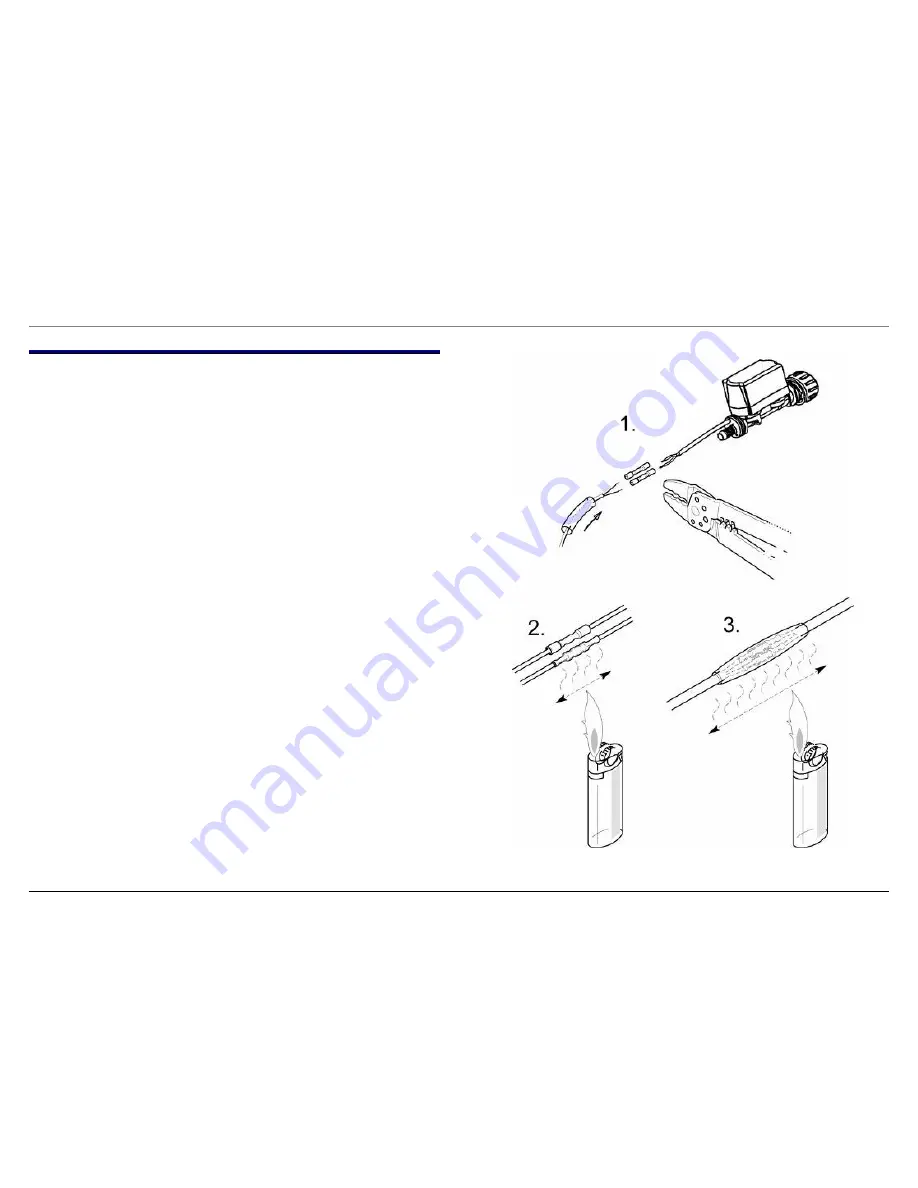
815_58300000003806_ara_en_e.doc – 30.01.12
Seite 38 von 67
6.3
Replacing the Aqua Stop valve
►
Open the housing
►
Disconnect the inlet hose
►
Cut through the electric connecting cables
►
Strip the insulation off the cable ends
►
Push the shrink-fit hose over the cable
►
Connect electric cables to the insulating sleeves (1.)
►
After fitting, warm the connectors until the shrinkage process occurs
and the hot-melt adhesive comes out of the ends of the connectors
(2).
►
Push the shrink-fit hose over the connectors and also warm until
the shrinkage process is complete (3)