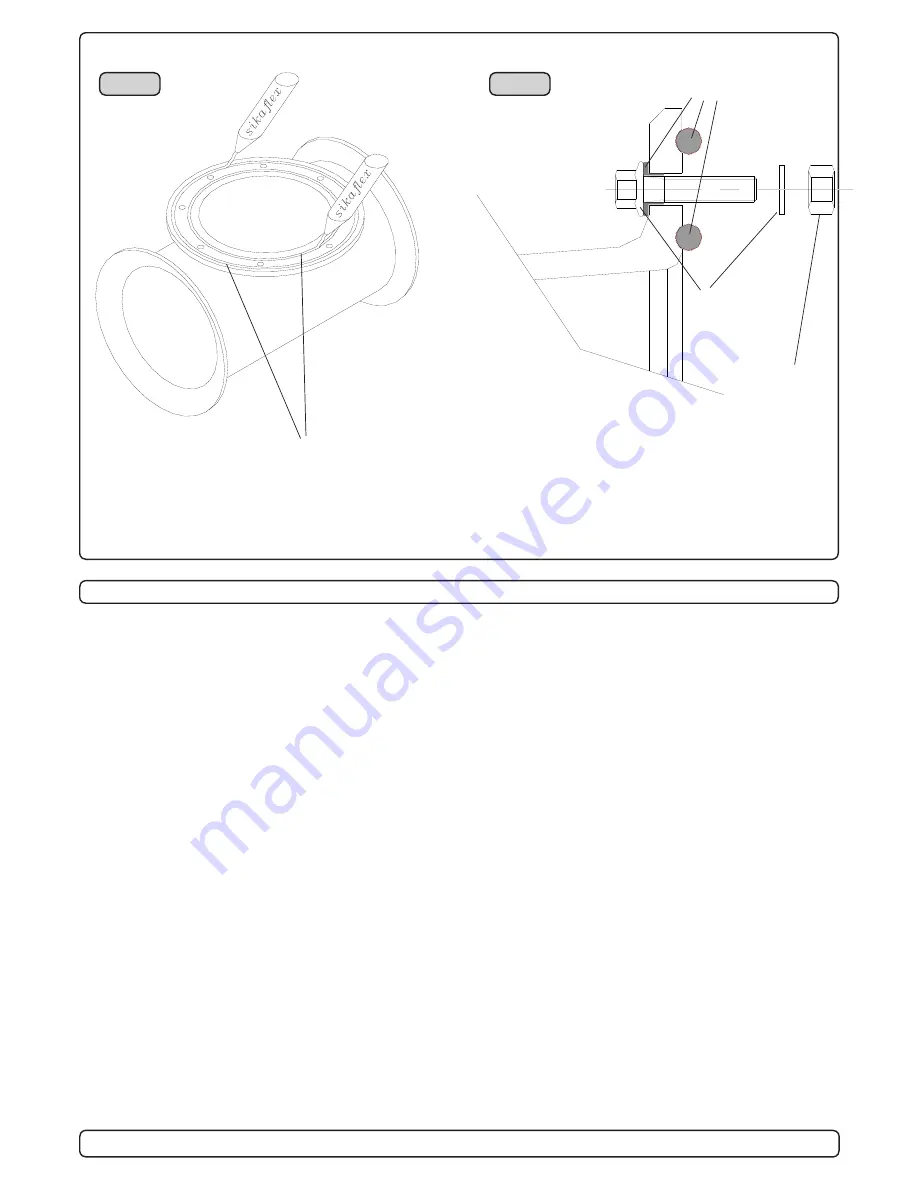
4
SE80/185T & SE100/185T Ignition Protected thruster assembly
1.0 - 2007
Fig. 1
Bolt on installation of the stern tunnel
1. Make sure that there are enough space both inside and out-
side the transom of the boat.
2. Once the place for the installation has been decided, hold the
tunnel in place in the horizontal position and mark the bolt
holes. Remove the tunnel and it is then possible to calculate
and mark the centre.
3. It is important that the tunnel flange sits flush on the transom.
If this is not so, then the area on the transom will have to be
flattened to ensure a snug fit.
PS ! Take care with grinders as it is very easy to remove to
much in fibreglass
At this time, cut out the centre hole and the transom to the
same internal diameter as the tunnel flange and drill the bolt
holes. Before bolting on the stern tunnel, the prepared area
must be sealed with a gelcoat or similar to ensure there is no
water ingress into the hull.
4. Before fitting the tunnel to the transom, fit the lower gear leg
to the tunnel as described on page 6. We recommend that
you fit the oil feed pipe also before the tunnel is bolted to the
transom.
5. When fitting the tunnel, ensure that there is ample sealant
(Sikaflex or similar) in the sealing tracks of the tunnel flange
and around the bolts to make a water tight fitting (Fig. 1/2).
Bolts, washers and nuts are not included as they will wary de-
pending on the transom thickness We recommend A4 stain-
less with A4 lock nuts and A4 washers of a large diameter on
both outside and inside.
Bolts diameter: ø 10mm or 3/8” stainless steel
6. Refer to the installation manual for the recommended thruster
fitting.
If a bow thruster is also installed, we strongly advice to
use separate battery banks for the two thrusters to avoid
extreme voltage drop if both thrusters are to be used at the
same time. Refer to the thruster manuals for adviced battery
capacity and cable sizes for each thruster.
Also ensure that you do not have direct connections of both +
and - if you have built together controls for both thrusters to
avoid current leakage between separate battery banks.
If you are installing the standard Sidepower dual joystick
panel this is already secured.
Fig. 2
SEALANT
WASHERS
LOCKNUT OR
DOUBLE NUTS
SEALANT