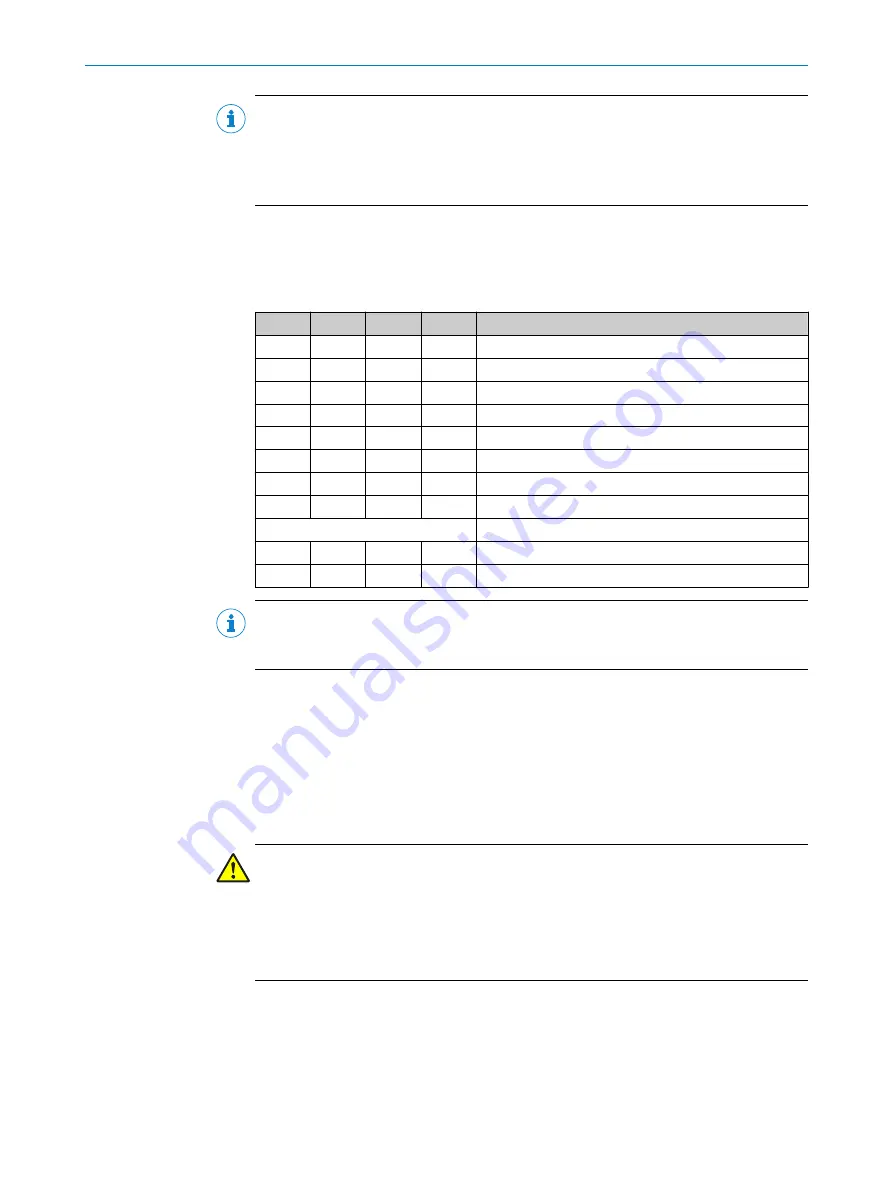
NOTE
The control for the monitoring case switching must meet the required safety level.
The circuit for the control inputs must be suitable for the ambient conditions to be
expected so that systematic and design-related effects and resulting errors on the
switching of the monitoring cases can be excluded.
Static complementary sampling
Using external inputs (e.g., those of a PROFIsafe safety controller), 2
4
= 16 monitoring
cases can be switched via a maximum of four control input pairs.
Table 15: Truth table for complementary sampling
A
B
C
D
E.g. case
0
0
0
0
1
1
0
0
0
2
0
1
0
0
3
1
1
0
0
4
0
0
1
0
5
1
0
1
0
6
0
1
1
0
7
1
1
1
0
8
…
…
0
1
1
1
15
1
1
1
1
16
NOTE
An undefined input information will result in the device switching the safety outputs to
the OFF state or signaling
Protective field interrupted
.
7.11.2
Multiple sampling
If multiple sampling is set, an object must be scanned several times before the S3000
transmits a protective field interruption. In this way you can reduce the probability that
insects, welding sparks or other particles result in the shutdown of the system.
If a multiple sampling of 3 is configured, for example, an object must be detected in the
protective field three times in succession before the S3000 signals
Protective field inter‐
rupted
.
DANGER
In the case of non-compliance, it is possible that the dangerous state of the machine
may not be stopped or not stopped in a timely manner.
The total response time is increased by the multiple sampling.
b
With a multiple sampling greater than 2, note that a supplement must be added to
the basic response time.
A multiple sampling of 2 is the minimum setting. The multiple sampling can be set to a
value up to 16 using the CDS. The supplement to the basic response time resulting
from this setting is displayed in the CDS.
CONFIGURATION
7
8013291/ZA19/2019-11-14 | SICK
O P E R A T I N G I N S T R U C T I O N S | S3000 PROFINET IO, S3000 PROFINET IO-OF
85
Subject to change without notice