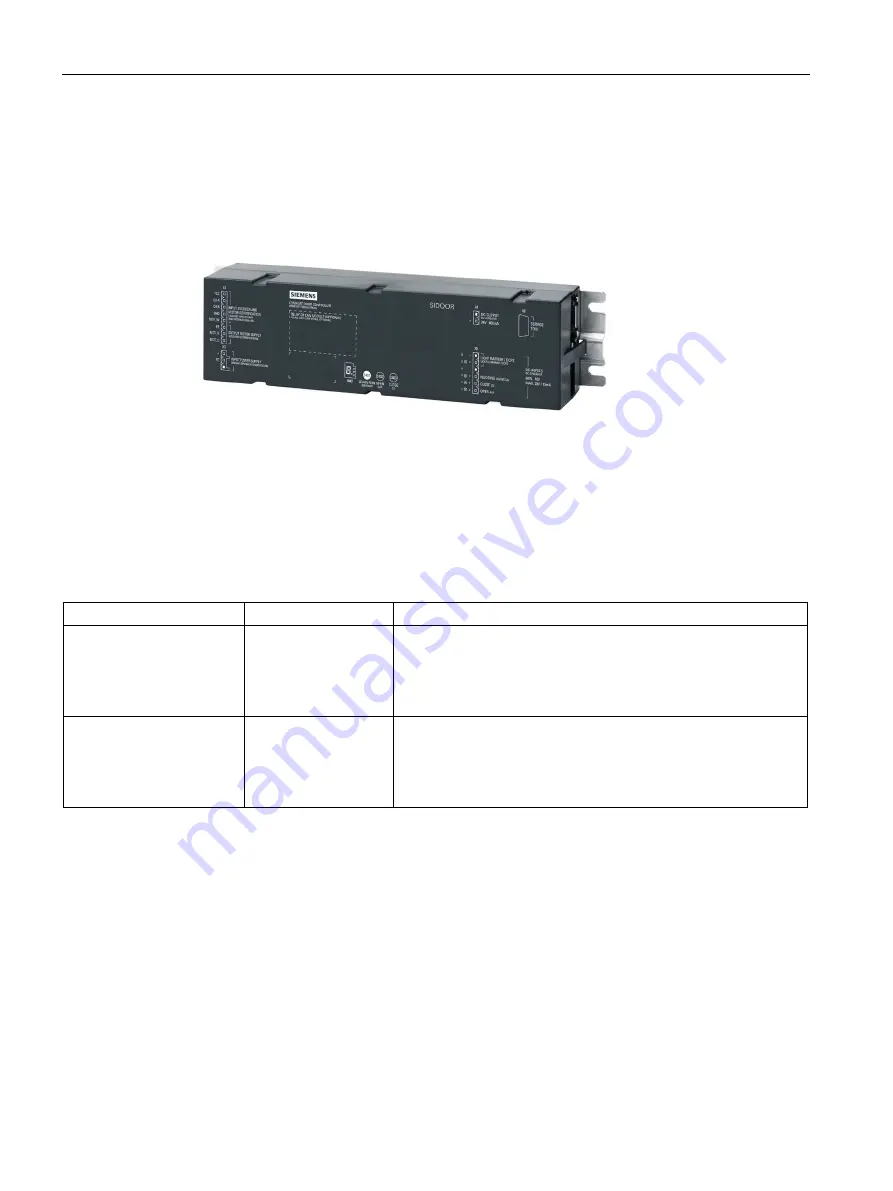
Product family
3.2 Products
ATE500E
14
System Manual, 09/2017, A5E33917696-AD
3.2
Products
3.2.1
Controllers
Controllers are electronic control systems that are connected to the power supply unit
through an external power supply unit. They are generally connected to the higher-level
controller via digital or fieldbus interfaces, and can be configured via a user interface.
The controllers are designed for different areas of application. The following table provides
an overview of the available controllers.
Versions
Product
Article No.
Description
SIDOOR ATE500E RELAY 6FB1211-5AT10-7AT2
•
Controller for elevator doors, horizontal
•
Dynamic door weights of up to 280 kg can be driven with the
SIDOOR MED280 motor.
•
Relay module
SIDOOR ATE500E CAN
6FB1211-1AT10-7AT3
•
Controller for elevator doors, horizontal
•
Dynamic door weights of up to 280 kg can be driven with the
SIDOOR MED280 motor.
•
Serial interface to the higher-level controller (CAN module)