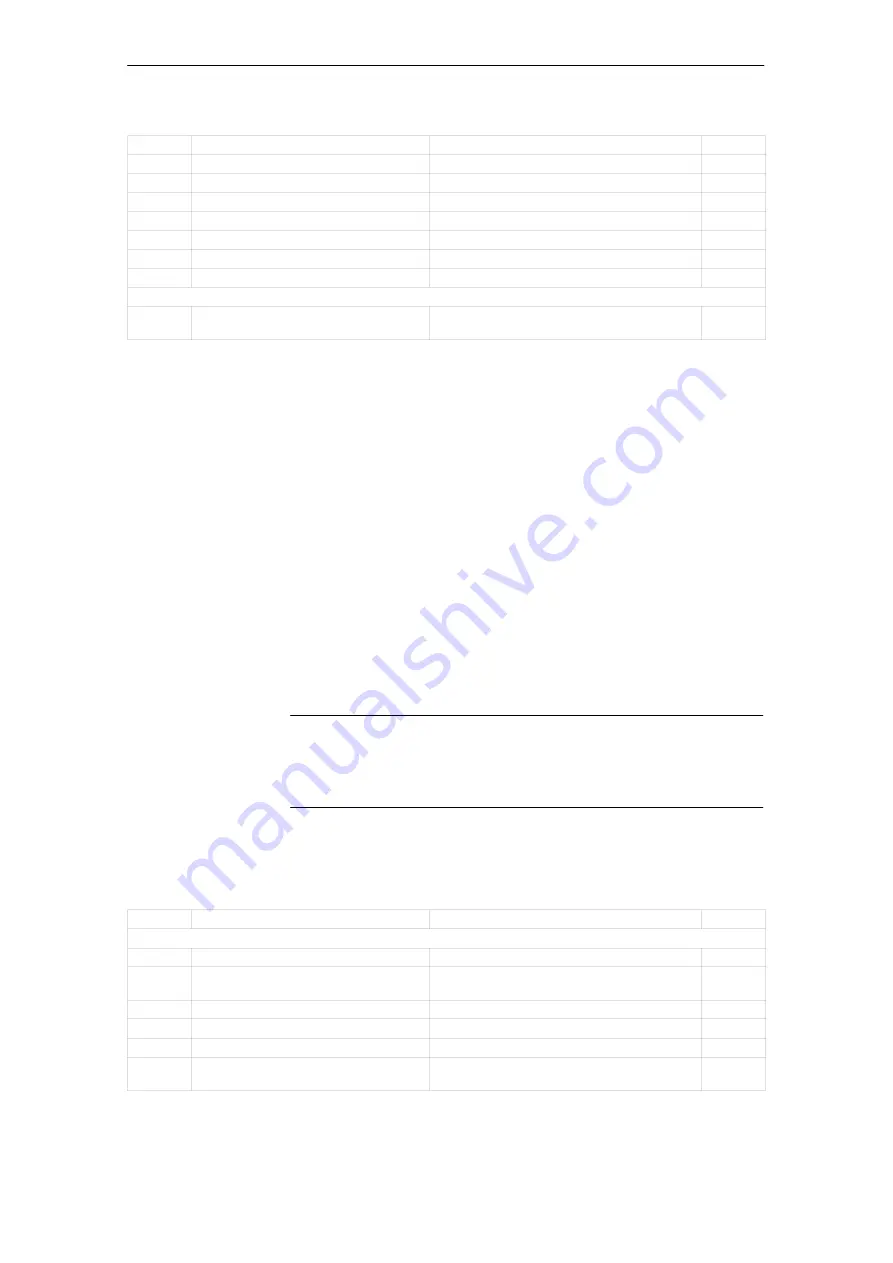
06.03
10.4 Memory configuration
10-298
Siemens AG, 2003. All rights reserved
SINUMERIK 840Di Manual (HBI) – 06.03 Edition
Number
Ref.
Name/remarks
Identifier
28090
MM_NUM_CC_BLOCK_ELEMENTS
Number of block elements for Compile cycles
28100
MM_NUM_CC_BLOCK_USER_MEM
Size of block memory for Compile cycles
28105
MM_NUM_CC_HEAP_MEM
Heap memory for compile cycle applications
28210
MM_NUM_PROTECT_AREA_ACTIVE
Number of simultaneously active protection zones
/FB/, A3
28500
MM_PREP_TASK_STACK_SIZE
Stack size of preparation task
28510
MM_IPO_TASK_STACK_SIZE
Stack size of IPO task
28550
MM_PRSATZ_MEM_SIZE
Available memory for internal blocks
Axis-specific ($MA_ ...)
38010
MM_QEC_MAX_POINTS
Number of values for quadrant error
compensation
/FB/, K3
/IAD/
10.4.2
SRAM memory
The free SRAM memory is displayed in machine data
S
MD18060: INFO_FREE_MEM_DYNAMIC (free static memory).
The free SRAM should not be less than 15,000 bytes to ensure that data (e.g.
tool offsets) can be read in at all times.
Modifying the machine data listed in Table 10-14 results in a reconfiguration of
the SRAM with a loss of all user data. Before the change comes into effect in
the NC, the following alarm message is output:
S
Alarm: “4400 MD change results in reorganization of the non–volatile
memory (loss of data!)”
Notice
When reconfiguring the SRAM memory, all user data are lost. To prevent data
loss, a series machine start-up file should be created prior to reconfiguration
(see Section 14.2, Page 14-451).
Table 10-14
Machine data required to configure the SRAM
Number
Identifier
Name/remarks
Ref.
General ($MN_ ...)
18060
INFO_FREE_MEM_STATIC
Display data of the free static memory
18080
MM_TOOL_MANAGEMENT_MASK
Screen form for reserving memory for the tool
management
/FBW/
18082
MM_NUM_TOOL
Number of tools managed by NCK
18084
MM_NUM_MAGAZINE
Number of magazines managed by NCK
/FBW/
18086
MM_NUM_MAGAZINE_LOCATION
Number of magazine locations
/FBW/
18090
MM_NUM_CC_MAGAZINE_PARAM
Compile cycles of tool management: Number of
magazine data
/FBW/
Free memory
Reconfiguration of
the SRAM
Machine data
10 NC Start-Up with HMI Advanced