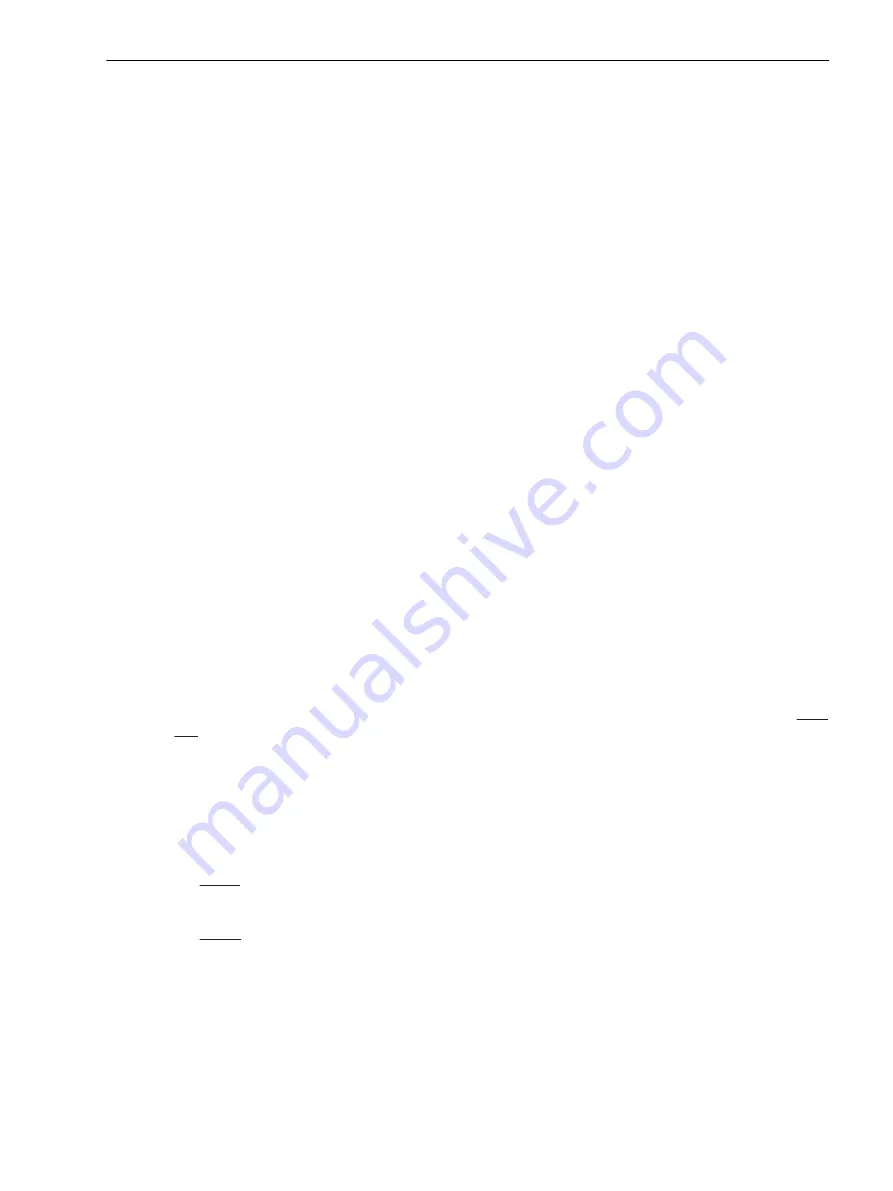
•
Vector jump protection Δφ
•
Fast threshold supervision of the voltages (U>; U<)
Control Functions
The device is equipped with control functions which operate, close and open, switchgear via the integrated
operator panel, the system interface, binary inputs, and using a personal computer with DIGSI software.
The status of the primary equipment can be transmitted to the device via auxiliary contacts connected to
binary inputs. The present status (or position) of the primary equipment can be displayed on the device, and
used for interlocking or plausibility monitoring. The number of the operating equipment to be switched is
limited by the binary inputs and outputs available in the device or the binary inputs and outputs allocated for
the switch position indications. Depending on the primary equipment being controlled, one binary input
(single point indication) or two binary inputs (double point indication) may be used for this process.
