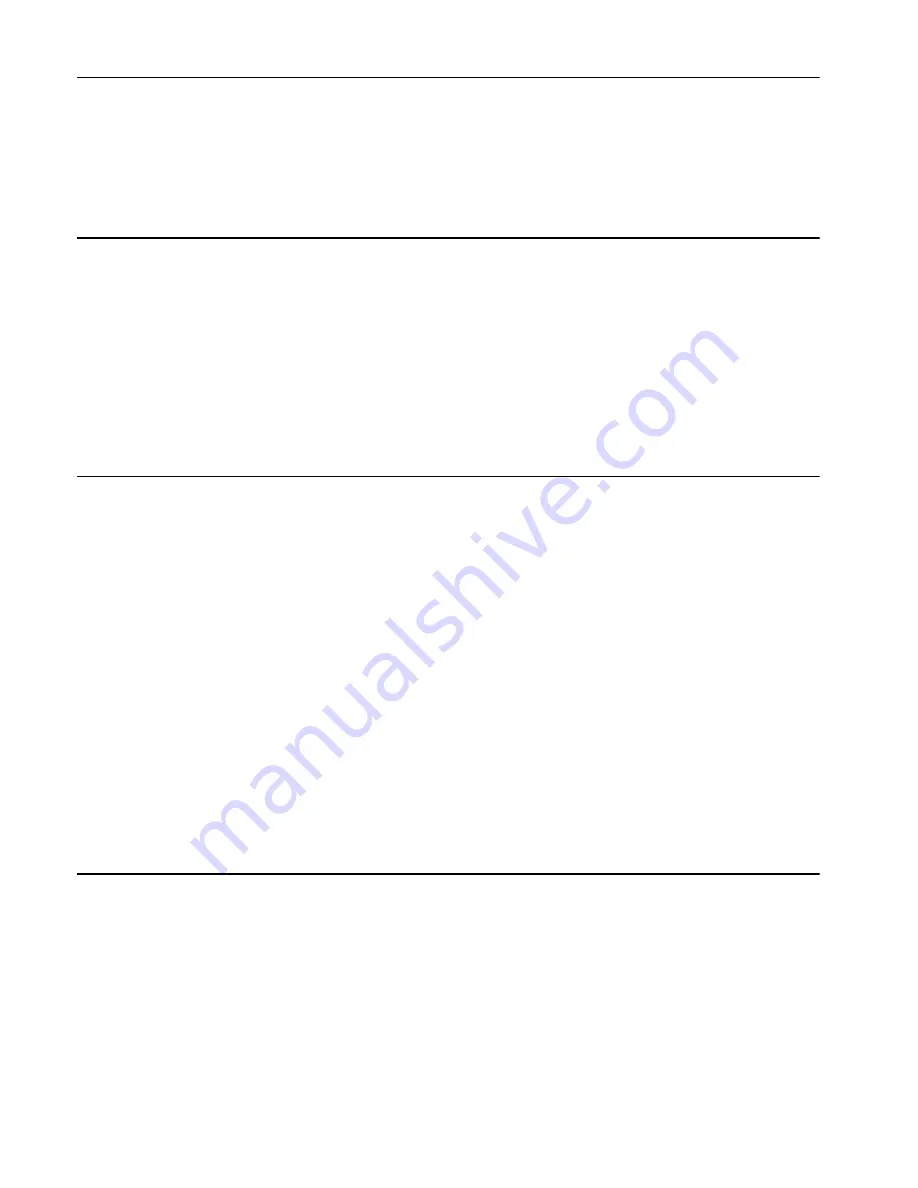
Explanation:
The Auto-Repos function (operating mode) was selected in the channel but is not implemented.
Reaction:
Alarm display.
Remedy:
This message is purely informational.
Programm
continuation:
Clear alarm with the Delete key or NC START.
10600
[Channel %1: ] Block %2 auxiliary function during thread cutting active
Parameters:
%1 = Channel number
%2 = Block number, label
Explanation:
An auxiliary function output is programmed in a thread cutting block.
Reaction:
Alarm display.
Remedy:
Consequential errors can occur if the machining path of the thread block is too short and further blocks (thread blocks)
follow in which no machining stop may occur.
Possible remedial measures:
- Program a longer path and/or a lower traversing rate.
- Output auxiliary function in another block (program section).
Programm
continuation:
Clear alarm with the Delete key or NC START.
10601
[Channel %1: ] Block %2 zero velocity at block end point during thread cutting
Parameters:
%1 = Channel number
%2 = Block number, label
Explanation:
This alarm occurs only when several blocks with G33 follow in succession. The block end velocity in the specified block
is zero, although a further thread cutting block follows. The reasons for this can be, for instance:
- G9
- Auxiliary function after motion
- Auxiliary function output before the motion of the following block
- Positioning axis in the block
Reaction:
Interpreter stop
NC Start disable in this channel.
Interface signals are set.
Alarm display.
Remedy:
Modify the NC part program by removing any programmed "Stop at end of block" G09.
Modify general MD11110 $MN_AUXFU_GROUP_SPEC [n] for selecting the output time of an auxiliary function group by
changing "Auxiliary function output before/after the movement" to "Auxiliary function output during the movement".
Bit 5 = 1: Auxiliary function output before movement
Bit 6 = 1: Auxiliary function output during movement
Bit 7 = 1: Auxiliary function output after movement
Programm
continuation:
Clear alarm with the RESET key. Restart part program
10604
[Channel %1: ] Block %2 thread pitch increase too high
Parameters:
%1 = Channel number
%2 = Block number, label
Explanation:
The thread pitch increase is causing an axis overload. A spindle override of 100% is assumed during verification.
Reaction:
Correction block is reorganized.
Local alarm reaction.
Interface signals are set.
Alarm display.
Remedy:
Reduce the spindle speed, thread pitch increase or path length in the NC program.
SINUMERIK 808D ADVANCED alarms
5.2 NCK alarms
Diagnostics Manual
98
Diagnostics Manual, 06/2015, 6FC5398-6DP10-0BA2