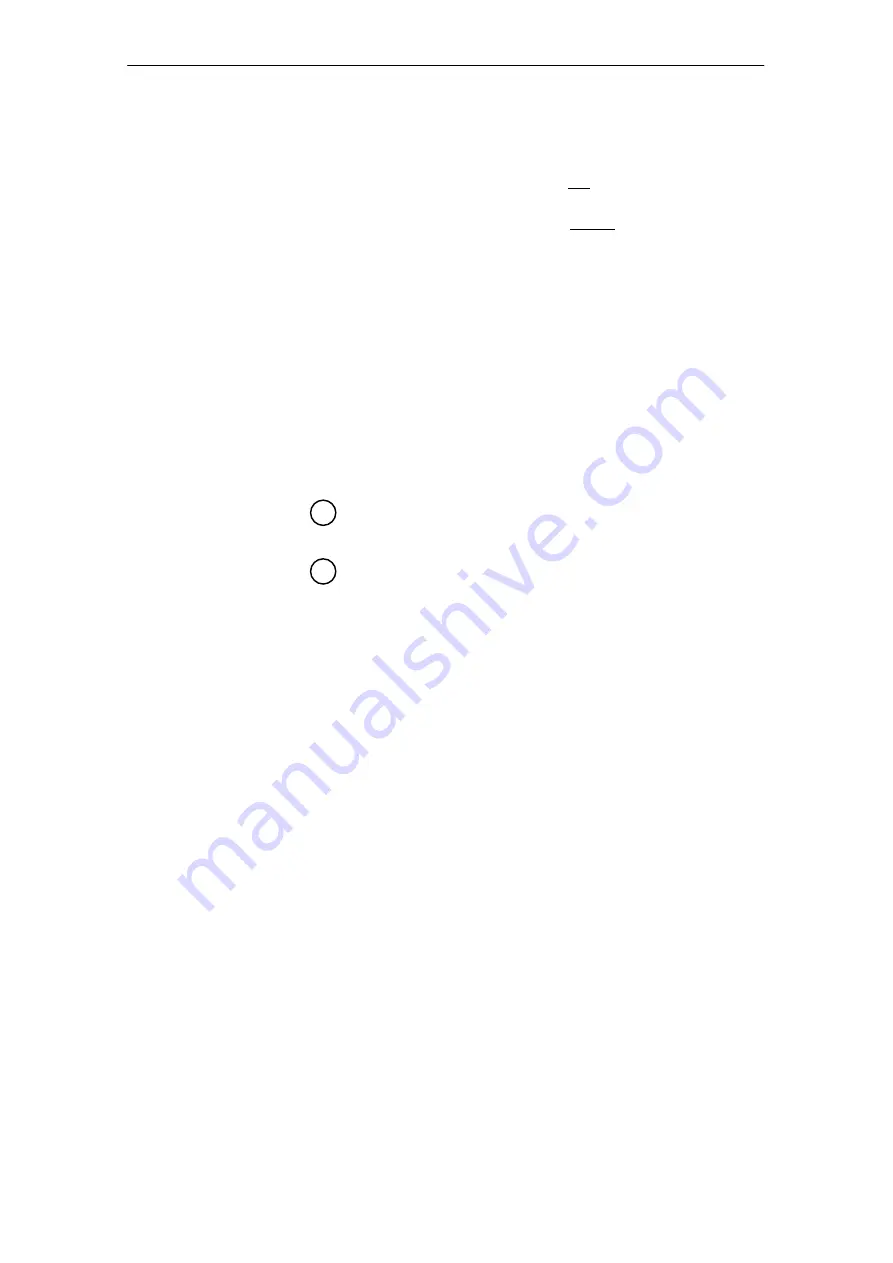
06.03
7.1 General
7-206
Siemens AG, 2003. All rights reserved
SINUMERIK 840Di Manual (HBI) – 06.03 Edition
T
M
Master Time: Shift of starting time of the NC position control
T
I
Input Time: Time of actual-value sensing The actual values are
transferred to the DP master in the next DP cycle.
T
O
Output Time: Time of setpoint acceptance. The setpoints were created
by the DP master application in the previous DP cycle.
GC
Global Control Message Frame Type (Broadcast Message Frame) for
cyclic synchronization of the isosynchronism between DP Master and
DP slaves
R
Computing time of speed and/or position controller
Dx
User data exchange between DP master and DP slaves
DPV1
After cyclic communication an acyclic service is sent, if the token holding
time T
TH
was not exceeded. T
TH
is calculated by the configuring system.
GAP
An attempt is made during GAP to accept new active stations.
TOKEN
Token passing is either performed from the station to itself or to other
masters.
RES
The reserve is used as an “active pause” for the station to send the token
to itself until the equidistant cycle is terminated.
1
The actual values for the current DP cycle/position controller cycle are
transferred from the DP slave drives to the NC position controller.
2
The setpoints calculated by the NC position controller are transferred to
the DP slave drives.
7.1.3
SINUMERIK 840Di with PROFIBUS DP
The configuration of PROFIBUS DP is carried out within the framework of a
SIMATIC S7 project (further referred to as S7 project).
To create an S7 project for a SINUMERIK 840Di, the following components are
needed:
S
SIMATIC Manager STEP7
S
SINUMERIK 840Di
S
Programming device/PC with MPI connection (e.g. PG740) and MPI cable
(not required if the SIMATIC Manager is installed on the SINUMERIK 840Di)
S
Basic PLC program
S
840Di rack
(a SIMATIC S7-300 station preconfigured for SINUMERIK 840Di)
S
DriveOM/SlaveOM.
PROFIBUS DP and
SIMATIC S7
7 PROFIBUS DP Communication