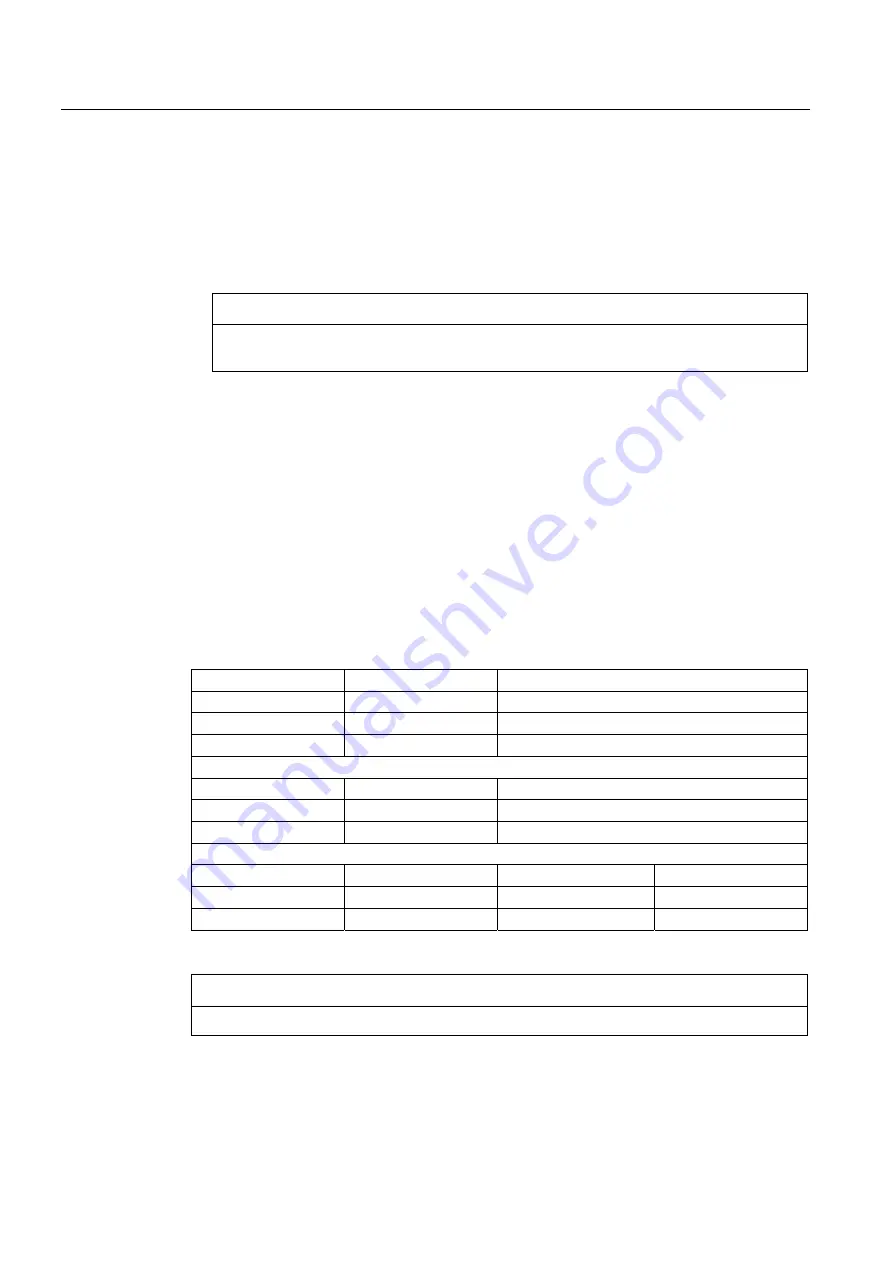
PROFIBUS DP Communication
8.7 DP slave MCP 483
Manual
280
Commissioning Manual, 05/2008, 6FC5397–4CP10–4BA0
8.7.5
Linking to the basic PLC and user program
The chapter describes the principal linking of the MCP 483 DP slave
●
to the PLC basic program for transferring the standard I/O data to the VDI interface
●
to the PLC user program (optional) to implement a user-specific response to a module
failure
NOTICE
Processing of additional I/O data is the sole responsibility of the user (machine
manufacturer) and is not supported by the PLC basic program.
PLC basic program
To transfer the standard I/O data of the MCP 483 DP slave via the PLC basic program, the
corresponding I/O range must be entered in the communication parameters of the FB1
function block.
Function block FB1
The communications parameters of the MCP are called MCPx... (x = 1 or 2) in function block
FB1. A maximum of 2 machine control panels are supported by the basic PLC program.
To synchronize several MCPs, the PLC program must be adapted accordingly. This is the
user's (machine manufacturer's) responsibility.
The following parameters are relevant, if you want to operate a machine control panel MCP
483 as DP slave in a SINUMERIK 840Di sl:
MCPNum:
INT
// Number of MCP
MCP1In:
POINTER
// Address of input signals
MCP1Out:
POINTER
// Address of output signals
MCP1BusAdr
Byte
// PROFIBUS address of the MCP DP slave
The MCP2... parameters are only needed if a 2nd MCP is used in addition to the 1st MCP:
MCP2In:
POINTER
// Address of input signals
MCP2Out:
POINTER
// Address of output signals
MCP2BusAdr
Byte
// PROFIBUS address of the MCP DP slave
Bus type via which the MCP is connected:
MCPBusType
Byte
// MPI
= 0
// PROFIBUS
= B#16#33
// Ethernet
= B#16#55
NOTICE
Parameters: MCPxStop and MCPxNotSend are of no significance.
References:
For a detailed description of the PLC basic program or of function block FB 1, please refer to: