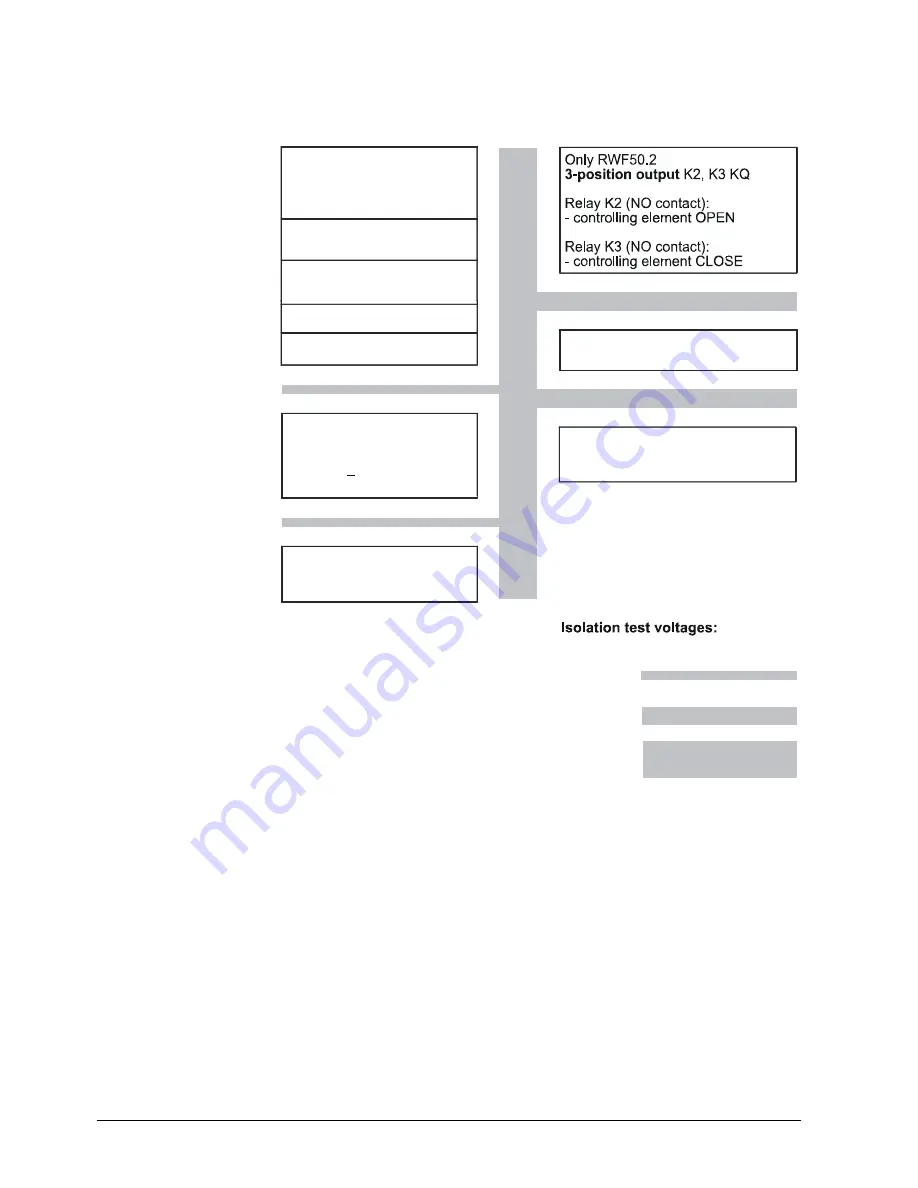
4.2 Galvanic
separation
The illustration shows the maximum test voltages between the electrical circuits.
DC 50 V
AC 1500 V
AC 3300 V
Analog input
Binary input
USB interface
LED
Buttons
For resistor thermometer
or
standard signals
D1
For potential-free contacts
Setup
For PC software ACS411
InP
Power supply measuring
transducer
G+, G-
DC 24 V 10%/max. 25 mA
(short-circuit-proof)
+
Only RWF50.3
Analog output
A+, A-
Burner release
1P, 1N
Relay (NO contact)
Power consumption
at AC 110...240 V,
+10%/-15%, 48...63 Hz
Max. 16 VA
7866d02e/1212
Figure 4: Test voltages
18/68
20089337
Summary of Contents for RWF 50.2
Page 2: ...20089337 Translation of the original instructions ...
Page 4: ...2 68 20089337 ...
Page 6: ...4 68 20089337 ...
Page 62: ...60 68 20089337 ...
Page 66: ...64 68 20089337 ...
Page 69: ......
Page 70: ......
Page 71: ......