastener screws, see figure 8b.
-
Remove the ultrasonic sensor (B, Fig. 8b), undoing the two screws fastening it to the metal mount, then undo the ring nut of the
connector connected to the sensor.
-
Fit the new sensor, reversing the order of the operations used for removal.
Fig.8b
Summary of Contents for S 64E
Page 43: ...Fig 20 fig 21...
Page 45: ......
Page 46: ...SECOND VERSION OF PNEUMATIC SYSTEM from April 2016...
Page 47: ...THIRD VERSION OF PNEUMATIC SYSTEM from March 2017...
Page 48: ...FOURTH VERSION OF PNEUMATIC SYSTEM...
Page 50: ...PEAL 32F...
Page 51: ......
Page 52: ...MBUGRF 2 LIGHT...
Page 53: ......
Page 54: ...COMIM Cod 4 119446B_EN 05 2018...