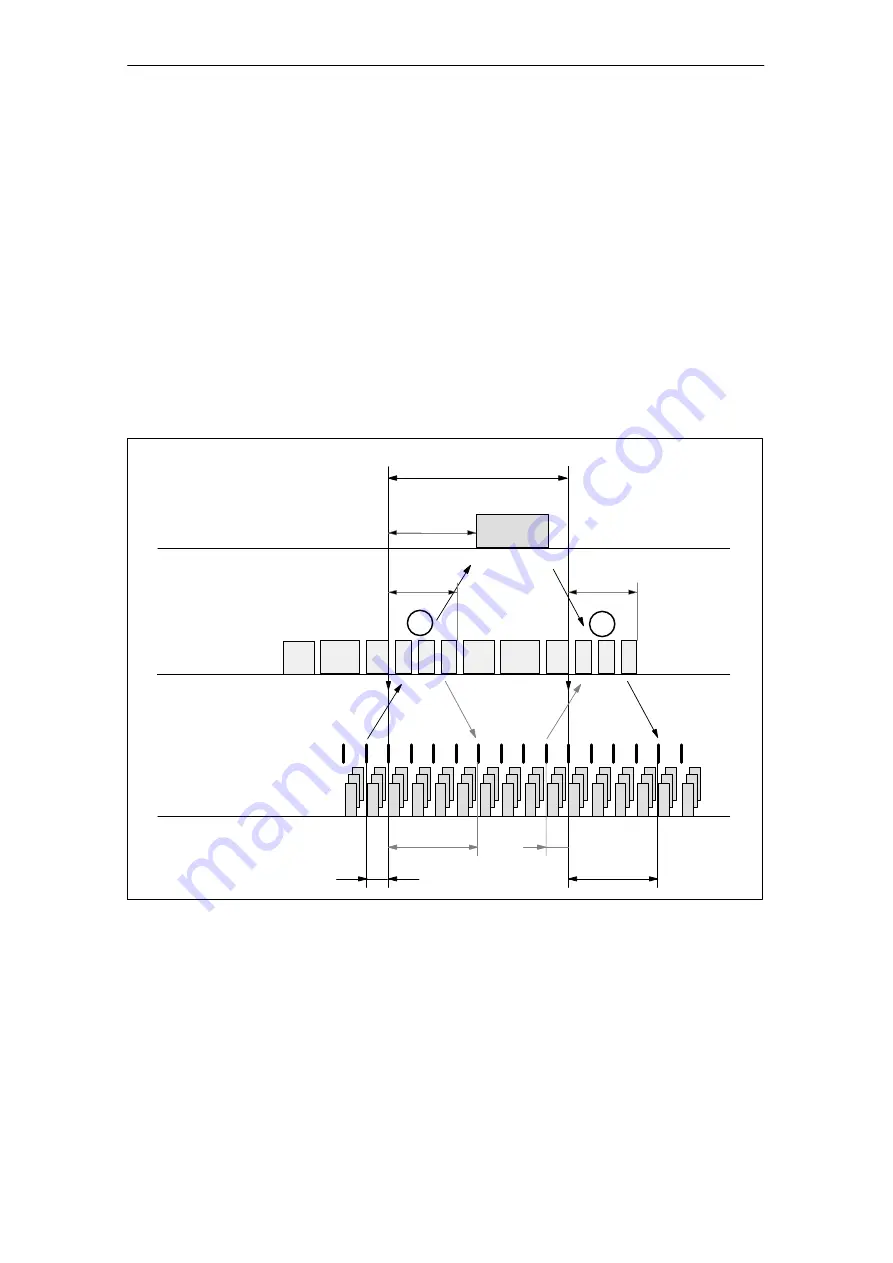
06.03
7.1 General
7-205
Siemens AG, 2003. All rights reserved
SINUMERIK 840Di Manual (HBI) – 06.03 Edition
7.1.2
Description of a DP cycle
At the time T
I
, all equidistant drives (DP slaves) read in the current actual posi-
tion values. In the next DP cycle, at time T
DX
, the actual values are transferred
to the DP master.
At the time T
M,
with T
M
> T
DX,
the NC position controller is started, calculating
the new speed setpoints using the actual position values transferred.
At the beginning of the next DP cycle at time T
DX
, the speed setpoints are trans-
ferred from DP master to the DP slaves (drives).
At the time T
O
, the speed setpoints are accepted by all servo drive controls as
the new default.
Dx
Dx
Dx
GC
RGT
DPV1
Dx
Dx
Dx
Speed
controller cycle
Drives:
DP slave: 1 to 3
NC:
Master or position
controller
T
I
T
M
T
O
T
MAPC =
T
DP
RGT
GC
T
DX
R
PROFIBUS DP
communication
1
2
T
DX
R
R
R
R
R
R
R
R
R
R
R
R
R
R
R
R
DPV1
T
O
TI
Fig. 7-2
Example: Optimized DP cycle with 3 DP slaves 611U
Explanations regarding Fig. 7-2:
T
MAPC
Master Application Cycle: NC position controller cycle
With SINUMERIK 840Di, the following applies in all cases: T
MAPC
= T
DP
T
DP
DP cycle time: DP cycle time
T
DX
Data Exchange Time: Total of transfer times of all
DP slaves
Actual values
Position controller
Setpoints
7 PROFIBUS DP Communication