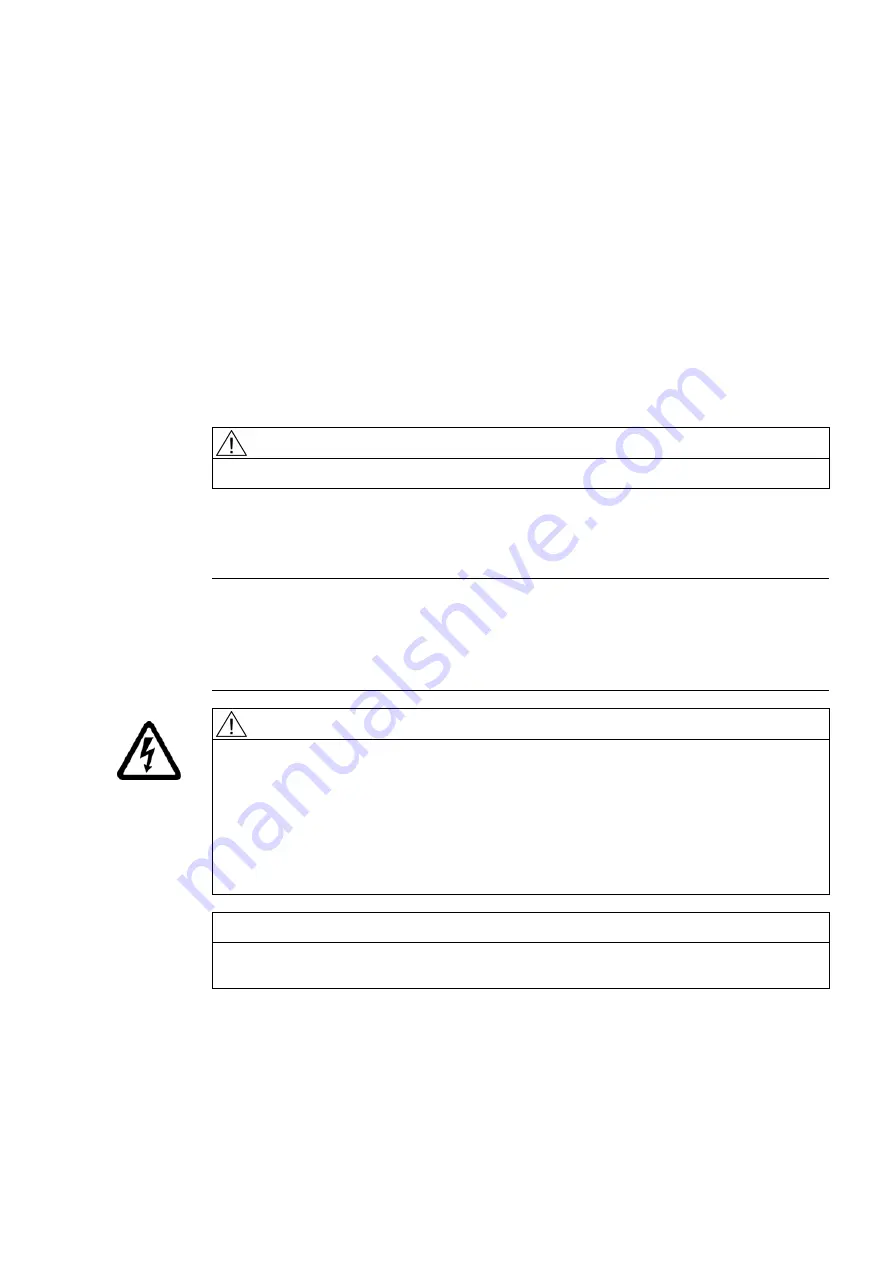
A5E00264365A
Siemens AG Operating Instructions 2.02 1PL622
43
Start-up
4
4.1
Preparations
Safety note
WARNING
Only expert personnel should be entrusted with work on power installations.
Checking the insulation resistance
Note
There is no need to check the insulation resistance when commissioning. We only
recommend doing so after long storage or shutdown periods.
After long storage or shutdown periods, the insulation resistance of the windings must be
measured to ground with direct voltage.
WARNING
Hazardous voltage
During the measurement, and immediately afterwards, hazardous voltage levels are
applied on some of the terminals and they should not be touched. Touching live
components can be result in death or serious injury.
Never touch the terminals when measuring or immediately after the measurement.
Check the supply feeder cables connected in order to ensure that the line supply voltage
cannot be connected.
CAUTION
Before you begin measuring the insulation resistance, please read the manual for the
insulation resistance meter you are going to use.
●
Always measure the insulation resistance of the winding to the motor enclosure when the
winding temperature is between 20 and 30°C.