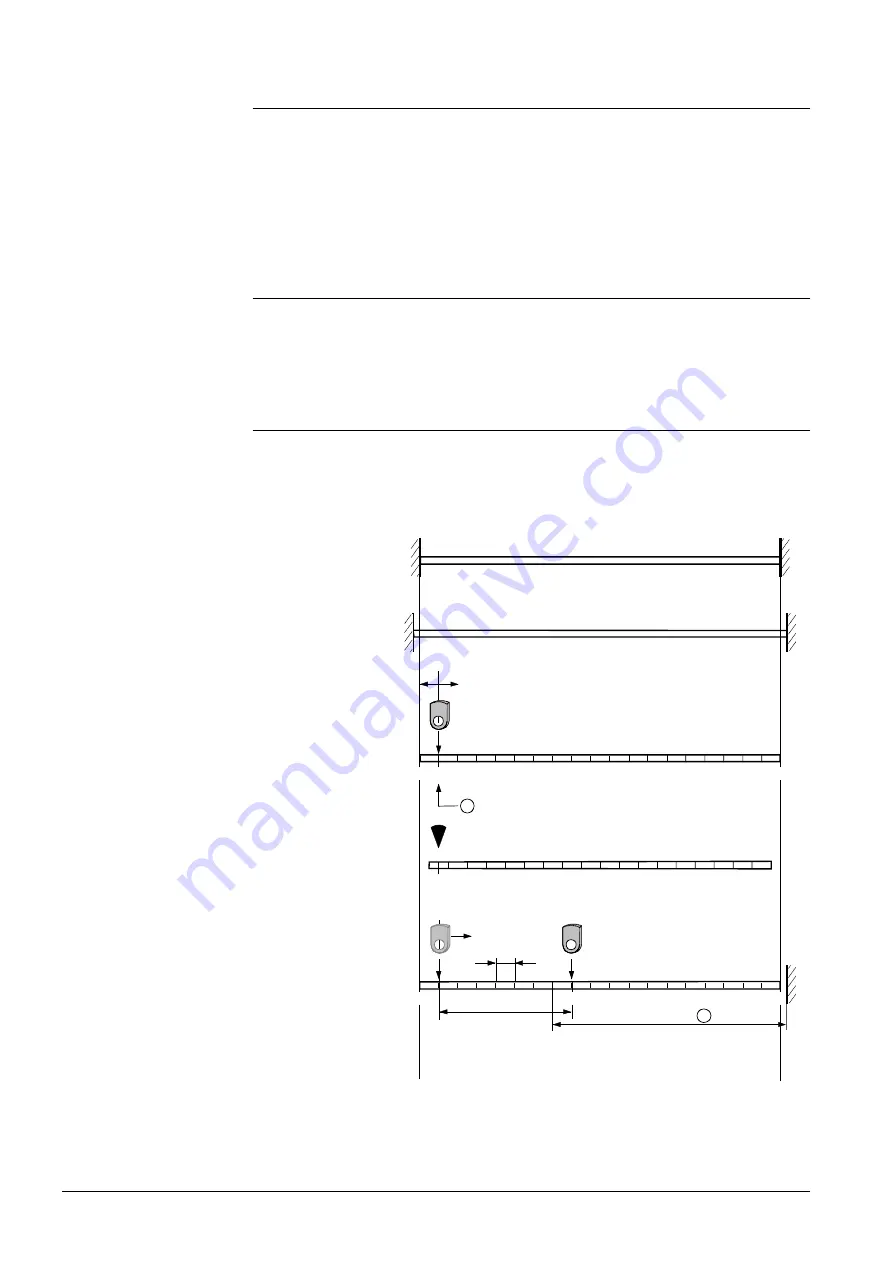
12/44
Siemens
Actuators without spring return GEB…1
CM2Z4621en
Building Technologies
2017-05-26
3 Technical
design
This chapter discusses the following topics:
∂
Motor
technology.
∂
Adjustable auxiliary switches.
∂
Adjustable characteristic function (positioning signal, DC 0...35 V).
∂
Control characteristics by including the neutral zone
3.1 Motor
technology
A synchronous motor enables accurate speed control. The magnetic coupling serves
as a torque supervision to protect both actuator and dampers.
3.2 Rotary range and mechanical limitation
The illustration below shows the relationship between the inner and outer mechanical
limitation of the rotary range.
Gear train rotary range
Inner mechanical limits
5°
0°
20°
40°
60°
80°
5°
95°
90°
2,5°
0°
0°
95°
97.5°
-2,5°
40°
95°
Χ
=
62.5°
x 5°= 7 5°
·
·
x >1
x = 0
Χ
= 95°-x 5° +2.5°
Χ
= 95°
·
0°
46
21
D
03
1
2
Outer mechanical limits
Adapter setting range
Actuator rotary range
(without rotary angle limitation)
•
Gear train presetting
(factory setting)
Pointer
Rotary angle scale
Rotary angle limitation
Adapter setting
Example: x = 7
x = number of steps (5°)
‚
incl. gear train presetting
Introduction
Motor technology
Mechanical functions