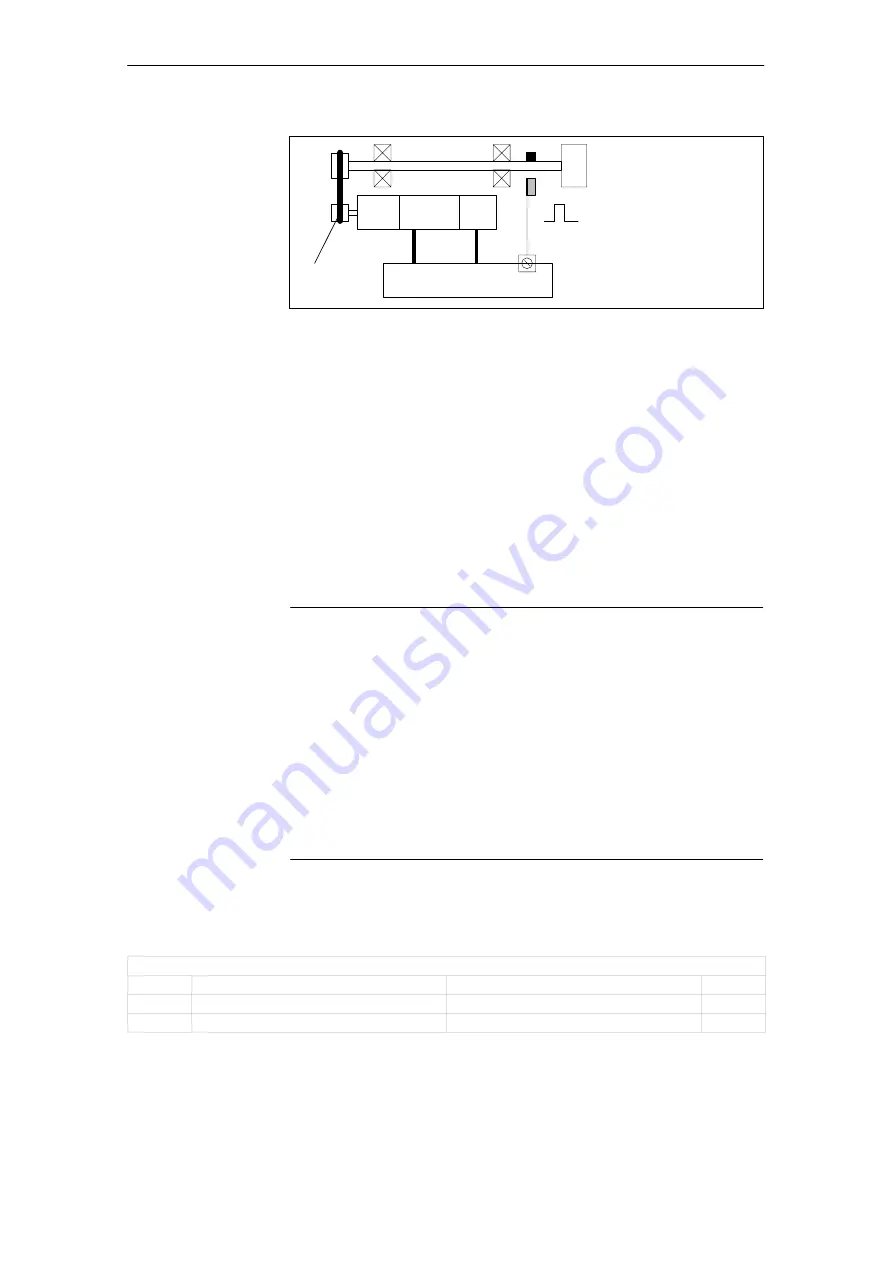
06.03
10.5 Axes and spindles
10-372
Siemens AG, 2003. All rights reserved
SINUMERIK 840Di Manual (HBI) – 06.03 Edition
Motor
Motor
encoder
SIMODRIVE 611 universal
Chuck
BERO
Power
connection
Motor en-
coder cable
gearbox
Toothed belt
Fig. 10-31 Synchronization using BERO
The spindle will be synchronized:
after the NC has powered up when the spindle is moved using a
programming command
after request for resynchronizing from the PLC
IS DB31,... DBX16.4 (resynchronize spindle 1)
IS DB31,... DBX16.5 (resynchronize spindle 2)
after each gear stage change when an indirect measuring system is used
MD 31040: ENC_IS_DIRECT (direct measuring system) = 0
when the encoder cut-off frequency falls below the programmed value after
a speed has been programmed which is above the encoder cut-off fre-
quency.
Notice
To synchronize the spindle, it must always be rotated using a programming
command (e.g. M3, M4, SPOS). The specification of a spindle speed using
the direction keys of the machine control panel is not sufficient.
If the spindle encoder is not mounted directly on the spindle and there are
speed-transforming gears between the encoder and spindle (e.g.
motor-mounted encoder), then a BERO signal connected to the drive
module must be used for synchronization.
The control then automatically resynchronizes the spindle after each gear
change. No manual intervention is required on the part of the user.
In general, backlash, gearbox elasticity and proximity switch hysteresis re-
duce the accuracy achievable during synchronization.
Table 10-45
Synchronizing spindle: Machine data
Axis-specific ($MA_ ...)
34100
REFP_SET_POS
Reference point value
34090
REFP_MOVE_DIST_CORR
Reference point offset
34200
REFP_MODE
Referencing mode
When is
synchronization
necessary?
Machine data
10 NC Start-Up with HMI Advanced