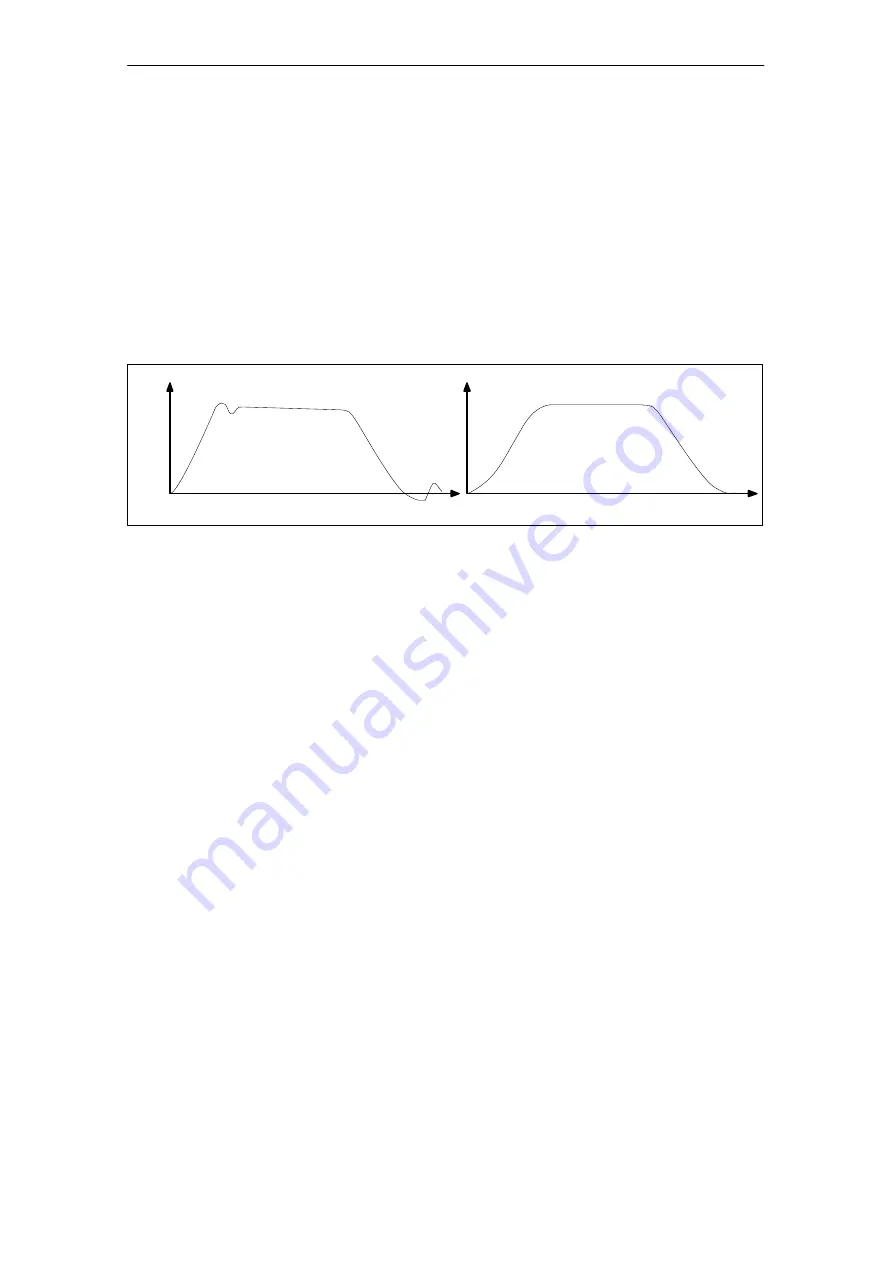
06.03
10.5 Axes and spindles
10-334
Siemens AG, 2003. All rights reserved
SINUMERIK 840Di Manual (HBI) – 06.03 Edition
If a K
V
factor is already known for the machine in question, this can be set and
checked. For checking, reduce the acceleration of the axis in
MD32300: MAX_AX_ACCEL (axis acceleration)
to make sure that the drive does not reach its current limit when accelerating
and decelerating.
The K
V
factor must also be checked for high speeds of the rotary axis and
spindle (e.g. for spindle positioning, tapping).
The approach behavior at various speeds can be checked by means of a
storage oscilloscope or the HMI Advanced servo trace software. The check is
made on the basis of the speed setpoint.
n
set
[V]
t [msec]
n
set
[V]
t [msec]
“Poor”
Selected Kv factor
“Good”
Selected Kv factor
Fig. 10-19 Speed setpoint curve
No overshoots may occur while the drive is approaching the static statuses; this
applies to all speed ranges.
The reasons for an overshoot in the control loop can be:
Acceleration too high (current limit is reached)
Error in speed controller (reoptimization necessary)
Mechanical backlash
Mechanical components canted.
For safety reasons set the K
V
factor to a little less than the maximum possible
value.
The real K
V
factor must precisely match that set because monitoring functions
are derived from the K
V
factor that would otherwise respond (e.g. contour
monitoring).
The machine axes are accelerated and decelerated at the acceleration entered
in
MD 32300: MAX_AX_ACCEL (axis acceleration)
This value should allow the axes to be accelerated and positioned rapidly and
accurately while ensuring that the machine is not unduly loaded.
The default values of the acceleration are in the range from 0.5 m/sec
2
to 2 m/
sec
2
Checking the
servo gain
Overshoot in the
control loop
Acceleration
Default values
10 NC Start-Up with HMI Advanced