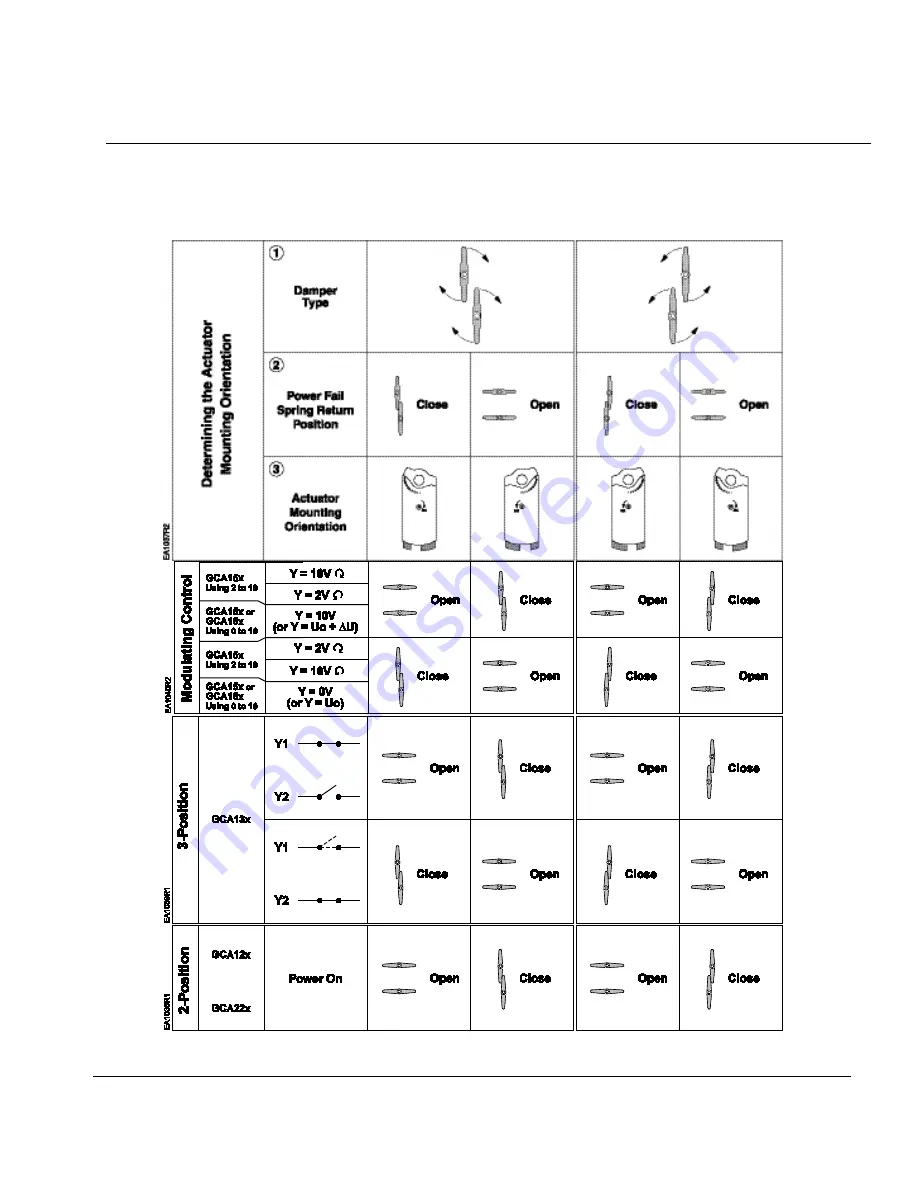
OpenAir™ GCA Series Spring Return 160 lb-in Electronic Damper Actuator
Technical Instructions
Document No. 155-173P25
May 19, 2014
Siemens Industry, Inc.
Page 13
Flip the actuator to select either clockwise or counterclockwise fail-safe rotation of the damper
shaft. Follow steps 1, 2, and 3 of Table 3 to determine the correct actuator mounting orientation.
Table 3. Actuator Mounting Orientation and Damper Control.