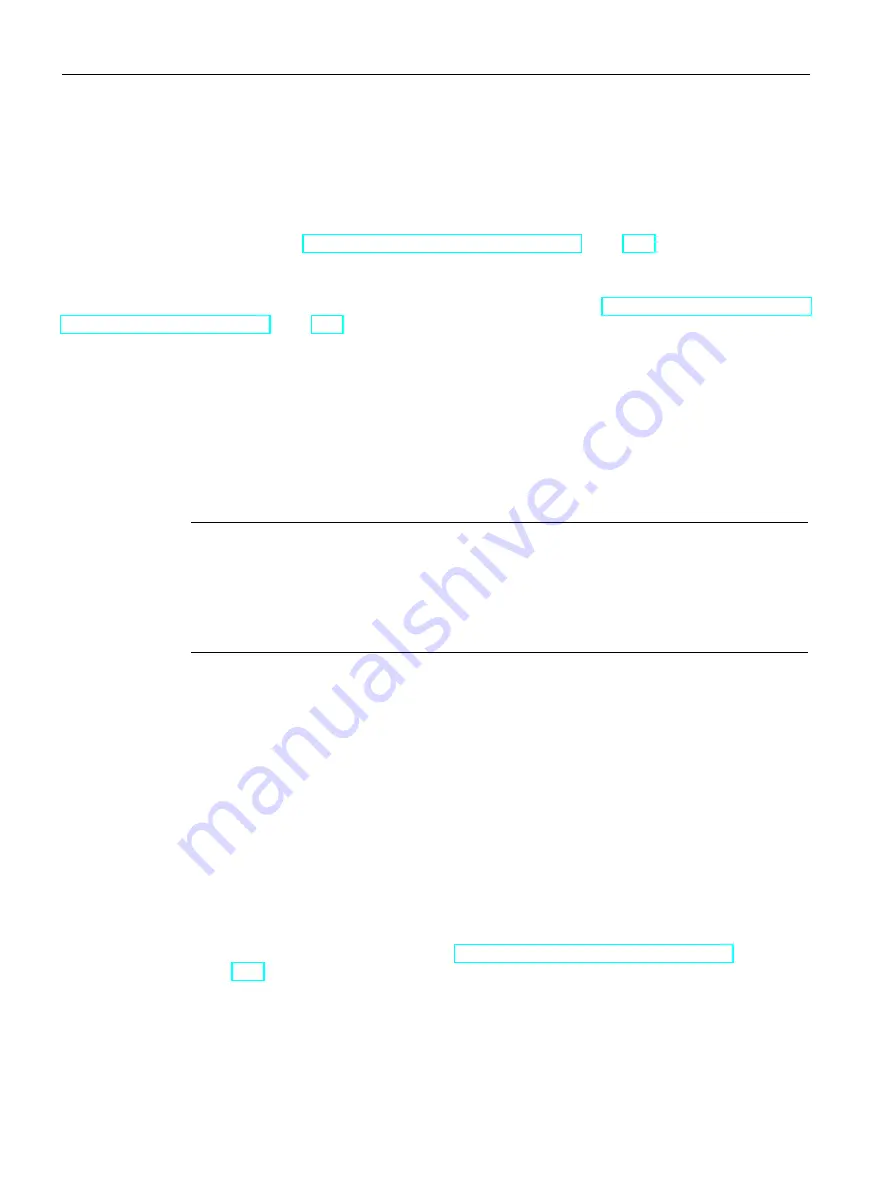
Controllers
4.5 Relay and fieldbus interfaces
ATD4xxW Door Controller for Industrial Applications
148
System Manual, 01/2017, A5E38080677-AB
4.5.5
Local/master operation
The slave (= SIDOOR control unit) generally signals via StatW1 (bit 9 = 1 "control
requested") that the master (= higher-level PLC on the fieldbus) should assume control. If
the PLC signals via STW1 (bit 10 = 1 "control by the programmable logic controller") that it is
taking over control, the process data is deemed to be valid and must be processed
accordingly. See Figure 4-4 Sequential control state graph (Page 149).
If the PLC does not assume control (bit 10 = 0 "no control") or if the slave does not request
control (ZSW1 bit 9 = 0 "local operation"), the process data is discarded and the sequential
control remains in the "S1:Z_switching on inhibited" state (see Figure 4-4 Sequential control
state graph (Page 149)).
For safety reasons, the controller automatically switches to local mode under the following
conditions:
●
Service button S402 (Open), S403 (Close) or S401 (Learn run) operated
●
An external drive order is pending via the service interface (X8, terminal for service tool
and USB adapter)
●
The local commissioning terminal module (H1, terminal module with S1 to S4, operator
control buttons for terminal module) is in a safety-related state through the use of the
operator control buttons
Note
Protected areas
Some areas of the navigation system are categorized as being safety-related. These include,
among others, all areas that affect the processing of the travel curve parameters. Local
operation mode ends and control is requested again by the PLC only upon leaving these
protected areas.
4.5.6
Master monitoring
Master monitoring monitors the internal communication channel to the higher-level PLC. This
ensures a defined response to the following situations:
●
Cable breakage (or bus interruption)
●
Hardware fault in the sending/receiving unit
●
Incorrect communication configuration (e.g. baud rate, polling list/slave addresses)
●
Failure of the master system
Master monitoring is also referred to as a process timeout because it operates based on the
user data received at the application level. The parameter p2040 defines the monitoring time
in ms. If no user data is received within this period, the sequential control assumes the
"S1:Z_switching on inhibited" state (see Figure 4-4 Sequential control state graph
(Page 149)). Monitoring can be deactivated by setting the parameter p2040 to "0". The
master cycle time and the type of telegram communication must be considered when
configuring the monitoring time. The occurrence of a process timeout is visualized by the
status code "y". A master timeout does not need to be acknowledged because it is only to be
evaluated as an alarm. A process timeout error is subject to an off delay of 2 s.
Summary of Contents for SIDOOR ATD401W
Page 1: ......