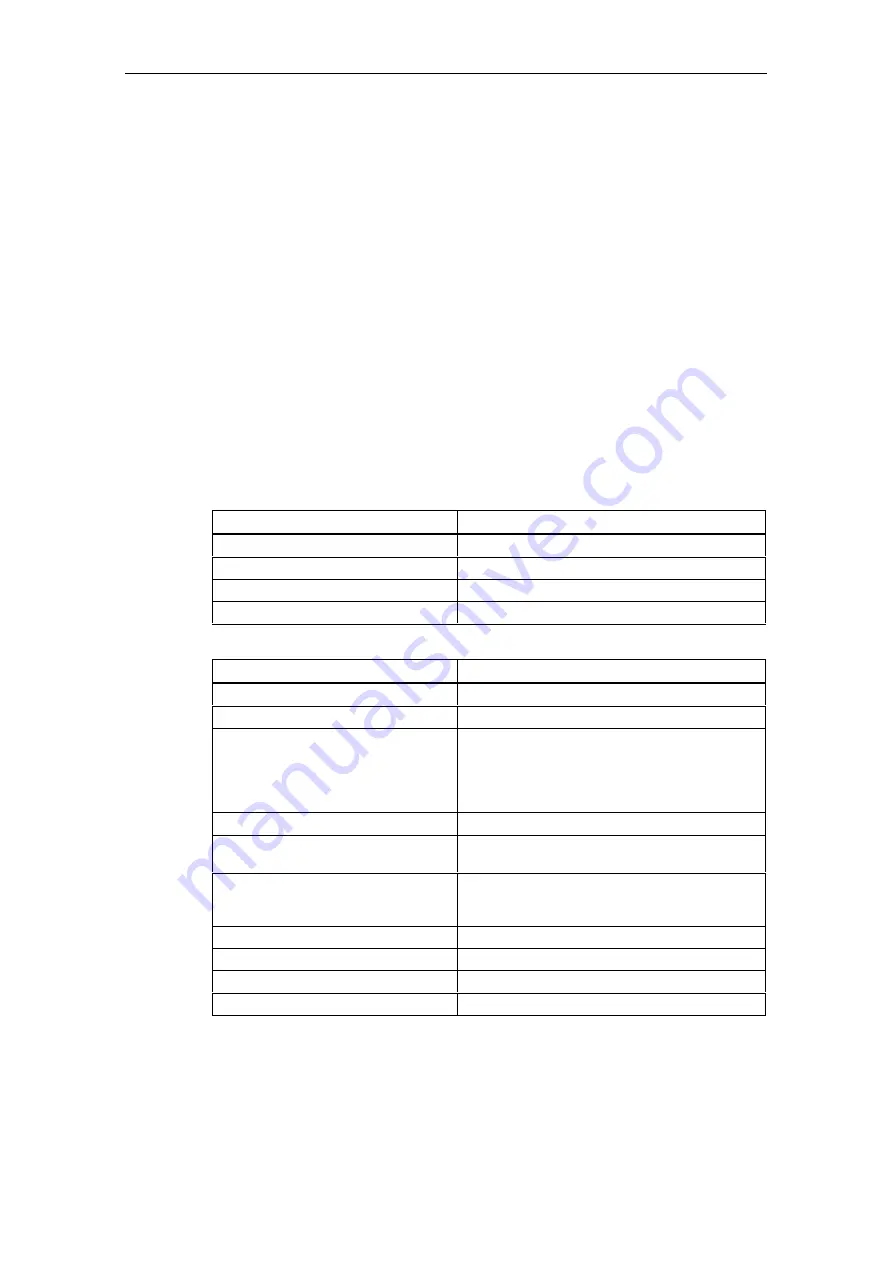
(GLWLRQ$
/LQNVWR352),%86'30DVWHU6\VWHPV
PROFIBUS Optional Board Operating instructions
6SE6400-5AK00-0BP0
49
6,0$7,&+0,+XPDQ0DFKLQH,QWHUIDFH
You can access a MICROMASTER4 directly using a SIMATIC HMI as the
PROFIBUS master.
A MICROMASTER4 reacts to a SIMATIC HMI in the same way as it does to a
SIMATIC S7. As regards access operations to drive parameters, the following
simple formula applies:
½
Parameter number = data block number
½
Parameter subindex = data block offset
All SIMATIC OPs and TDs with final digit 7 are suitable.
3UR7RRO
The SIMATIC HMI is configured with "ProTool".
The following specific settings for drives must be noted when ProTool is used as
the configuring tool:
Controls: Protocol always "
6,0$7,&6
"
2WKHUSDUDPHWHUV
)LHOG
9DOXH
Network parameter - profile
DP
Network parameter - baud rate
(optional)
Communication partner - address
(PROFIBUS address of the drive)
Communication partner - slot/subrack
don’t care, 0
9DULDEOHV*HQHUDOLQGH[FDUG
)LHOG
9DOXH
Name
(optional)
Control
(optional)
Type
Depending on addressed parameter value, e.g.:
INT:
for I2, O2
DINT:
for I4, O4
WORD: for V2, L2
REAL: for NF
Area
DB
DB
(data block number)
Parameter number
1 ... 3999
DBB, DBW, DBD
(data block offset)
Subindex
0:
for nonindexed parameters
0 ... 120: for indexed parameters
Length
(not activated)
Acquisition cycle
(optional)
No. of elements
1
Decimal places
(optional)
Summary of Contents for Micromaster Profibus
Page 1: ...0 520 67 5 352 86 2SWLRQDO RDUG 2SHUDWLQJ LQVWUXFWLRQV GLWLRQ 8VHU RFXPHQWDWLRQ ...
Page 2: ......
Page 8: ... GLWLRQ PROFIBUS Optional Board Operating instructions 8 6SE6400 5AK00 0BP0 ...
Page 10: ... GLWLRQ PROFIBUS Optional Board Operating instructions 10 6SE6400 5AK00 0BP0 ...
Page 60: ... SSHQGL GLWLRQ PROFIBUS Optional Board Operating instructions 60 6SE6400 5AK00 0BP0 ...
Page 62: ... ORVVDU GLWLRQ PROFIBUS Optional Board Operating instructions 62 6SE6400 5AK00 0BP0 ...
Page 64: ......
Page 65: ......