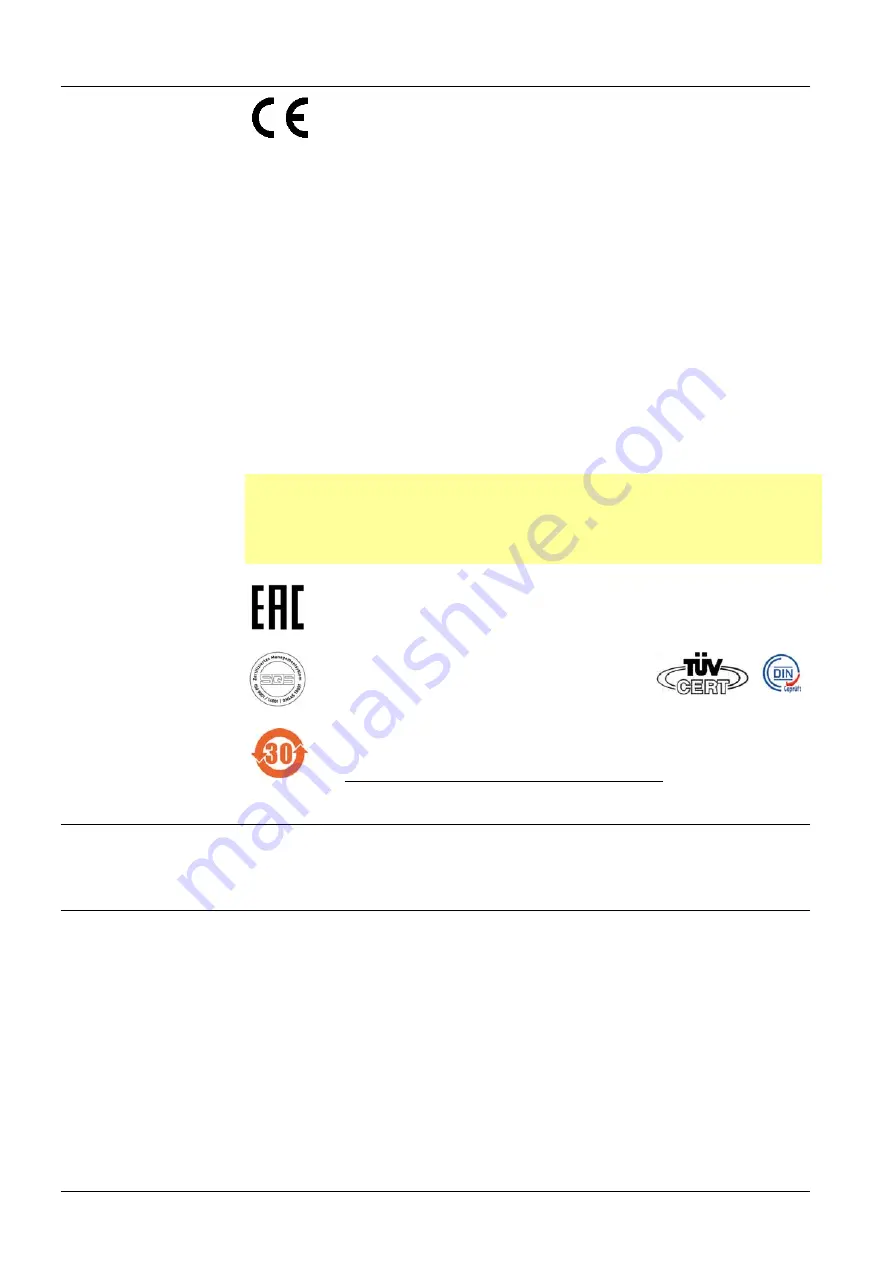
4/16
Building Technologies Division
CC1N7138de
18.05.2016
Standards and certificates
Applied directives:
Low-voltage
directive
2014/35/EC
Directive for pressure devices
97/23/EC and
2014/68/EC (2016-07-16)
Electromagnetic
compatibility
EMC
(immunity) *)
2014/30/EC
*) The compliance with EMC emission requirements must be checked after the burner control is
installed in equipment
Compliance with the regulations of the applied directives is verified by the adherence to
the following standards / regulations:
Automatic burner control systems for burners and appliances
burning gaseous or liquid fuels
DIN EN 298
Automatic electrical controls for household and similar use
Part 2-5:
Particular requirements for automatic electrical burner control
systems
DIN EN 60730-2-5
The relevant valid edition of the standards can be found in the declaration of
conformity!
Note on
DIN EN 60335-2-102
Household and similar electrical appliances - Safety - Part 2-102:
Particular requirements for gas, oil and solid-fuel burning appliances having electrical
connections. The electrical connections of the LMO and the AGK11 comply with the
requirements of EN 60335-2-102.
EAC Conformity mark (Eurasian Conformity mark)
ISO 9001:2008
ISO 14001:2004
OHSAS 18001:2007
China RoHS
Hazardous substances table:
http://www.siemens.com/download?A6V10883536
Service notes
The service adapters can only be used for a short time. They may only be used in
supervised operation by qualified staff.
Life cycle
Burner controls has a designed lifetime* of 250,000 burner startup cycles which, under
normal operating conditions in heating mode, correspond to approx. 10 years of usage
(starting from the production date given on the type field).
This lifetime is based on the endurance tests specified in standard EN 298.
A summary of the conditions has been published by the European
Control
Manufacturers Association
(Afecor) (www.afecor.org).
The designed lifetime is based on use of the burner controls according to the
manufacturer’s Data Sheet. After reaching the designed lifetime in terms of the number
of burner startup cycles, or the respective time of usage, the burner control is to be
replaced by authorized personnel.
* The designed lifetime is not the warranty time specified in the Terms of Delivery