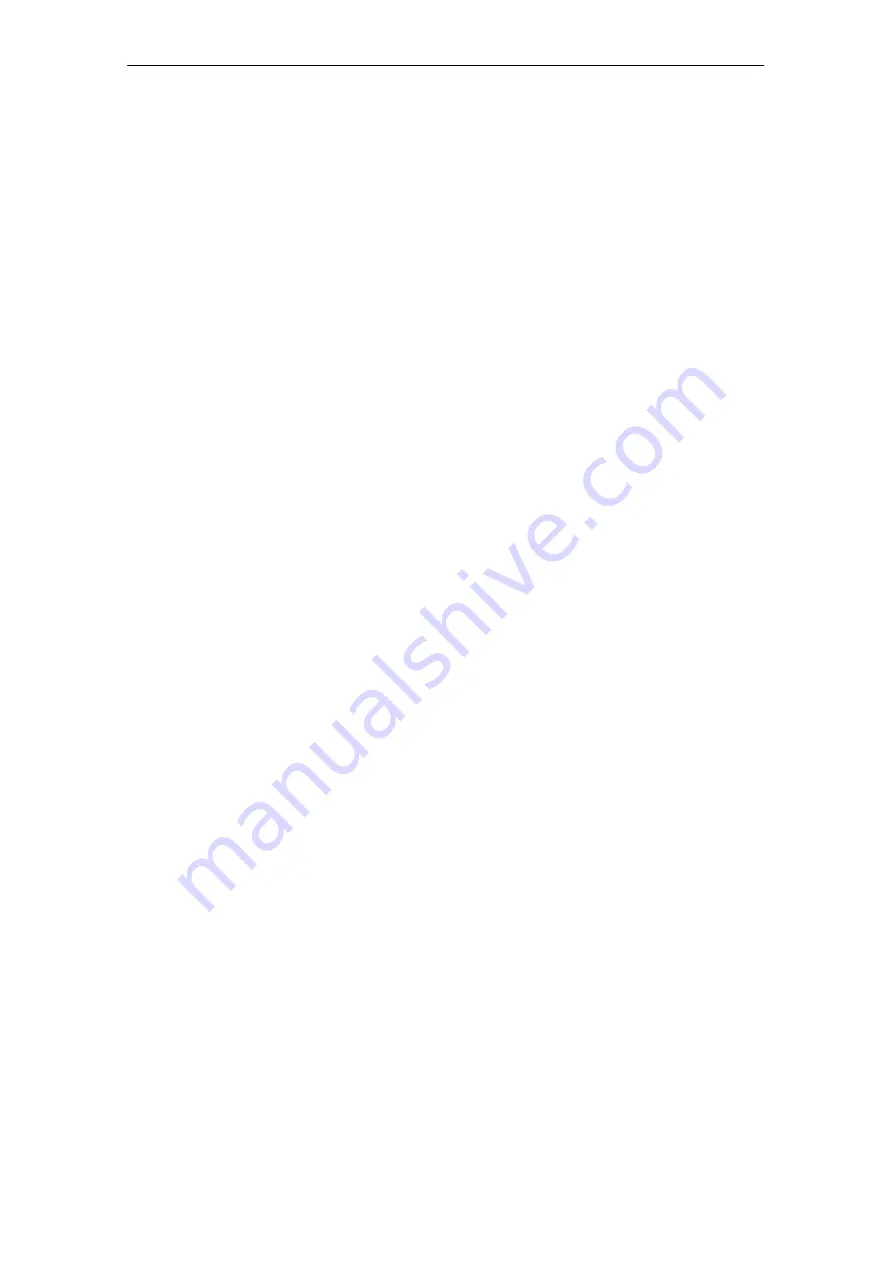
06.03
10.3 System data
10-291
Siemens AG, 2003. All rights reserved
SINUMERIK 840Di Manual (HBI) – 06.03 Edition
Explanations regarding Fig.10-2:
T
Pos
Computational time required by the position controller
T
DP
DP cycle time: DP cycle time
T
DX
Data exchange time: Total of transfer times of all
DP slaves
T
M
Master time: Shift of starting time of the NC
position control
GC
Global Control: Broadcast message frame for cyclic
synchronization of the isosynchronism between DP master
and DP slaves
R
Computational time
Dx
User data exchange between DP master and DP slaves
MSG
Acyclic services (e.g. DP/V1, token transfer)
RES
Reserve: “active break” until the equidistant cycle has elapsed
S
MD10062 POSCTRL_CYCLE_DELAY (position control cycle offset)
The following setting is recommended as the orientation value for the position
control cycle offset:
T
M
= T
DP
– 3*T
pos max
–
T
DP
The DP cycle time is equivalent to position controller cycle of the SINUMERIK
840Di
–
T
pos max
Display using HMI Advanced (Option):
Operating area switchover > Diagnosis > Service displays >
System resources
Error response
S
Alarm: “380005 PROFIBUS DP: Bus access conflict, type t, counter z”
Error causes/remedy
S
t = 1
The position controller cycle offset has been chosen too small. The cyclic
PROFIBUS DP communication with the drives was not yet completed with
the start of the position controller.
Remedy: Increasing the position controller cycle offset.
S
t = 2
The position controller cycle offset has been chosen too large. The cyclic
PROFIBUS DP communication with the drives started before the position
controller was completed. The position controller requires more
computational time than available within the DP cycle.
–
Remedy: Reducing the position controller cycle offset
or
–
Remedy: increasing the DP cycle time.
The DP cycle time is set using STEP7 “HW Config”. See Section 7.3,
page 7-211f.
10 NC Start-Up with HMI Advanced