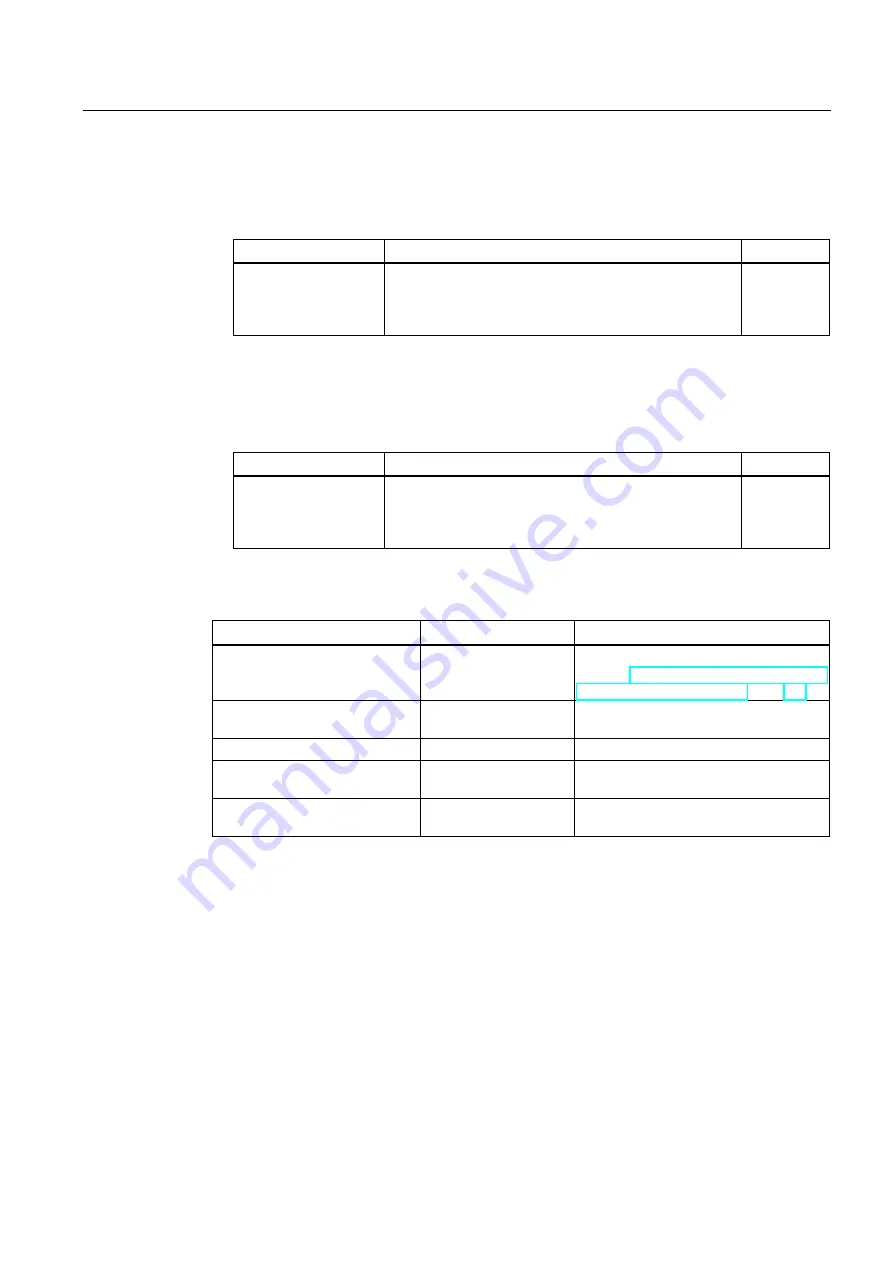
Technical specifications
7.8 Environmental conditions
Carrier controller
Operating Instructions, 09/2013, A5E03474162-02
53
The following table shows the valid environmental conditions for the device.
●
Mechanical environmental conditions
Standard
Title
Release
IEC 60721-3-3:1994
Classification of environmental conditions – part 3:
Classes of environmental disturbances and their limits,
section 3: Stationary operation
1
, weatherproof
Class 3M3 applies.
01.12.1994
1
Stationary operation refers to operation in combination with the rail system. The rail system
must be designed to prevent the transmission of any impermissible impact to the carrier
controller.
●
Climatic environmental conditions
Standard
Title
Release
IEC 60721-3-3:1994
Classification of environmental conditions – part 3:
Classes of environmental disturbances and their limits,
section 3: Stationary operation, weatherproof
Class 3K3 applies.
01.12.1994
The following values are derived for the significant environmental conditions from the
standards stated.
Environmental condition
Value
Comment
Temperature
0 to 45 °C
Applies to installation according to
chapter "Mounting location and free
space for the carrier control (Page 17)"
Atmospheric pressure
1140 to 795 hPa
Corresponds to an altitude of –1000 to
2000 m
Humidity, relative
10 … 90 %
No condensation
Vibration
IEC 60068-2-6
5 to 9 Hz: 3.5 mm
9 to 500 Hz: 9.8 m/s
2
Sinusoidal
Clock frequency of the
frequency inverter
≤
12 kHz
–
Operation with additional protective measures
You must take additional measures to operate the HMI device at the following locations:
●
At locations with a high degree of ionizing radiation
●
At locations with harsher operating conditions, for example due to:
–
Corrosive vapors, gases, oils or chemicals
–
Electrical or magnetic fields of high intensity
●
In systems that require special monitoring, for example:
–
Elevators
–
Systems in especially hazardous rooms