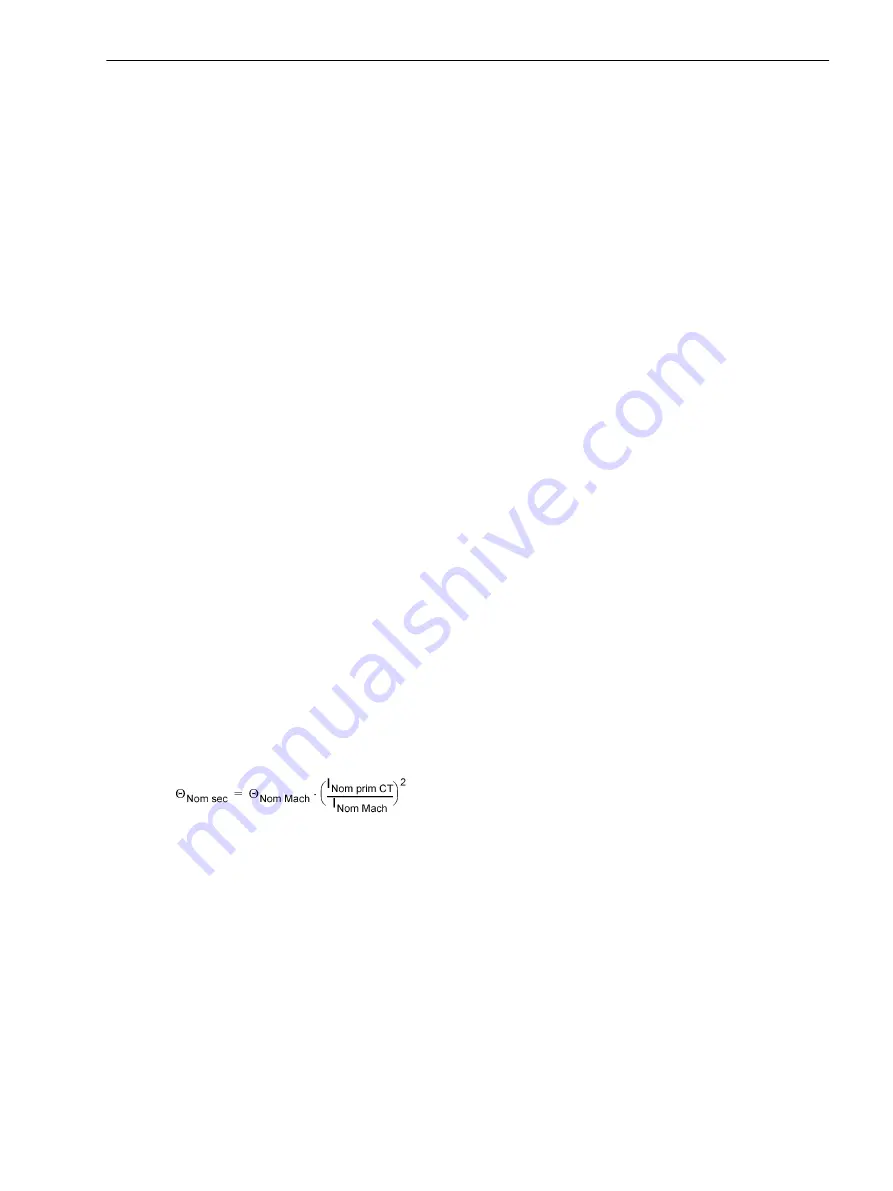
this threshold is undershot, tthe tripping command will be reset and the protected equipment can be switched
on again.
The thermal element level is given in % of the tripping overtemperature.
A current warning level is also available (parameter 4205
I ALARM
). The setting is set as the secondary
current in A (mperes) and should be equal to or slightly less than the permissible current k ·
Ι
Nom sec
. It can be
used instead of the thermal warning element by setting the thermal warning element to 100 % thus virtually
disabling it.
Extension of Time Constants
TIME CONSTANT
set in address 4203 is valid for a running motor. When a motor without external cooling is
running down or at standstill, the motor cools down more slowly. This behavior can be modeled by increasing
the time constant by factor
Kτ-FACTOR
, set at address 4207. Motor stop is detected if the current falls below
the threshold value
BkrClosed I MIN
of the current flow monitoring (see side title "Current Flow Moni-
toring" in Subsection
). This understands that the motor idle current is greater than this
threshold. The pickup threshold
BkrClosed I MIN
affects also the following protection functions: voltage
protection and restart inhibit for motors.
If no differentiation of the time constants is necessary (e.g. externally-cooled motors, cables, lines, etc.) the
Kτ-FACTOR
is set at 1 (default setting value).
Dropout Time after Emergency Starting
The dropout time to be entered at address 4208
T EMERGENCY
must ensure that after an emergency startup
and after dropout of the binary input
>EmergencyStart
the trip command is blocked until the thermal
replica is below the dropout threshold again.
Ambient or Coolant Temperature
The specifications made up to now are sufficient to model the overtemperature. The ambient or coolant
temperature, however, can also be processed. This has to be communicated to the device as digitalized meas-
ured value via the interface. During configuration, parameter 142
49
must be set to
With amb. temp.
.
If the ambient temperature detection is used, the user must be aware that the
49 K-FACTOR
to be set refers
to an ambient temperature of 104° F or 40° C, i.e. it corresponds to the maximum permissible current at a
temperature of 104° F or 40° C.
Since all calculations are performed with standardized quantities, the ambient temperature must also be
standardized. The temperature at nominal current is used as standardized quantity. If the nominal current
deviates from the nominal CT current, the temperature must be adapted according to the formula following.
In address 4209 or 4210
49 TEMP. RISE I
the temperature adapted to the nominal transformer current is
set. This setting value is used as standardization quantity for the ambient temperature input.
[formel-maschinentemperatur-260602-kn, 1, en_US]
with
Θ
Nom sec
Machine temperatur at secondary nominal current = setting at the protection
device (address 4209 or 4210)
Θ
Nom Mach
Machine temperature at nominal machine current
Ι
NomCT prim
Nominal primary CT current
Ι
Nom Mach
Nominal current of the machine
If the temperature input is used, the tripping times change if the coolant temperature deviates from the
internal reference temperature of 104° F or 40° C. The following formula can be used to calculate the tripping
time:
Functions
2.11 Thermal Overload Protection 49
SIPROTEC 4, 7SJ62/64, Manual
177
C53000-G1140-C207-8, Edition 08.2016
Summary of Contents for SIPROTEC 4
Page 8: ...8 SIPROTEC 4 7SJ62 64 Manual C53000 G1140 C207 8 Edition 08 2016 ...
Page 18: ...18 SIPROTEC 4 7SJ62 64 Manual C53000 G1140 C207 8 Edition 08 2016 ...
Page 30: ...30 SIPROTEC 4 7SJ62 64 Manual C53000 G1140 C207 8 Edition 08 2016 ...
Page 540: ...540 SIPROTEC 4 7SJ62 64 Manual C53000 G1140 C207 8 Edition 08 2016 ...
Page 594: ...594 SIPROTEC 4 7SJ62 64 Manual C53000 G1140 C207 8 Edition 08 2016 ...
Page 720: ...720 SIPROTEC 4 7SJ62 64 Manual C53000 G1140 C207 8 Edition 08 2016 ...