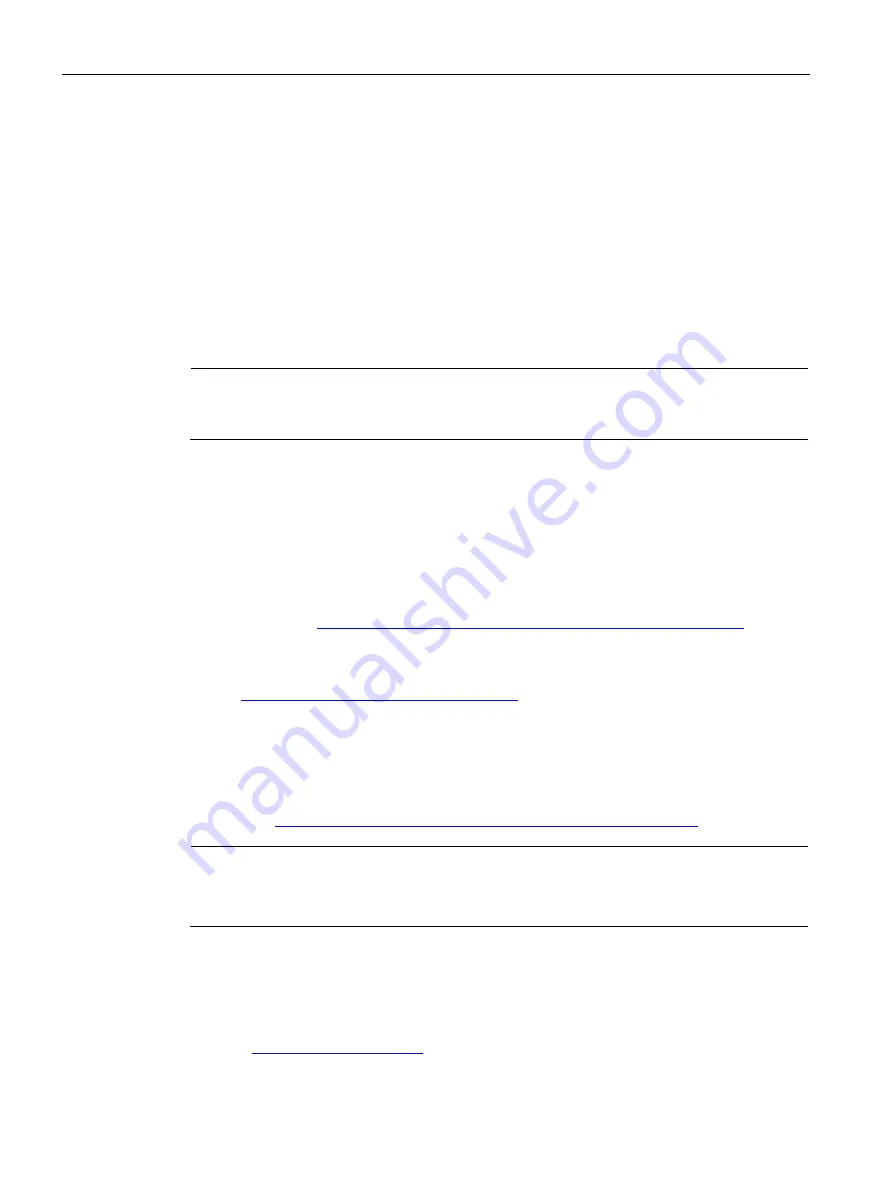
Introduction
SIMOTICS S-1FT2 synchronous motors for SINAMICS S120
4
Operating Instructions, 07/2021, A5E50610821B AB
Operating instructions without a specified sequence are identified using a bullet point:
•
Execute the operating instructions.
Enumerations
•
Enumerations are identified by a bullet point without any additional symbols.
–
Enumerations at the second level are hyphenated.
Notes
Notes are shown as follows:
Note
A Note is an important item of information about the product, handling of the product or the
relevant section of the document. Notes provide you with help or further suggestions/ideas.
More information
Information on the following topics is available at:
•
Ordering documentation / overview of documentation
•
Additional links to download documents
•
Using documentation online (find and search in manuals / information)
More information (
https://support.industry.siemens.com/cs/ww/en/view/108998034
If you have any questions regarding the technical documentation (e.g. suggestions,
corrections), please send an e-mail to the following address:
E-mail (
mailto:docu.motioncontrol@siemens.com
My support
Information on how to produce individual contents for your own machine documentation
based on Siemens contents is available under the link:
My support (
https://support.industry.siemens.com/My/ww/en/documentation
Note
If you want to use this function, you must register once.
Later, you can log on with your login data.
Training
The following link provides information on SITRAIN - training from Siemens for products,
systems and automation engineering solutions:
SITRAIN (