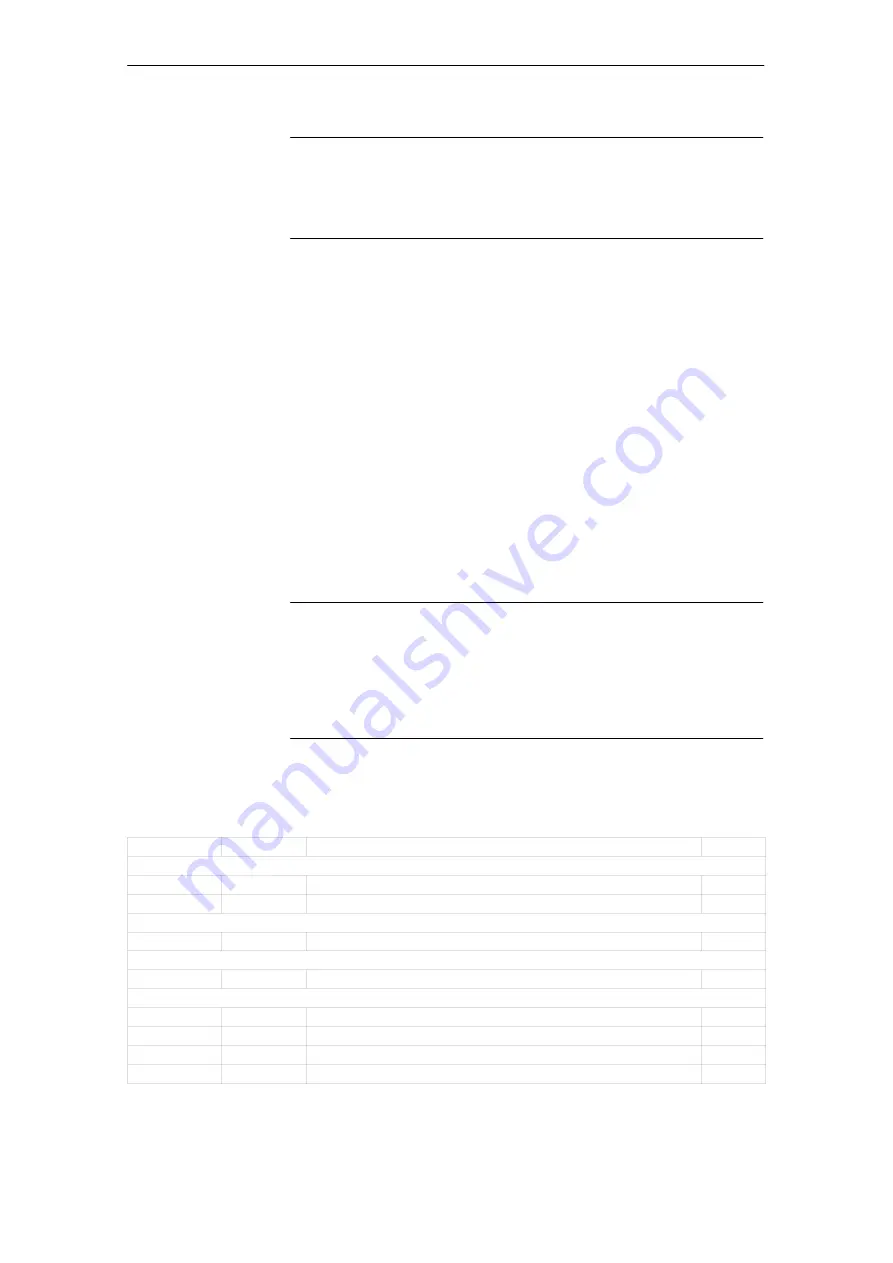
06.03
10.5 Axes and spindles
10-359
Siemens AG, 2003. All rights reserved
SINUMERIK 840Di Manual (HBI) – 06.03 Edition
Notice
The axis will not move if the traversing key is pressed!
The value entered in MD34100: REFP_SET_POS[n] (ref. point value) is dis-
played on the actual-value display of the appropriate traversing key.
8. The adjustment of the absolute encoder of this machine axis is thus com-
pleted.
For time-optimized adjustment of several machine axes, the following procedure
is recommended:
1. Traverse all or several machine axes (as far as permitted by the machine
design) to the adjustment point (see above, Points 1 – 5).
2. Switch over to: JOG/REF mode (Point 6).
3. Carry out the adjustment for each machine axis (Point 7).
A readjustment of the absolute encoder is required:
after dismantling/installing the encoder or the motor with absolute encoder
or,
if data are lost in the NC SRAM, battery voltage failure, PRESET,
in the case of gear change between load and absolute encoder.
Notice
The status in
MD34210: ENC_REFP_STATE[n] (status of absolute encoder)
is only reset by the NC automatically in the case of gear change.
In all the other cases, the user must reset the status to 0 = “Encoder not ad-
justed” by himself/herself and provide for readjustment.
Table 10-39
Referencing: Interface signals
DB number
Bit, Byte
Name
Ref.
Mode group-specific
Signals from PLC to mode group
11, ...
0.7
Mode group reset
K1
11, ...
1.2
Machine function REF
K1
Mode group-specific
Signals from mode group to PLC
11, ...
5.2
Active machine function REF
K1
Channel-specific
Signals from PLC to channel
21,...
1.0
Activate referencing
Channel-specific
Signals from channel to PLC
21,...
28.7
(MMC –––> PLC) REF
K1
21,...
33.0
Referencing active
21,...
35.7
Reset
K1
21,...
36.2
All axes to be referenced are referenced.
Adjusting several
axes
Readjustment
Interface signals
10 NC Start-Up with HMI Advanced