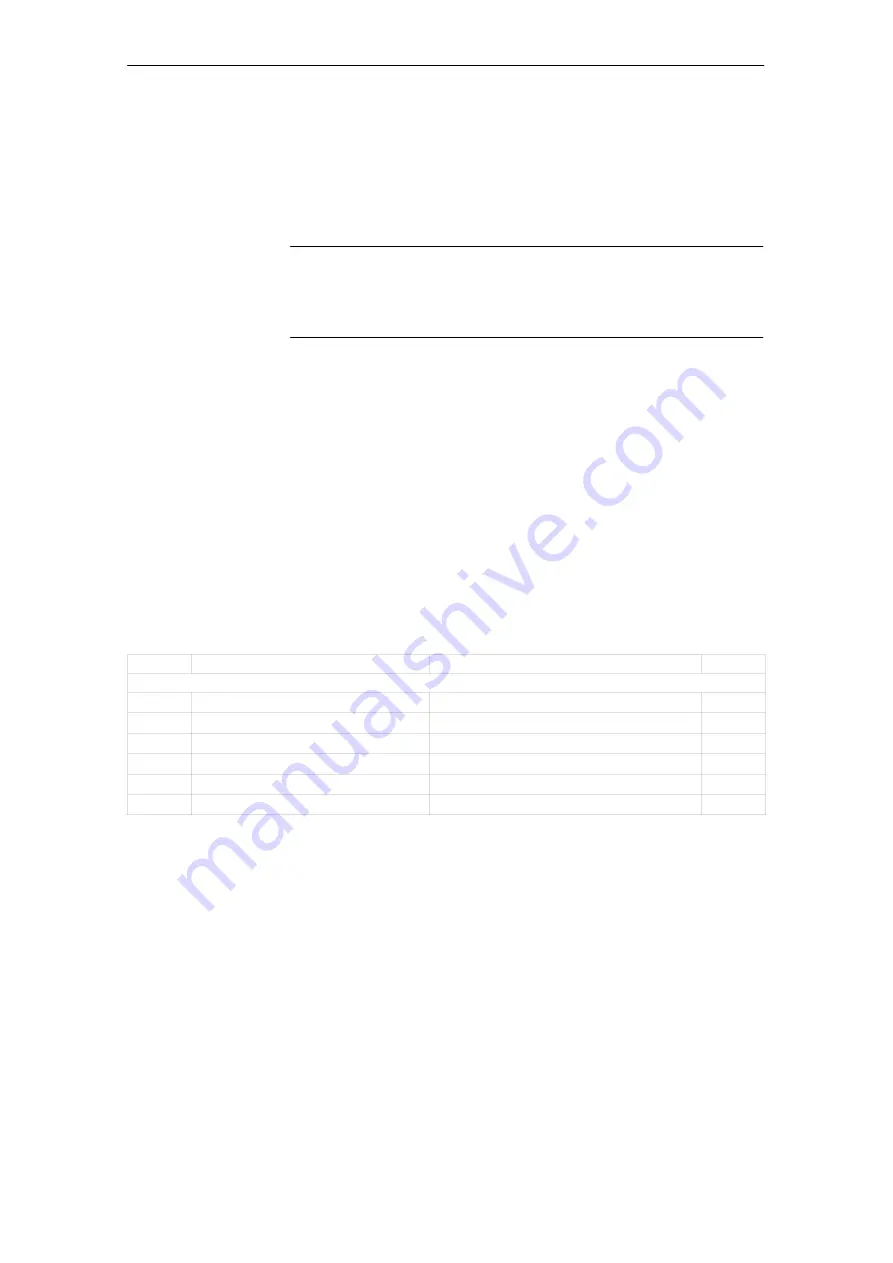
06.03
10.5 Axes and spindles
10-335
Siemens AG, 2003. All rights reserved
SINUMERIK 840Di Manual (HBI) – 06.03 Edition
The sign of a properly adjusted acceleration of a machine axis is acceleration
and positioning free from overshoot at rapid traverse rate and maximum load
(heavy workpiece).
After the acceleration has been entered, the axis is traversed rapidly and the
actual current values and current setpoint are recorded.
Note
With SIMODRIVE 611 universal drives, the current actual value and the current
setpoint can be recorded using the SimoCom U start-up tool (trace function).
For further information, please refer to the online help of SimoCom U.
This recording shows whether the drive reaches the current limit. During this,
the current limit can be reached for a short time.
However, the current must be well below the current limit before the rapid tra-
verse velocity or the final position is reached.
Slight load changes during machining must not cause the current limit to be
reached. Excessive current during machining causes falsification of the contour.
For this reason, the acceleration value should be a little bit less than the maxi-
mum acceleration value.
Machine axes can have different acceleration values, even if they interpolate
with each other.
Table 10-34
Position control: Machine data
Number
Identifier
Name/remarks
Ref.
Axis-specific ($MA_ ...)
32100
AX_MOTION_DIR[n]
Traversing direction
32110
ENC_FEEDBACK_POL
[n]
Sign of actual value
32200
POSCTRL_GAIN[n]
Servo gain
32300
MAX_AX_ACCEL[n]
Axis acceleration
32900
DYN_MATCH_ENABLE[n]
Dynamic adaptation
32910
DYN_MATCH_TIME[n]
Time constant of dynamic adaptation
/FB/
Description of Functions, Basic Machine,
G2 Velocities, Setpoint/Actual-Value Systems, Closed-Loop Control,
Section: Closed loop control
Checking the
acceleration
Machine data
References
10 NC Start-Up with HMI Advanced