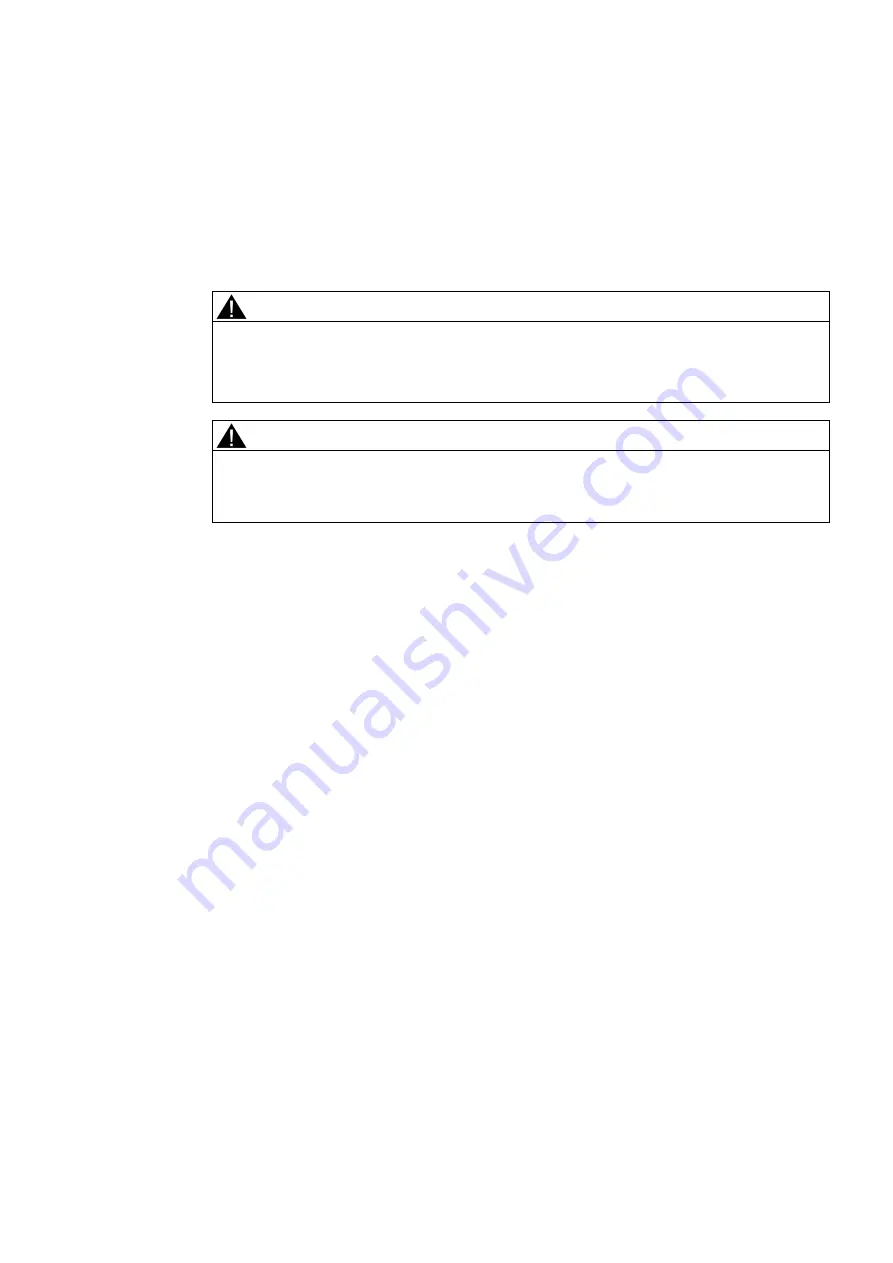
5
Commissioning
WARNING
Danger of severe injuries caused by the unintentional starting of the drive unit
Secure the drive unit to prevent it from being started up unintentionally.
Attach a warning notice to the start switch.
WARNING
Incorrect disposal of used oil is a threat to the environment and health
Remove any oil spillage immediately with an oil-binding agent in compliance with
environmental requirements.
Procedure
After mounting, the geared motor is ready for use.
1.
Run the geared motor for a short period of time under no-load operation.
2.
Check for any irregularities such as oil leakages, strong vibration and noise.
3.
Switch in the load.
You have now started up the geared motor.
BA 2012
Operating Instructions, 03/2013, 70000004024300
31
Summary of Contents for Worm Gearbox S 5 BA 2012
Page 1: ...Answers for industry MOTOX MOTOX Worm Gearbox S BA 2012 Operating Instructions 03 2013 ...
Page 2: ......
Page 34: ...Commissioning BA 2012 32 Operating Instructions 03 2013 70000004024300 ...
Page 36: ...Operation BA 2012 34 Operating Instructions 03 2013 70000004024300 ...
Page 44: ...Disposal BA 2012 42 Operating Instructions 03 2013 70000004024300 ...
Page 53: ......