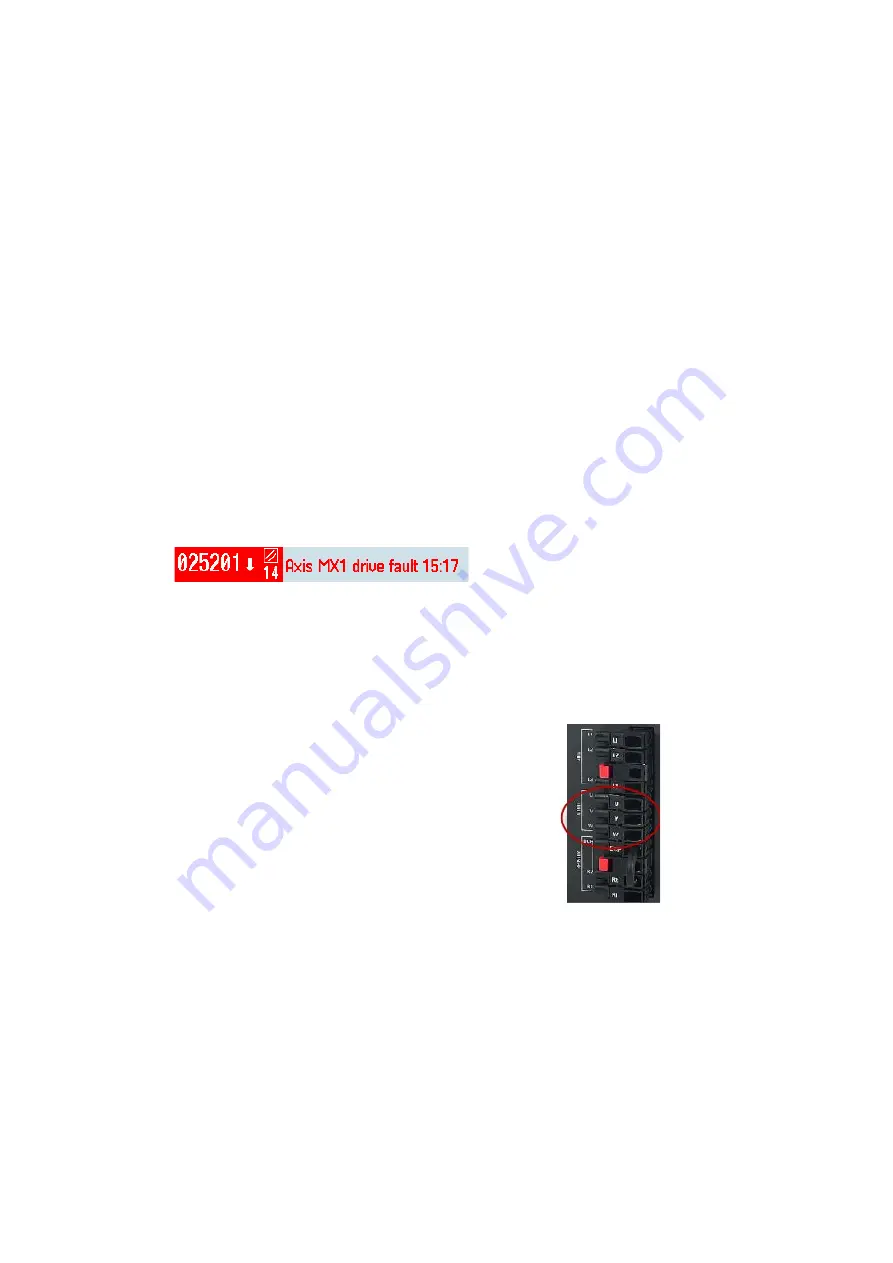
Service Manual
22
01/2017
Case 4
1.
Check whether the deceleration switches cannot bounce back.
2.
Check whether there is connection fault of the deceleration switches.
Case 5
Check whether the machine data MD34000 is set correctly (the deceleration switches are not available when MD34000 = 0).
Case 6
1.
Check whether the machine approaching switch and its related connections are damaged.
2.
Check whether the machine data MD34060 is set properly.
3.
Check whether the encoder corresponding to the feed axis and its related connections are damaged.
Case 7
Check whether the machine data MD30200 is set correctly (the system cannot approach the reference point when MD30200
= 0).
Case 8
1.
Check whether the machine data MD31020 is set correctly.
2.
Alternatively adjust the reference cam switch by 2 mm to 3 mm.
3.17
Drive alarm
Fault description
Case 1:
The control system issues a drive-related alarm.
Case 2:
The drive also issues an alarm, normally A05/A06/A07/A08/A09 for the SINAMICS V60 drive, and
F30001/F30002/F31117 for the SINAMICS V70 drive.
Diagnostic steps
A05/A06/F30001: IGBT or internal chip overcurrent
It may appear when the main power supply is connected/during motor operation.
1.
Check the U, V, W, and PE connections on the drive for the following:
•
Whether connections between different phases are short-circuited
•
Whether a U, V, or W phase is disconnected
•
Whether the grounding connection is incorrect or has bad grounding
•
Whether the wires are damaged
2.
Power on again and observe whether the fault still exists after verification.
3.
If the fault still exists after the above operation, check the insulation of the motor and see if it is damaged. The motor
can be changed when necessary. Then power on again and observe whether the fault still exists.
4.
Replacement and maintenance are necessary if the fault still exists after the above inspection, because probably the
drive is damaged.
A07/F30002: ground connection short-circuited
It may appear when the main power supply is connected/during motor operation.
1.
Check the U, V, W, and PE connections on the drive to see whether the connections among different phases are
short-circuited.
Summary of Contents for SINUMERIK 808D
Page 30: ...Service Manual 30 01 2017 Notes ...