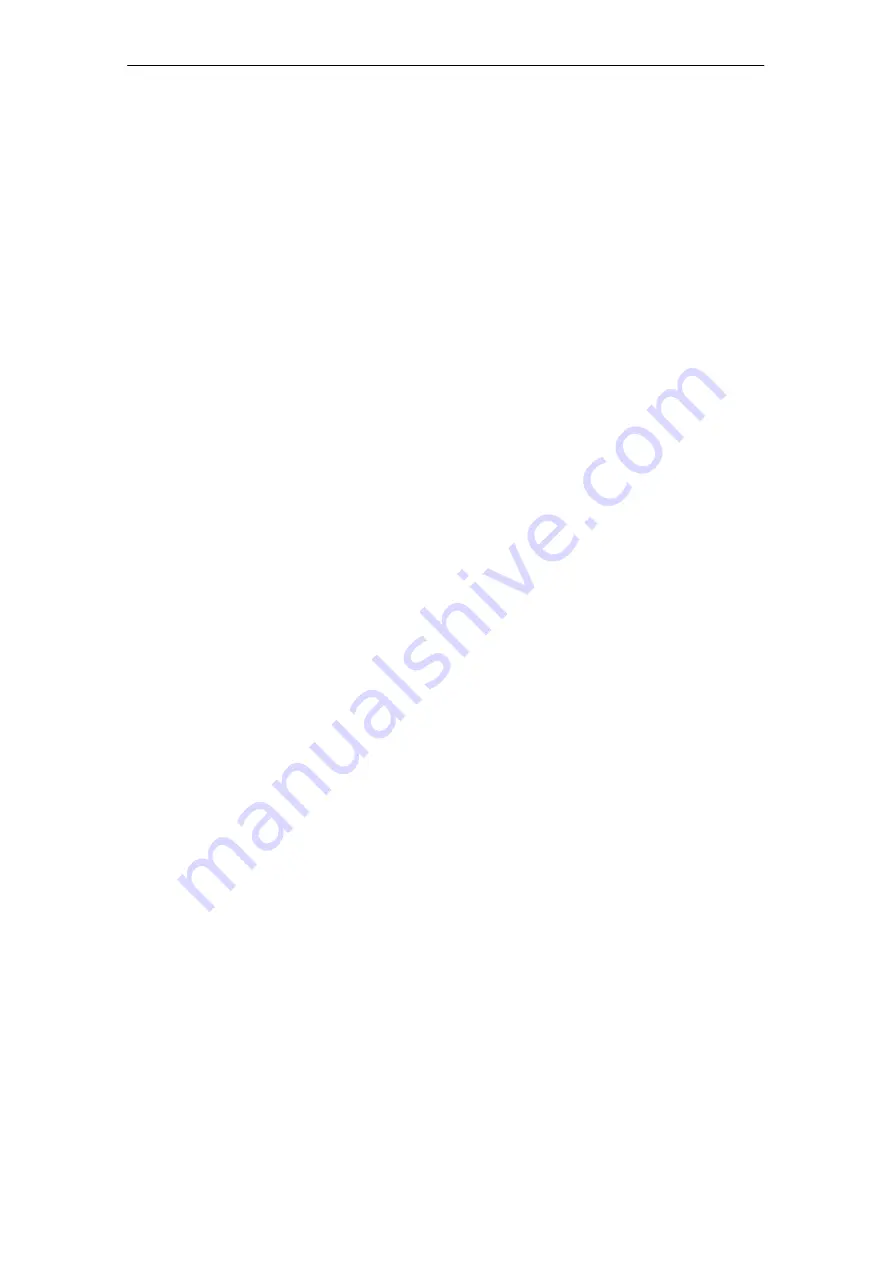
06.03
10.5 Axes and spindles
10-349
Siemens AG, 2003. All rights reserved
SINUMERIK 840Di Manual (HBI) – 06.03 Edition
The zero mark monitoring of the encoder of a machine axis checks whether
pulses were lost between two zero mark passes.
MD 36310: ENC_ZERO_MONITORING (zero mark monitoring)
is used to enter the number of detected zero mark errors at which the
monitoring is to respond.
Special feature:
A value of 100 will additionally disable the hardware monitoring of the encoder.
Error response
Alarm: 25020 Zero mark monitoring”
and stopping the machine axes using a speed setpoint ramp whose
characteristic is set in
MD36610: AX_EMERGENCY_STOP_TIME (time of brake ramp in case of
error conditions).
Error causes/remedy
MD36300: ENC_FREQ_LIMIT
[
n
]
(encoder limit frequency) set too high
Encoder cable damaged
Encoder or encoder electronics defective.
It is possible to switch over between the two possible encoders or position
measuring systems of a machine axis at any time. The permissible position
difference between the two position measuring systems is monitored.
MD 36500 ENC_CHANGE_TOL (maximum tolerance when switching over
the actual position value)
Error response
Alarm: “25100 Measuring system cannot be switched over”
The requested switchover to another encoder is not carried out.
Error causes/remedy
The specified permissible tolerance is too small
The position measuring system to which you will switch over is not
referenced.
The position difference between the two encoder or position measuring systems
of a machine axis is monitored with
MD36510 ENC_DIFF_TOL (measuring system synchronism tolerance)
Error response
Alarm: “25105 Measuring systems are not synchronous”
and stopping the machine axes using a speed setpoint ramp whose
characteristic is set in
MD36610: AX_EMERGENCY_STOP_TIME (time of brake ramp in case of
error conditions).
Encoder
zero mark
monitoring
Position tolerance
when switching over
the encoder
Cycl. monitoring of
encoder
position tolerance
10 NC Start-Up with HMI Advanced