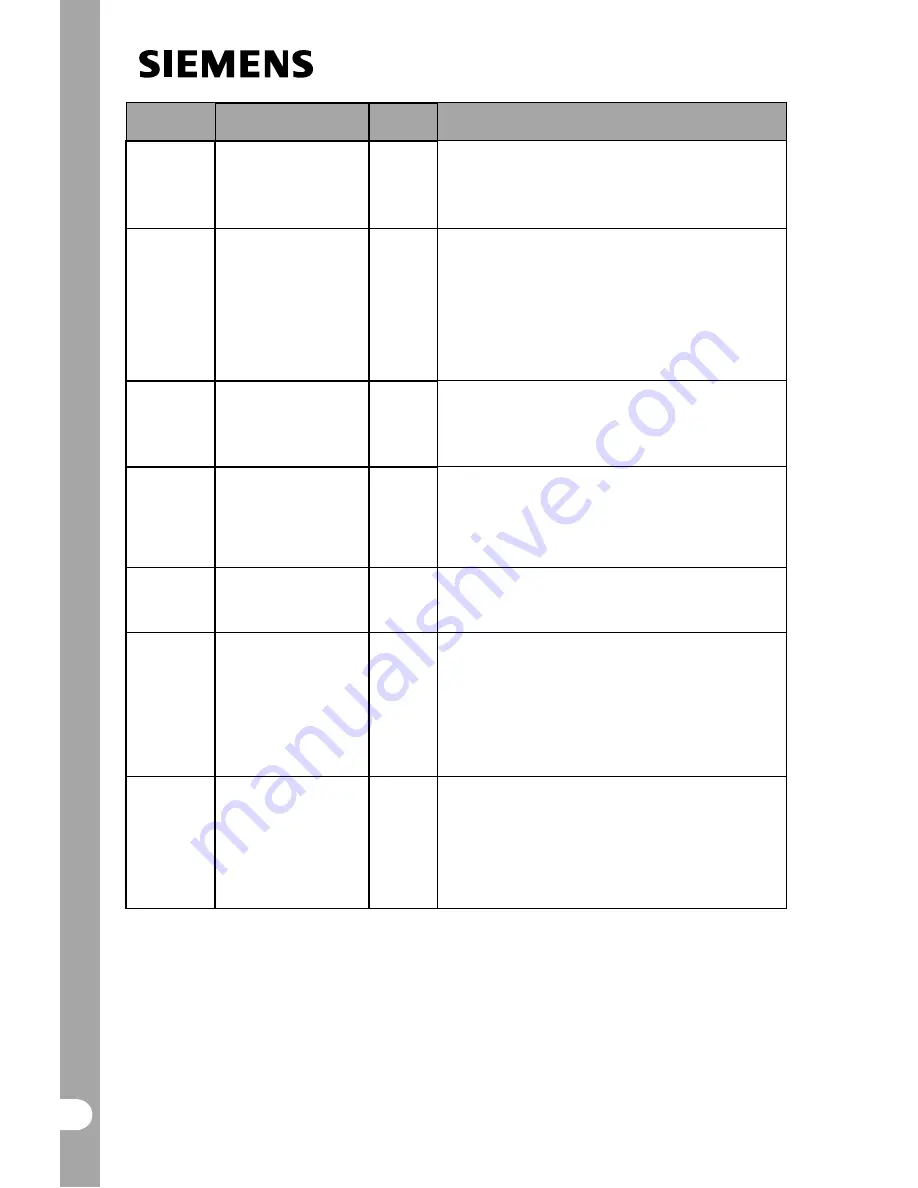
COMBIMASTER & MICROMASTER Integrated
REFERENCE MANUAL
©
Siemens plc. 1999
| G85139-H1731-U300-D2
38
Parameter
Function
Range
[Default]
Description / Notes
P965
Special Baud Rate 2
0 – 255
(SW
Version :
3.00
onwards)
Specific to CAN (Access only possible with P099 = 2).
P966
PZD Send Interval
Time
0 –
65535
[0]
(SW
Version :
3.00
onwards)
Specific to CAN (Access only possible with P099 = 2).
The rate in ms at which PZD is sent is set.
0
= Values sent only after a remote request
1…65534 =
Values sent after a preset time (in ms)
or after a remote request
.
65535
= Values sent whenever the PZD changes
or after a remote request.
P967
Last Received Control
Word
0 – FFFF
Hex
Specific to PROFIBUS-DP/CAN. See PROFIBUS / CAN
Handbooks for further details. (Access only possible
with P099 = 1 or 2).
This is the control word which was most recently received
and is currently active within the drive.
P968
Last Sent Status Word
0 – FFFF
Hex
Specific to PROFIBUS-DP/CAN. See PROFIBUS / CAN
Handbooks for further details. (Access only possible
with P099 = 1 or 2).
This is the status word which currently represents the
operating state of the drive and which is returned on
demand to the requestor.
P969
(SW
Version :
3.00
onwards)
Specific to CAN (Access only possible with P099 = 2).
P971
••••
EEPROM storage
control
0 – 1
[1]
0
= Changes to parameter settings (including
P971
are lost when power is removed.
1
= Changes to parameter settings are retained during
periods when power is removed.
IMPORTANT
Take care not to exceed the EEPROM write cycle limit of
50,000/parameter (approx.) when using the serial link to
update parameters, otherwise data loss or corruption may
occur. Read cycles are unlimited.
P986
Relay Output
0 – 3
[0]
(SW
Version :
3.00
onwards)
Relay 1 = Fault Relay (RL1)
Relay 2 = Brake Relay
0
= Relay 1 & 2 - open.
1
= Relay 1 – closed
2
= Relay 2 – closed
3
= Relay 1 & 2 - closed