The capability of switching primary equipment can be restricted by a setting associated with switching
authority (Remote or Local), and by the operating mode (interlocked/non-interlocked, with or without pass-
word request).
Processing of interlocking conditions for switching (e.g. system interlocking) can be established with the aid of
integrated, user-configurable logic functions.
Messages and Measured Values; Fault Recording
The indication list provides information about conditions in the power system and the device. Measurement
quantities and values that are calculated can be displayed locally and communicated via the serial interfaces.
Device messages can be allocated to a number of LEDs, externally processed via output contacts, linked with
user-definable logic functions and/or issued via serial interfaces.
During a generator or network fault (fault in the power system), important events and state changes are
stored in a fault annunciation buffer. The instantaneous or rms measured values during the fault are also
stored in the device and are subsequently available for fault analysis.
Communication
Serial interfaces are available for the communication with operating, control and memory systems.
Front Interface
A 9-pin DSUB socket on the front panel is used for local communication with a personal computer. By means
of the SIPROTEC 4 operating software DIGSI, all operational and evaluation tasks can be executed via this oper-
ator interface, such as specifying and modifying configuration parameters and settings, configuring userspe-
cific logic functions, retrieving operational and fault messages and measured values, readout and display of
fault recordings, querying of devices statuses and measured values.
Rear Interfaces
Depending on the individual ordering variant, additional interfaces are located at the rear side of the device.
They serve to establish an extensive communication with other digital operating, control and memory compo-
nents:
The service interface can be operated via electrical data lines and also allows communication via modem. For
this reason, remote operation is possible via personal computer and the DIGSI operating software, e.g. to
operate several devices via a central PC.
The system interface ensures the central communication between the device and the substation controller. It
can be operated via data lines or fibre optic cables. Several standard protocols are available for the data
transfer:
•
IEC 61850
An EN 100 module allows to integrate the devices into 100 Mbit Ethernet communication networks used
by process control and automation systems and running IEC 61850 protocols. In parallel to the process
control integration of the device, this interface can also be used for communication with DIGSI and for
inter-relay communication via GOOSE.
Introduction
1.2 Application Scope
SIPROTEC 4, 7VE61 and 7VE63, Manual
19
C53000-G1176-C163-3, Edition 10.2017
Summary of Contents for SIPROTEC 4 7VE61
Page 8: ...8 SIPROTEC 4 7VE61 and 7VE63 Manual C53000 G1176 C163 3 Edition 10 2017 ...
Page 24: ...24 SIPROTEC 4 7VE61 and 7VE63 Manual C53000 G1176 C163 3 Edition 10 2017 ...
Page 142: ...142 SIPROTEC 4 7VE61 and 7VE63 Manual C53000 G1176 C163 3 Edition 10 2017 ...
Page 192: ...192 SIPROTEC 4 7VE61 and 7VE63 Manual C53000 G1176 C163 3 Edition 10 2017 ...
Page 222: ...222 SIPROTEC 4 7VE61 and 7VE63 Manual C53000 G1176 C163 3 Edition 10 2017 ...
Page 230: ...230 SIPROTEC 4 7VE61 and 7VE63 Manual C53000 G1176 C163 3 Edition 10 2017 ...
Page 256: ...256 SIPROTEC 4 7VE61 and 7VE63 Manual C53000 G1176 C163 3 Edition 10 2017 ...
Page 314: ...314 SIPROTEC 4 7VE61 and 7VE63 Manual C53000 G1176 C163 3 Edition 10 2017 ...
Page 316: ...316 SIPROTEC 4 7VE61 and 7VE63 Manual C53000 G1176 C163 3 Edition 10 2017 ...
Page 330: ...330 SIPROTEC 4 7VE61 and 7VE63 Manual C53000 G1176 C163 3 Edition 10 2017 ...