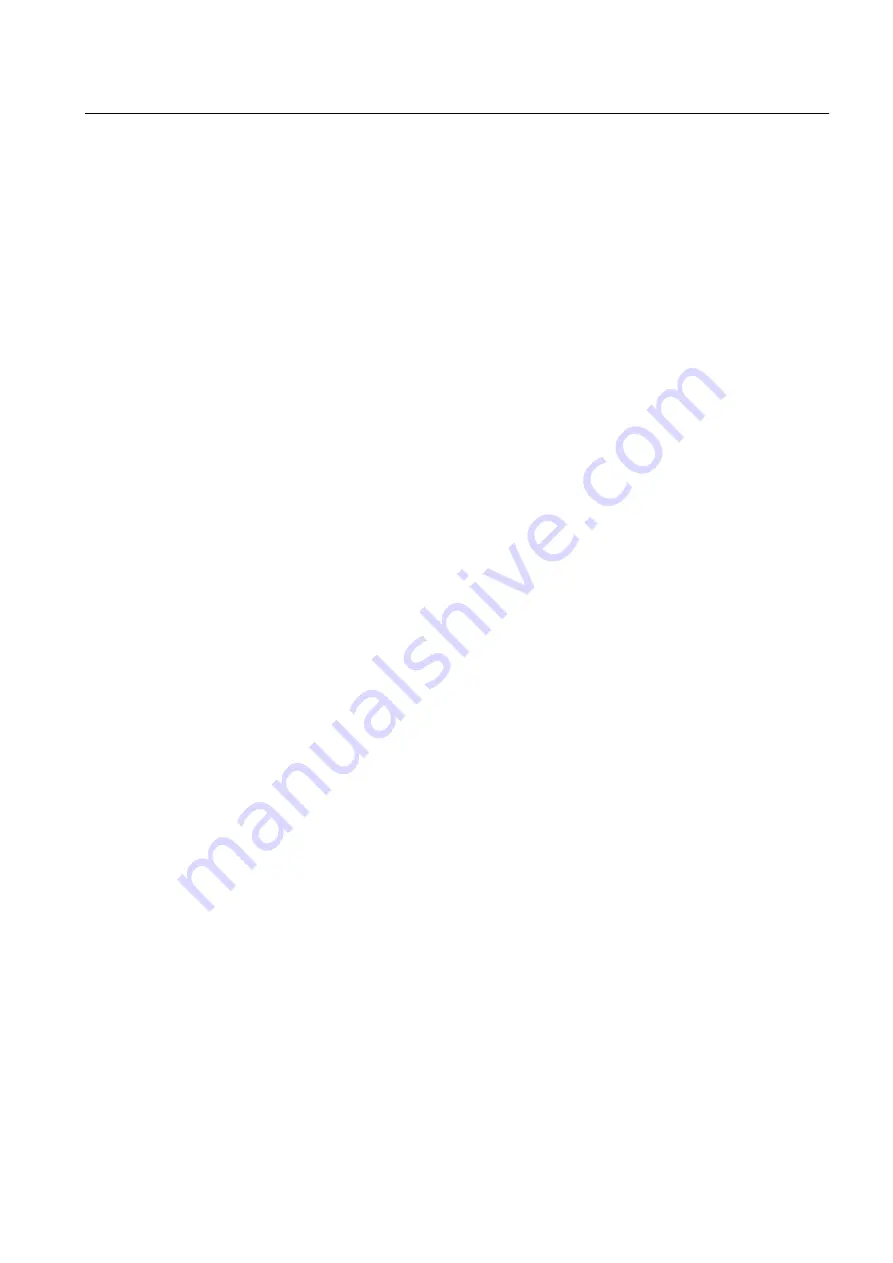
5.3.2
Selecting fixing screws
● Unless specified otherwise, use mounting bolts with at least strength class 8.8 to ISO 898‑1.
In this way you guarantee that the machine is securely mounted and the forces can be
transferred through the torque.
● Take into account the maximum forces occurring in the case of a fault such as short circuit
or system transfers in phase opposition.
– When selecting the bolts
– When designing the foundation
5.3.3
Preconditions for smooth, vibration-free operation
Preconditions for smooth, vibration-free operation:
● Stable foundation design
● Precise alignment of the machine
● Correct balancing of parts to be fitted to the shaft end.
● Maintaining the vibration velocity according to ISO 10816‑3
5.3.4
Aligning the machine to the driven machine and attaching it to it (foundation
mounting)
1. Refer to any instructions for aligning the driven machine and those of the coupling
manufacturer.
2. Align the machines with coupling output to the driven machine in such a manner that the
center lines of the shafts at the operating temperature do not have any parallel or angular
offset. This ensures that no additional forces affect their bearings during operation.
If the thermal change of the motor and the driven machine is different, couple in the cold
state with an appropriate alignment offset. The alignment offset to be set in the cold state
must be determined and specified by the system specialist.
3. For the vertical positioning (x→0), place thin shims over a large surface area under the
machine feet. The number of shims should be kept as low as possible, i.e. stack as few as
possible. This also prevents the machine being subjected to any stress/distortion. Use the
existing tapped holes for the forcing-off bolts to raise the machine.
The balance state of the shaft (full-key or half-key balancing) and alignment errors primarily
influence the service life of the bearing, especially for high motor speeds or when using
rigid couplings.
Assembling
5.3 Installing the machine
SIMOTICS DC 1GG6
Operating Instructions 02/2016
47
Summary of Contents for SIMOTICS DC 1GG6
Page 2: ...08 02 2016 10 27 V4 00 ...
Page 12: ...Table of contents SIMOTICS DC 1GG6 12 Operating Instructions 02 2016 ...
Page 14: ...Introduction 1 1 About these instructions SIMOTICS DC 1GG6 14 Operating Instructions 02 2016 ...
Page 70: ...Commissioning 7 8 Switch off SIMOTICS DC 1GG6 70 Operating Instructions 02 2016 ...
Page 82: ...Operation 8 9 Faults SIMOTICS DC 1GG6 82 Operating Instructions 02 2016 ...
Page 104: ...Maintenance 9 2 Repair SIMOTICS DC 1GG6 104 Operating Instructions 02 2016 ...
Page 138: ...Service and Support SIMOTICS DC 1GG6 138 Operating Instructions 02 2016 ...
Page 142: ...Quality documents SIMOTICS DC 1GG6 142 Operating Instructions 02 2016 ...
Page 153: ......