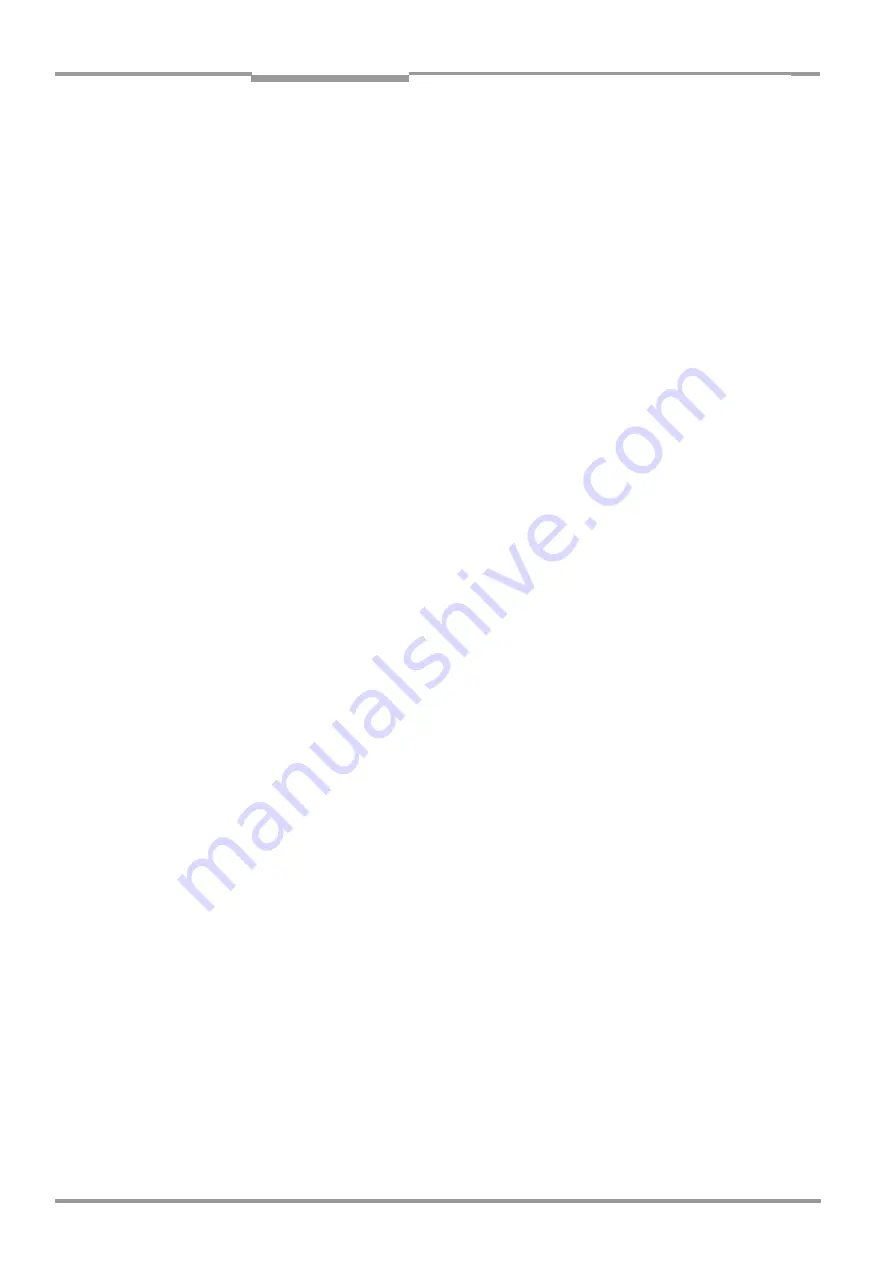
Chapter
3
Operating instructions
ICR 84x Image Code Reader
3-2
©
SICK AG · Division Auto Ident · Germany · All rights reserved
8 010 961/0000/10-05-2005
Product description
3.1.3
System requirements
The following are required to start up and operate the ICR:
Electrical connecting:
1.
A SICK connection module for power supply of the ICR (15 to 30 V DC) and connection
of the data and functional interfaces.
Available types:
– CDB 420-001 (no. 1 023 885) for 10 to 30 V DC, enclosure rating max. IP 65
– CDB 420-101 (no. 1 024 305) for 10 to 30 V DC, enclosure rating max. IP 65
– CDM 420-0001 (no. 1 025 362) for 10 to 30 V DC, enclosure rating max. IP 65
– or –
Alternatively, a non-SICK power supply unit with a voltage output of 15 to 30 V DC
(functional extra-low voltage pursuant to IEC 364-4-41) and at least
12 W
power
output.
Use cable no. 6 010 137 with 15-pin D-Sub HD socket and one open end for
connecting the ICR to the power supply unit.
2.
The following operating voltages/power output values
– CDB 420-001: 10 to 30 V DC, pursuant to IEC 364-4-41, at least 10 W
– CDM 420-0001: 10 to 30 V DC, pursuant to IEC 364-4-41, at least 10 W.
100 to 250 V AC, 50 to 60 Hz when using the CMP 400 Power Supply Module
– If the following modules are additionally built-in in the
CDB 420
module:
CMC 400 Connection Module Cloning: 10 to 30 V DC, additionally 0.5 W
– If the following modules are additionally built-in in the
CDM 420
module:
CMC 400 Connection Module Cloning: 10 to 30 V DC, additionally 0.5 W
CMD 400 Connection Module Display:
18
to 30 V DC, additionally 1 W
CMF 400 Connection Module Fieldbus:
18
to 30 V DC, additionally 2 W
3.
With external clock pulse (start/stop of reading interval) supply via the “Sensor 1“
switching input: a suitable reading pulse sensor for signaling the presence of an object
with a bar code, e. g. a photoelectric reflex switch.
4.
With optional external clock pulse (stop of reading interval) supply via the “Sensor 2“
switching input: a suitable reading pulse sensor for signaling the end of reading intervall,
e. g. a photoelectric reflex switch.
5.
If an external field illumination is necessary: a suitable light source to be connected to
the “Result 1“ switching output.
6.
To delay the external reading pulse using a track controll: a suitable incremental
encoder.
7.
A higher-level computer (host) with a data interface of type RS 422/485 or RS 232.
8.
To connect the ICR to the Profibus DP and the DeviceNet: the corresponding CMF 400
Connection Module Fieldbus (Operating instructions see
“Supplementary documentation“, Page 10-44
9.
For connection of the ICR to the CAN bus: the operating instructions “Using the CAN
interface“ (no. 8 009 180, English).
Starting-up and configuring:
10. A PC (at least 80486, 66 MHz, 16 MB RAM, CD ROM drive, serial interface, mouse
(recommended) with Windows 95
TM
/98
TM
, Windows NT4.0
TM
, Windows 2000
TM
or
Windows XP
TM
).