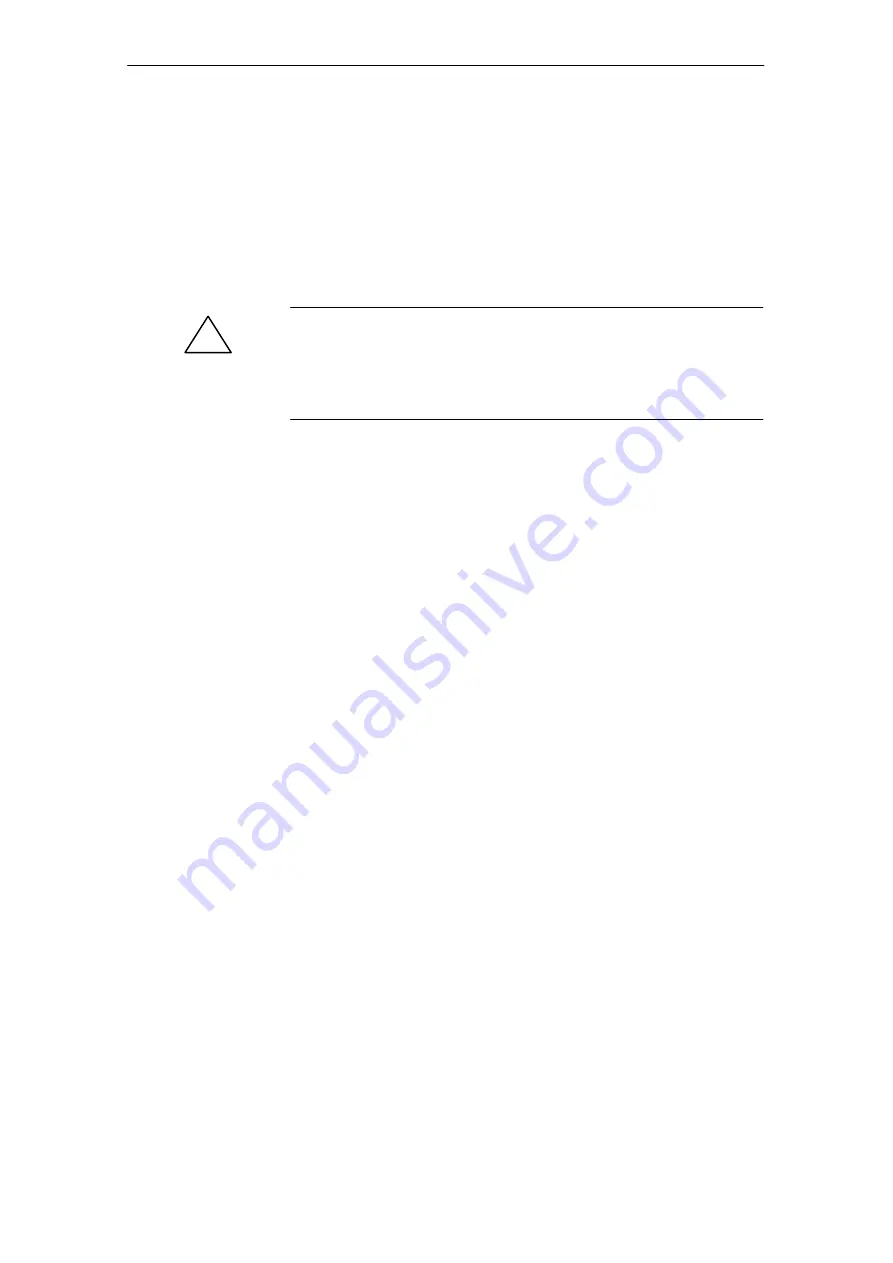
06.03
10.5 Axes and spindles
10-357
Siemens AG, 2003. All rights reserved
SINUMERIK 840Di Manual (HBI) – 06.03 Edition
– length measurement system equidirectional to the machine system:
Absolute offset =
machine actual po actual position of
the measuring system
– length measurement system opposite to the machine system:
Absolute offset =
machine actual position – actual position of
the measuring system
MD34090: REFP_MOVE_DIST_CORR (reference point/absolute offset)
!
Warning
After you have determined the absolute offset and made an entry in
MD34090: REFP_MOVE_DIST_CORR (reference point/absolute offset)
the position measuring system must be re-referenced.
/FB1/
Description of Functions, Basic Machine,
R1 Reference Point Approach
Section: Referencing with linear measurement systems
with distance-coded reference marks
Referencing of an axis with absolute encoders is carried out automatically when
the NC powers up if the corresponding axis is detected adjusted.
The following two requirements must be fulfilled:
The absolute encoder is adjusted.
Sign: MD 34210: ENC_REFP_STATE[n] = 2
The measuring system of the machine axis, which is active when the NC
powers up, uses the absolute encoder.
The acceptance of the absolute encoder is carried out without axis movement.
In the case machine axes are equipped with absolute encoders, the measuring
system is not synchronized by approaching a reference point, but it is adjusted.
When adjusting the axis, the actual value of the absolute encoder is matched
with the machine zero once during the start-up and then enabled.
The adjustment can be carried out in three different ways:
Operator-assisted adjustment
Automatic adjustment with probe
Adjustment with BERO.
Any other kinds of referencing with absolute encoders will not be supported.
References
Absolute encoder
Adjustment
10 NC Start-Up with HMI Advanced