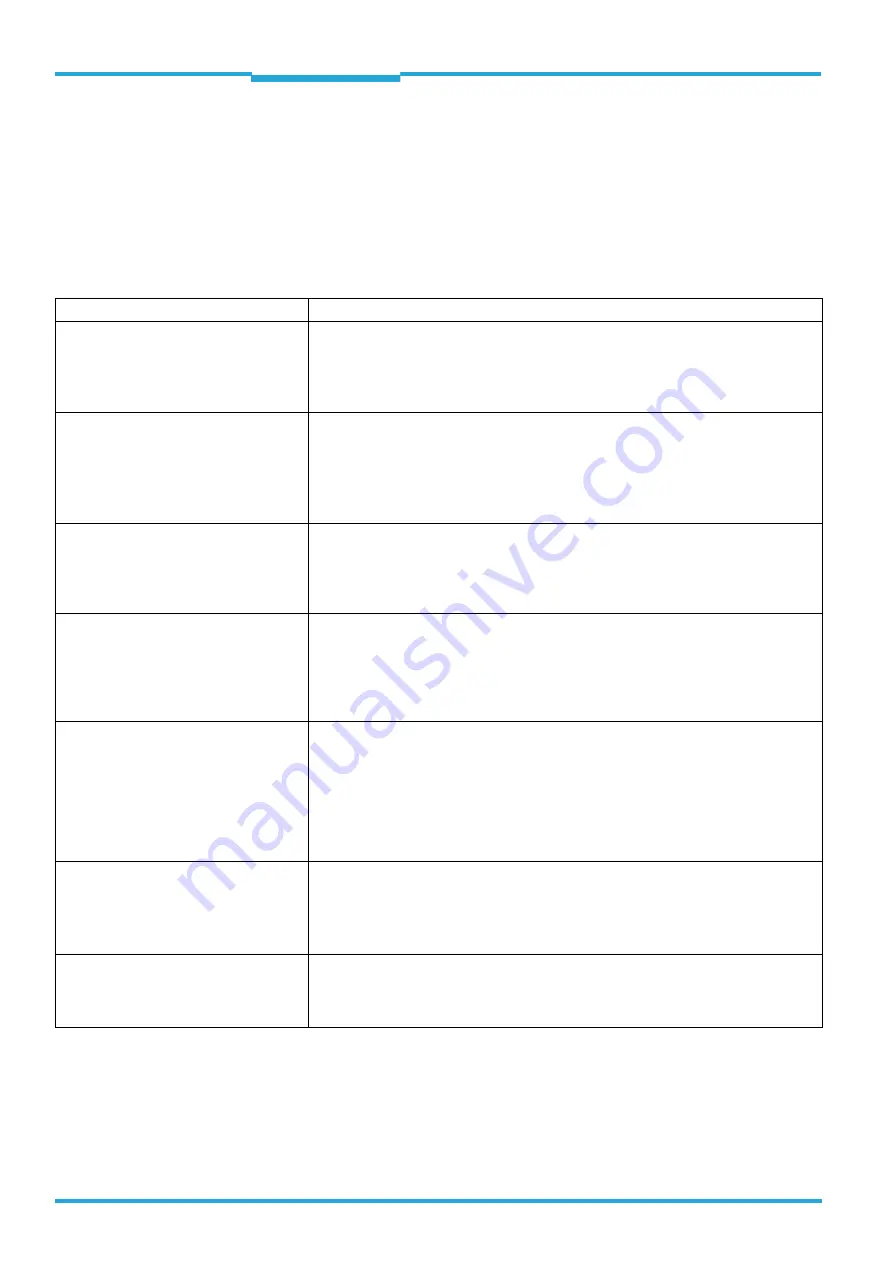
Chapter
3
Operating Instructions
Laser measurement sensor LD-MRS
20
©
SICK AG · Germany · All rights reserved · Subject to change without notice
8012948/ZMQ0/2017-06-09
Product description
3.3
System requirements
For general system requirements refer to the data sheet for the LD-MRS (see
Technical specifications, Page 94
The requirements for
,
are summarized in the respective chapters.
3.3.1
Product features and functions (overview)
Performance feature
Characteristic
General advantages
• reliable detection of objects in the field of view of the LD-MRS
• high scanning range and compact housing
• simultaneous measurement on 8 planes
• LD-MRS HD: expanded penetration through dust by special receiver unit and extended
dust filter software
Safety and comfort for the user
• Rugged, compact aluminum housing also available as lightweight housing
• laser class 1, laser switches off in case of faults
• enclosure rating IP 69K in mounted condition
• upgradable by firmware update via data interface Ethernet
• low power consumption
• wide range of supply voltage
Simple operation / parametrization
• Configuration of measuring mode using the SICK LaserView Customer Edition visual-
ization tool with Windows and Linux
• And configuration of field monitoring using the SOPAS-ET the configuration software
with Windows
• alternatively using commands in messages
Operating states
• wait mode: Configuration of the LD-MRS
• Operating mode measurement: Scanning the field of view
• Operating mode "Object tracking". Scanning the field of view and tracking of up to 64
objects in field of view.
• Field monitoring mode: scanning the field of view and monitoring specific fields for
changes (field intrusion)
Output of results
• Measurements: via the Ethernet data interface
• Object tracking: pre-processed object data allows for object tracking of up to 64 ob-
jects simultaneously, as well as the output of their dynamic properties (e.g.. speed, di-
rection, size, etc.)
• Field violations: via a maximum of 10 externals switch outputs with the help of two op-
tional CAN modules (accessory) with eight configurable I/O ports each, optional arm-
ing of specific, freely-definable evaluation instances through 2 external switching
inputs
Electric interfaces
• power supply (9 to 27 V DC)
• Ethernet data interface
• Data interface CAN
• synchronization interface
• auxiliary data interface: RS-232
Connection technology (type)
• connection "Ethernet": 4-pin socket (round plug-in connection)
• connection "Data interfaces/synchronization": 12-pin socket (round plug-in connec-
tion)
• connection "Power": 4-pin plug (round plug-in connection)
Tab. 3-4: Product features and functions (overview)