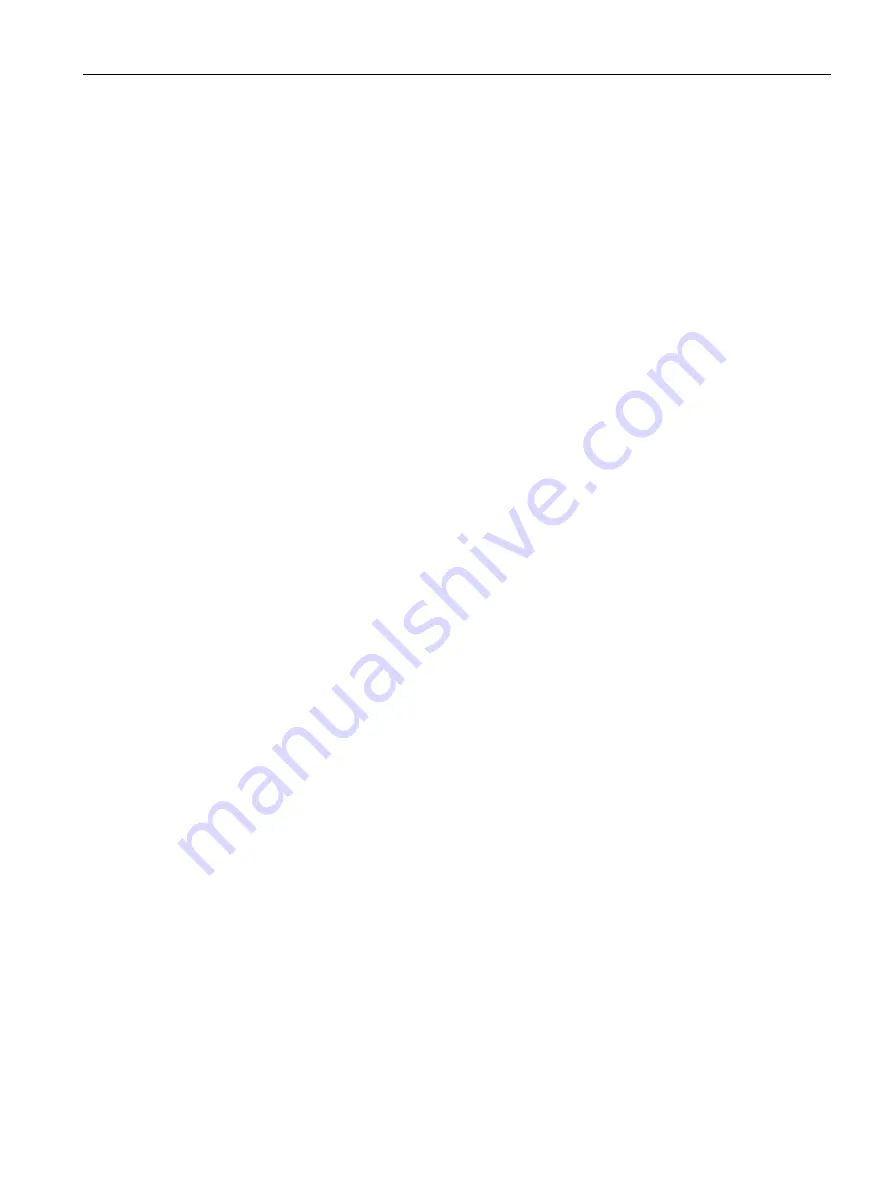
Functions
6.19 Motor CW
Motor
starter (3RK1308‑0**00‑0CP0)
Equipment Manual, 11/2019, A5E34821005002A/RS-AC/003
119
6.19
Motor CW
In automatic mode, the motor is activated or deactivated in the CW direction with the aid of
the process image of the outputs. If you would like to control the motor via the 3DI/LC
module, activate the LC input on the 3DI/LC module (manual local mode). Bit 0.0
"Motor CW" in the process image of the outputs is ignored in manual local mode.
The parameter can only be implemented as an "NO contact".
If "Input n-signal" = retentive, and "Input n-action" = Motor-CW/CCW, at least one input must
always be parameterized with the "Tripping ... " or "Quick Stop" input action.
If this rule is violated, the motor starter will reject the parameters with the relevant diagnostic
message.