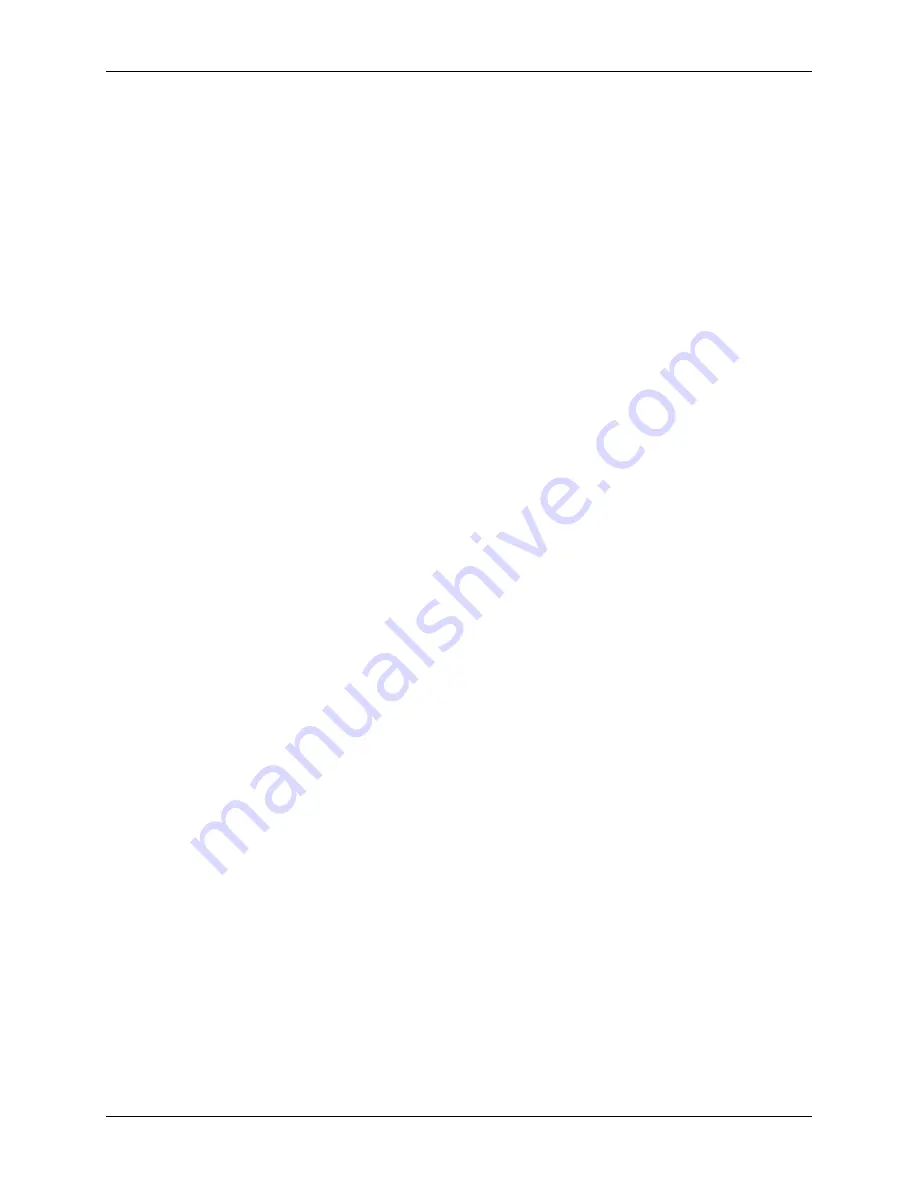
Installation
UMSITRPDS3-1
November
2010
4-4
4.3.3 Impulse Piping for Absolute and Differential Models
Impulse piping is the piping to be connected to the transmitter’s process connection(s). For suggested
flow and level measurement piping arrangements, refer to:
•
Differential Model - Figures 4-1 and 4-2
•
Absolute Model - Figures 4-3 and 4-4
•
Flange Model - Figure 4-5
Note the following when planning and installing piping.
•
Install impulse piping in accordance with ANSI Code B31.1.0.
•
Make impulse piping length as short as possible to reduce frictional loss and temperature-induced
pressure variations.
IMPORTANT
When using impulse lines on a high temperature process, locate the transmitter far
enough away from the heat source to keep it within temperature specifications [28°C
(50ºF) per foot cooling to a normal ambient is assumed for non-insulated impulse lines].
•
For lines between the process and transmitter, use impulse piping of 3/8" OD or larger to avoid
friction effects (causes lagging) and blockage.
•
Use the least number of fittings and valves possible to minimize leakage problems. Teflon
®
tape is the
recommended thread sealant for process connections at the transmitter.
•
Valves used in pressure service should be either globe or gate type. Valves used in gas service should
be of a type that does not permit condensate to build up behind the valve.
•
Install sediment chambers with drain valves to collect solids suspended in process liquids or moisture
carried with non-condensing gases.
•
Install air chambers with vent valves at high point in piping to vent gas entrained in process liquid.
•
Remote diaphragm seals can be used to keep corrosive liquid or gas from the transmitter pressure
inlets and isolation diaphragm.
•
Alternatively, use sealing fluid to isolate the process from the transmitter. Sealing fluid must be of
greater density than process fluid and non-miscible.
•
For transmitters located above the process, slope piping from the transmitter at least 1 inch/foot (83
mm/M) down toward process. For transmitters below the process, slope piping at least 1 inch/foot (83
mm/M) up to process.
•
Protect pressure lines (by shielding if necessary) from objects or equipment that may bend or kink the
line causing fluid flow restriction.
•
Protect the pressure lines from extreme temperature ranges. Lines should be protected from freezing
by installing a heat trace.
•
A three-valve manifold should be used with a differential transmitter model. A two-valve manifold
can be used with an absolute model to permit servicing and zero checks.
Summary of Contents for 7MF4033 series
Page 48: ...Model 275 Universal Hart Communicator UMSITRPDS3 1 November 2010 2 26 ...
Page 86: ...Installation UMSITRPDS3 1 November 2010 4 34 ...
Page 152: ...Calibration and Maintenance UMSITRPSD3 1 November 2010 7 20 ...
Page 158: ...Circuit Description UMSITRPDS3 1 November 2010 8 6 ...
Page 197: ......
Page 198: ......
Page 200: ...Model Designations and Specifications UMSITRPDS3 1 November 2010 9 42 ...
Page 204: ...Glossary UMSITRPDS3 1 November 2010 10 4 ...
Page 208: ...Appendix A Online Configuration Map UMSITRPDS3 1 11 4 November 2010 ...
Page 216: ...Appendix C Elevation and Suppression Correction UMSITRPDS3 1 13 4 November 2010 ...