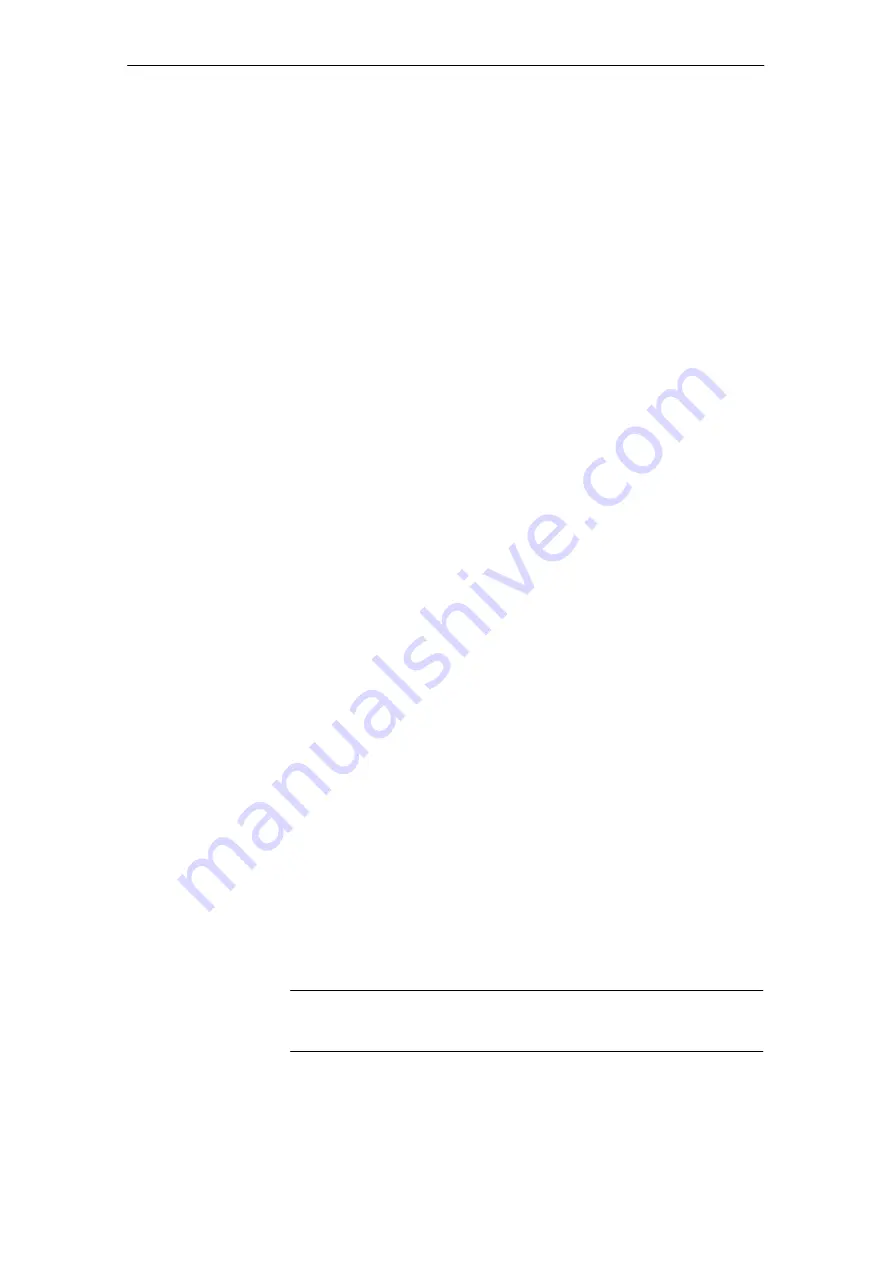
06.03
10.5 Axes and spindles
10-348
Siemens AG, 2003. All rights reserved
SINUMERIK 840Di Manual (HBI) – 06.03 Edition
and stopping the machine axis using a speed setpoint ramp whose
characteristic is set in
MD36610: AX_EMERGENCY_STOP_TIME (time of brake ramp in case of
error conditions).
Error causes/remedy
Contour errors are due to signal distortions in the position-control loop.
Remedy:
Enlarge tolerance band
Check the Kv factor.
The real servo gain must correspond to the desired servo gain set by MD
32200: POSCTRL_GAIN
[
n
]
.
HMI Advanced
Operating area: DIAGNOSIS > Service displays > Service of axis
Check optimization of speed controller
Check easy movement of axes
Check machine data for traversing movements
(feed override, acceleration, max. speeds, ...)
When operating with feedforward control:
MD 32810: EQUIV_SPEEDCTRL_TIME (equivalent time constant of speed
control loop for feedforward control)
If the machines are set too inexactly, MD 36400: CONTOUR_TOL must be
increased.
Monitoring of the cut-off frequency of the encoder of a machine axis.
MD 36300: ENC_FREQ_LIMIT (encoder cut-off frequency)
Error response
Alarm: “21610 Encoder frequency exceeded”
IS: DB31, ... DBX60.2 “Encoder cut-off frequency exceeded 1”
IS: DB31, ... DBX60.3 “Encoder cut-off frequency exceeded 2”
and stopping the machine axis using a speed setpoint ramp whose
characteristic is set in
MD36610: AX_EMERGENCY_STOP_TIME (time of brake ramp in case of
error conditions).
Error causes/remedy
The position control resumes automatically after the axes have stopped.
Notice
The axis concerned must be re-referenced.
Encoder
cut-off frequency
monitoring
10 NC Start-Up with HMI Advanced