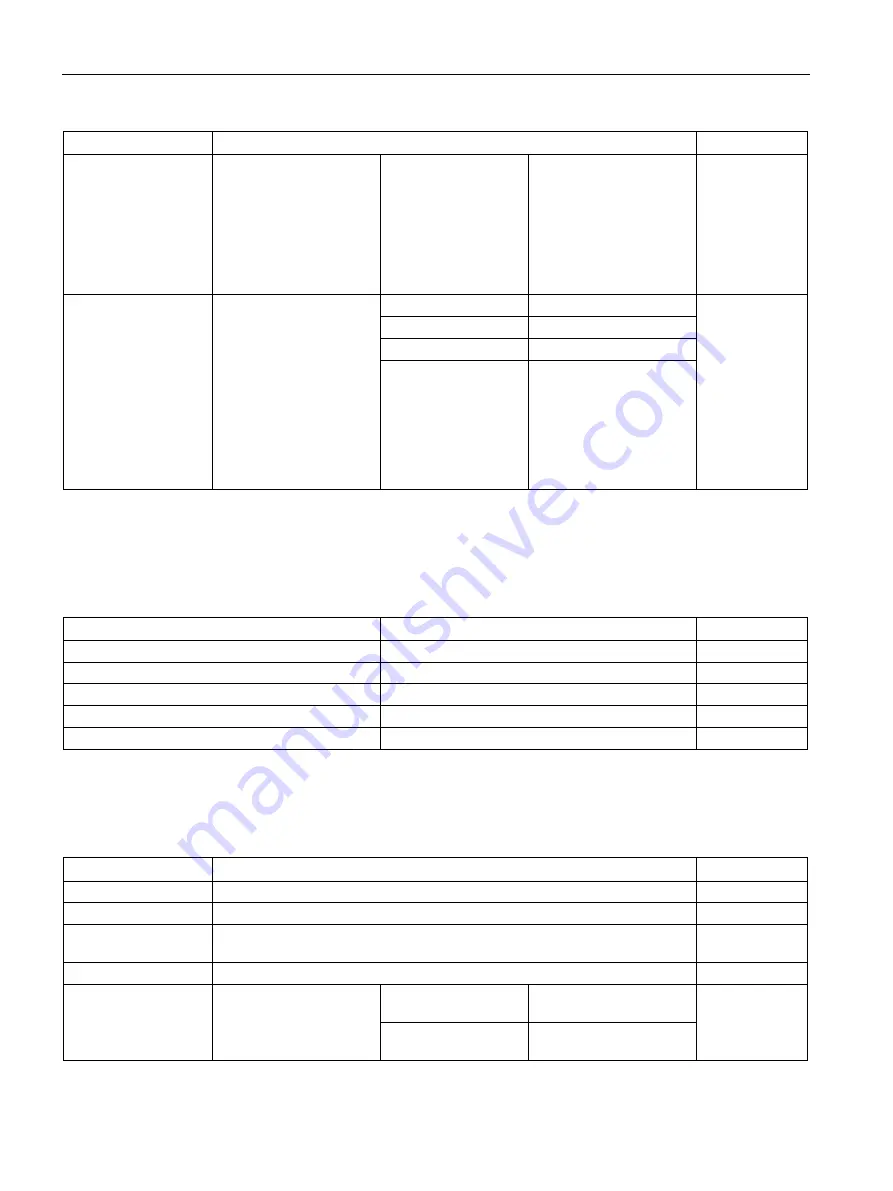
Engineering and remote access
7.6 Cyclic and acyclic data
PSU8600power supply systems
218
Manual, 04.2016, A5E35883207-7-76
Data
Description
Data type
•
Bit0/1: OK
•
Bit2/3: Channel1
•
Bit4/5: Channel2
•
Bit6/7: Channel3
•
Bit8/9: Channel4
•
Bit10-15: unused = 0
3
LED lit yellow
LED state
Actual display status of
the LEDs. Each LED is
represented by 2 bits:
•
Bit0/1: OK
•
Bit2/3: Channel1
•
Bit4/5: Channel2
•
Bit6/7: Channel3
•
Bit8/9: Channel4
•
Bit10-15: unused = 0
0
LED is off
Unsigned16
1
LED lights up
2
LED flashes at 1 Hz
3
LED flashes at 2 Hz
7.6.2.4
Data sets SITOP BUF8600
Index 0x0006: Device information (reading)
Data
Description
Data type
MLFB / Order number
Article No. / Order number
VisibleString(20)
Product state
Product release
Unsigned8
Fill byte(s)
-
Unsigned8
SW version
Software version
Unsigned32
Serial number
Serial number
VisibleString(16)
Index 0x0020: State information (reading)
SITOP BUF8600 100 ms/40 A and SITOP BUF8600 300 ms/40 A
Data
Description
Data type
Fill byte(s)
-
Unsigned16
Fill byte(s)
-
Unsigned16
Charging current
[10mA]
Charge current
Unsigned16
Load current [10mA]
Load current
Unsigned16
Module operation state Operating state
0 = Off
Buffer component is in the
"Off" operating state.
Unsigned8
1 = Boot
Buffer component is pow-
ering up.
Summary of Contents for SITOP BUF8600
Page 6: ...Overview PSU8600power supply systems 6 Manual 04 2016 A5E35883207 7 76 ...
Page 12: ...Safety instructions PSU8600power supply systems 12 Manual 04 2016 A5E35883207 7 76 ...
Page 246: ...Environmental conditions PSU8600power supply systems 246 Manual 04 2016 A5E35883207 7 76 ...
Page 250: ...Environment PSU8600power supply systems 250 Manual 04 2016 A5E35883207 7 76 ...