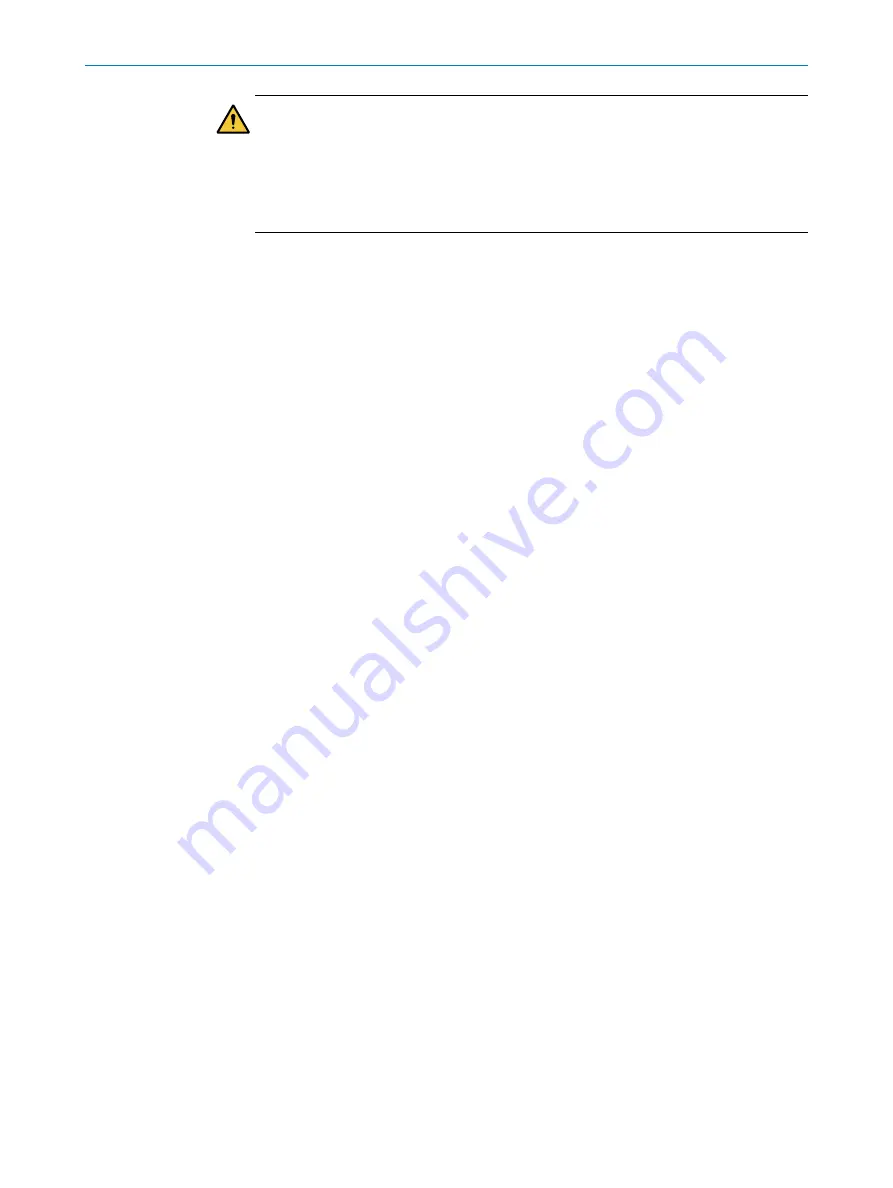
DANGER
Hazard due to lack of effectiveness of the protective device
In the case of non-compliance, it is possible that the dangerous state of the machine
may not be stopped or not stopped in a timely manner.
b
Make sure that the following control and electrical requirements are met so the
safety laser scanner can fulfill its protective function.
•
It must be possible to electrically influence the control of the machine.
•
Use the same earthing method for all devices that are electrically connected to the
safety laser scanner.
•
All earthing points must be connected with the same ground potential.
•
Voltage must be supplied in accordance with SELV/PELV (IEC 60204-1) for all
devices that are electrically connected to the safety laser scanner.
•
All devices connected to a local input or output of the safety laser scanner must
be in the same SELV/PELV circuit as the safety laser scanner.
•
The control that is connected and all devices responsible for safety must com‐
ply with the required performance level and the required category (for example
according to ISO 13849-1).
•
When using a safety controller, different signal levels of both OSSDs in an OSSD
pair must be detected depending on applicable national regulations or required
reliability of the safety function. The maximum discrepancy time tolerated by the
control must be selected according to the application.
•
In order to reach higher electromagnetic compatibility under rough electromag‐
netic ambient conditions, we recommend setting the input filter time of the con‐
nected control (on-off filter) to a value ≥ 5 ms. Please note that this increases the
response time of the total system by at least this set filter time.
•
A restart interlock must be implemented depending on applicable national regula‐
tions or required reliability of the safety function. If a restart interlock is required, it
must be implemented in the external controller.
The safety laser scanner complies with the regulations for electromagnetic compatibility
(EMC) for the industrial sector (Radio Safety Class A).
4.4.1
Electromagnetic compatibility
Overview
Safety components switch all safety outputs to the OFF state in the event of errors in
order to rule out potentially dangerous situations. For example, faulty data transmission
must lead to a shutdown for safety-related devices, even if it can be tolerated for
non-safety-related devices.
To avoid electromagnetic interference as much as possible, a uniform grounding con‐
cept is required for the entire system. In particular, the functional earth must be
connected using suitable conductors.
Electromagnetic interference depends on the environment in which the product is used.
The product is tested and certified according to common standards. It is therefore
reliable when used in industrial environments.
Shielded cables
When using shielded cables, the shielding should be applied on both sides. Deviations
are only permitted in exceptional and justified cases. Especially when using motors or
other inductive consumers, one-sided support of the shielding is not sufficient because
it does not act against inductive interferers.
PROJECT PLANNING
4
8017784/1ELL/2022-01-21 | SICK
O P E R A T I N G I N S T R U C T I O N S | microScan3 Core I/O AIDA
47
Subject to change without notice