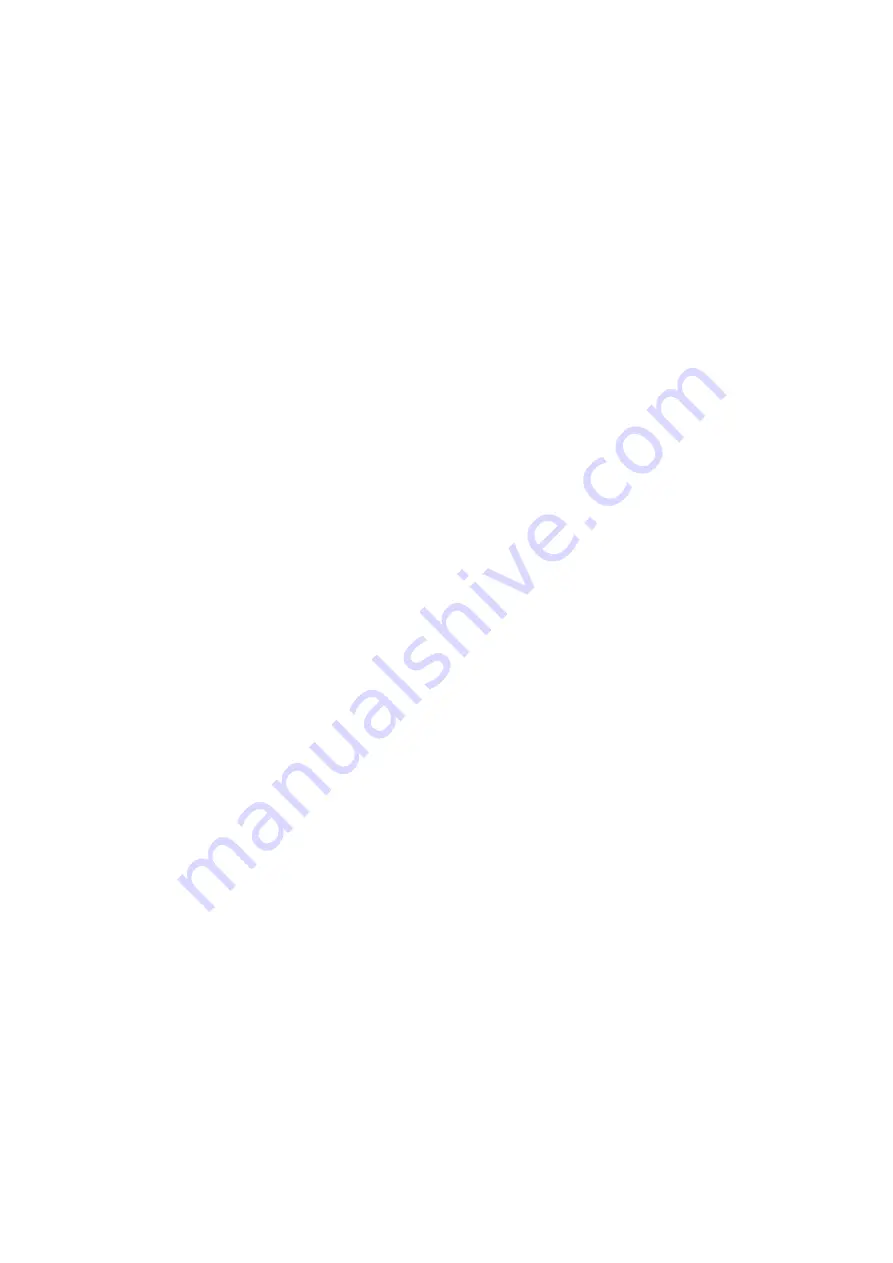
SIPART PS2 with PROFIBUS communication
Operating Instructions, 09/2007, A5E00127926-07
17
Description
3
3.1
Function
●
The electropneumatic positioner and an actuator form a control system. The current
position of the actuator is recorded by a servo potentiometer and the actual value x is fed
back. The setpoint and the actual value are simultaneously shown on the digital display.
●
The reference variable w is provided digitally through the PROFIBUS.
●
The positioner works as a predictive, anticipatory five-point controller whose output
variable ±Δy is used to control the integrated servo valves based on the pulse length
modulation method.
●
These input signals change pressure in the actuator chamber(s) and displace the
actuator until the control deviation becomes zero.
●
When the enclosure cover has been removed, the device can be operated and
configured using three buttons and the digital display.
●
The standard controller has one binary input (BE1) by default. This binary input can be
configured individually, and be used to block the operating modes.
●
It has a friction clutch and a switchable gear so that the positioner can be used with
different mechanical part-turn and linear actuators.
3.2
Structure
3.2.1
Design overview
The mechanical and electrical assembly, the device components and functional principle of
the positioner are described in the following chapter.
The positioner and the PROFIBUS PA communication interface function as components in a
digital process automation system. It functions as a slave and communicates with the master
through the PROFIBUS PA fieldbus. Apart from communication, the fieldbus also supplies
electrical auxiliary power to the positioner.
The positioner is available in the following configurations:
●
SIPART PS2 PA without explosion protection in the metal or plastic enclosure
●
SIPART PS2 PA with EEx ia/ib protection in the metal or plastic enclosure
●
SIPART PS2 PA with EEx d protection in the flameproof enclosure